Sealing technology plays a decisive role in ensuring performance stability, reducing friction, and protecting components from environmental influences. High-performance seals are essential for extending the life of robotic joints, actuators, and automated systems.
Beyond Protection: How Advanced Sealing Solutions Are Enhancing Robotic Performance
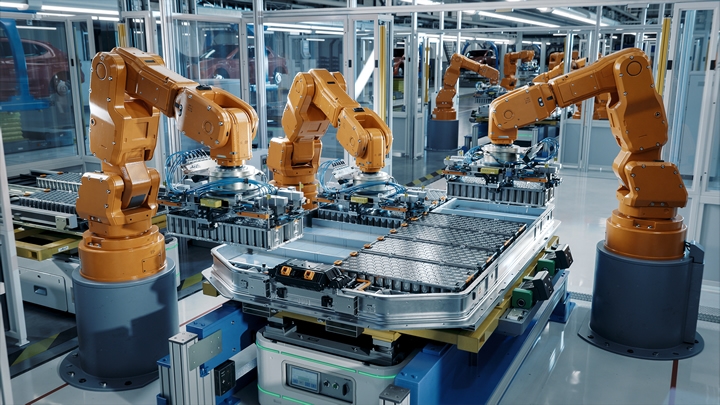
Article from | Freudenberg Sealing Technologies
From Friction Reduction to Advanced Materials: The Evolution of Sealing Technology
In modern robotics, reliability and efficiency depend on more than high-precision mechanics and intelligent control algorithms. Sealing technology plays a decisive role in ensuring performance stability, reducing friction, and protecting components from environmental influences. Often an afterthought, high-performance seals are essential for extending the life of robotic joints, actuators, and automated systems.
With robots now operating in increasingly extreme environments, traditional sealing solutions are reaching their limits. From high-speed industrial automation to outdoor applications in agriculture, energy, and logistics, sealing solutions must withstand aggressive chemicals, extreme temperatures, and constant exposure to contaminants. Freudenberg Sealing Technologies is addressing these challenges with Ingress Protection Seals for Robots (IPSR), a new generation of low-friction, highly durable sealing solutions engineered to extend service life and optimize robot performance.
Compact and durable: Ingress protection Seal for Robots (IPRS) for outdoor robotic applications
The Unique Challenges of Sealing Robotics
Unlike conventional industrial machinery, robotic systems experience dynamic, multi-directional motion, that places continuous stress on sealing components. Six-axis robots in automotive manufacturing perform high-speed movements while being exposed to cutting fluids, high temperatures, and metal debris. Autonomous mobile robots (AMRs) and AGVs navigate dusty, moisture-prone factory environments and require ingress protection without compromising mobility. Delta robots in semiconductor manufacturing demand extreme precision, where even microscopic seal degradation can result in unacceptable tolerances.
Outdoor robots face even greater challenges. Wind turbine maintenance robots operate in remote locations under extreme weather conditions, where seals must withstand high wind loads, temperature fluctuations, and UV exposure. Agricultural robots are exposed to constant vibration, chemically aggressive pesticides, and soil abrasion, all of which accelerate material degradation. Without advanced sealing solutions, these conditions increase maintenance requirements, reduce uptime, and compromise system reliability.
In conjunction with these challenges, seals in industrial robotics often face complex installation requirements. Many robotic systems have limited space for seals, requiring ultra-compact designs that maintain high performance while fitting into tight geometries. The development of customized seal profiles ensures that robots can maintain high speeds and precision without compromising durability.
To meet these challenges, Freudenberg Sealing Technologies has developed IPSR technology, based on multi-layer elastomer formulations and an adaptive Z-shaped sealing geometry. Unlike traditional O-rings, IPSR seals dynamically compensate for axial and radial motion, reducing friction while ensuring maximum resistance to contaminants. This load-distributing design extends the service life of robotic joints while minimizing energy loss.
IPSRs are also designed to operate reliably under varying lubrication conditions. Some robotic applications, particularly in outdoor environments, face inconsistent lubrication due to long service intervals or exposure to dirt and contaminants. By optimizing material properties, IPSR seals maintain their effectiveness even when lubrication levels fluctuate, providing consistent protection and reducing the risk of unexpected failure.
Advanced Material Science: New Frontiers in Sealing Performance
Material innovation is a key factor in the next generation of robotic seals. Freudenberg Sealing Technologies has developed advanced elastomers and engineered polymers that push the boundaries of chemical resistance, thermal stability, and mechanical durability.
One of the most significant breakthroughs is Fluoroprene XP, a proprietary elastomer designed to resist industrial lubricants, aggressive cleaners, and solvents. It is particularly well-suited for robotic systems in food processing, pharmaceutical, and semiconductor manufacturing industries, where exposure to disinfectants and process chemicals can rapidly degrade conventional sealing materials.
For applications that require flexibility at extreme temperatures, EPDM-based seals offer superior cold-weather-performance while maintaining structural integrity in high-humidity environments. This makes them ideal for logistics automation and warehouse robotics, where temperature fluctuations and condensation pose challenges for long-term reliability.
To optimize friction management, the engineering team applies solid-film lubricant coatings that minimize stick-slip effects and improve motion efficiency. This technology is especially critical in high-speed automation, where excessive friction generates heat and accelerates wear on mechanical components.
Reducing friction not only improves longevity but also has a direct impact on the energy efficiency of robotic systems, an essential factor in battery-operated AMRs and other mobile robots that require optimized power consumption.
Simulation-Driven Engineering for Optimized Sealing Performance
To develop high-performance sealing solutions, Freudenberg Sealing Technologies relies on extensive finite element analysis (FEA) simulations. These computational models allow engineers to evaluate friction coefficients, contact pressure distribution, and material deformation under dynamic load conditions prior to physical prototyping.
By using predictive modeling, Freudenberg engineers can refine seal geometries to reduce mechanical fatigue, optimize load distribution, and enhance wear resistance. This simulation-driven approach ensures that IPSR seals and other advanced sealing solutions meet the rigorous demands of today’s robotic applications.
In addition to optimizing mechanical performance, FEA simulations play a key role in evaluating the chemical resistance and aging behavior of sealing materials. This is particularly important for applications in chemically aggressive environments, such as semiconductor processing or heavy-duty industrial robotics, where exposure to reactive substances can accelerate seal degradation.
Sealing solutions tailored for the complex movements of six-axis robots
Application-Specific Sealing Solutions for Robotics
Different robotic applications require customized sealing solutions that balance durability, flexibility, and efficiency.
For six-axis industrial robots, which operate in automotive, aerospace, and electronics manufacturing, seals must withstand continuous high-speed articulation, exposure to cutting fluids, and mechanical stress. The company’s Premium Sine Seals (PSS) incorporate reinforced PTFE liners and elastomer composites for extended wear life and reduced energy consumption.
SCARA robots, widely used in precision assembly and electronics production, require high accuracy motion cycles. The Modular Plastic Sealing Concept (MPSC) combines sealing, bearing support, and vibration damping in a lightweight and durable structure to improve precision and durability.
Compact, low-friction seals to support SCARA speed and accuracy
Delta robots, frequently used in food and pharmaceutical automation, must comply with strict hygiene regulations. Freudenberg Sealing Technologies’ FDA-compliant fluoropolymer seals maintain high sealing performance under CIP (Cleaning-In-Place) and SIP (Sterilization-In-Place) conditions, ensuring long-term resistance to aggressive sanitation procedures.
Hygiene-focused sealing solutions for Delta robots in food and pharma automation
For AGVs and AMRs, seals must withstand abrasive particles, mechanical vibration, and exposure to industrial cleaning chemicals. The company’s PTFE-based seal designs provide long-term ingress protection while maintaining low rolling resistance, ensuring optimal battery efficiency in autonomous robotic systems.
Sealing in Collaborative Robotics and Human-Robot Interaction
In collaborative robotics, where humans and robots work side by side, sealing solutions must go beyond traditional ingress protection. The interaction between robot joints and actuators requires ultra-low-friction seals to ensure smooth and precise movements without sudden jerks or resistance. Freudenberg Sealing Technologies has optimized its sealing materials and coatings to eliminate stick-slip effects, enabling consistent force control and highly responsive motion dynamics. This is particularly important in applications such as robotic-assisted surgery, exoskeletons, and precision assembly lines, where even small inconsistencies in motion can compromise safety and performance. By integrating low-friction elastomers with self-lubricating properties, sealing solutions improve both efficiency and ease of use, ensuring that robots can seamlessly adjust force and motion when interacting with humans.
Sealing as a Competitive Advantage in Robotics
Sealing technology plays a critical role in maximizing the efficiency, reliability, and longevity of robotic systems. By developing advanced materials, optimizing sealing geometries through simulation, and developing application-specific solutions, Freudenberg Sealing Technologies is enabling robots to perform better in a wide range of industries.
As robotics continues to expand into new and more demanding environments, sealing solutions must evolve to meet these challenges. With ongoing research into high-performance elastomers, low-friction coatings, and innovative seal designs, Freudenberg Sealing Technologies remains at the forefront of advancing robotic sealing technology.
The content & opinions in this article are the author’s and do not necessarily represent the views of RoboticsTomorrow
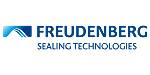
Freudenberg Sealing Technologies
Freudenberg Sealing Technologies is a proven supplier for demanding products and applications, and a development and service partner to customers in the automotive industries and in general industries. We apply 175 years of engineering and materials expertise. Then and now - we are focused on serving our customers' requirements and needs. Starting with the development of the Simmerring® radial shaft seal in 1929, Freudenberg Sealing Technologies has continuously expanded its industrial seals and component portfolio to include a range of technology solutions that address critical issues like performance, power, friction, emissions and material compatibility.
More about Freudenberg Sealing Technologies
Comments (0)
This post does not have any comments. Be the first to leave a comment below.
Featured Product
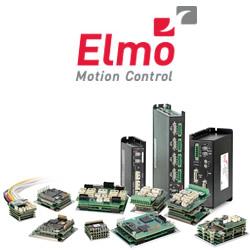