Some analysts assert that technological change is beneficial for all groups in our society, that the changes are more evolutionary than revolutionary in nature.
Contributed by | Seegrid
Beyond any notion of science fiction, ISO, the International Organization for standardization, defines an industrial robot as an automatically controlled, reprogrammable, multipurpose manipulator programmable in three or more axes. Leaders at Carnegie Mellon University have suggested that the field of robotics may be more practically defined as the study, design, and use of robot systems for manufacturing.
Typical applications of robots include: transportation, welding, painting, assembly, picking and placing products, packaging and palletizing, product inspection, and testing. All of these robotic tasks are accomplished with high endurance, speed, and precision.
Robots Taking Over the Plant Floor
Some industrial robots have increased flexibility regarding the positioning and orientation of the object on which they are operating, or even the overall task that has to be performed. Industrial robots often use precise guidance; many contain machine vision sub-systems linked to powerful computers or controllers. Artificial intelligence, which is still perceived as science fiction, is actually becoming an increasingly important factor in the modern day, more adaptable industrial robot. Industrial Truck Association President, Jeff Rufener, predicts that by 2025, fully automated and guided forklifts will account for 50% of industrial sales. The truth about robots, robotics, and functional uses is the purpose of this analysis. Putting all mythic notions aside, the state of robotics today has real-world applications, impacting employment, safety, quality, productivity, efficiency, and competitiveness.
Beyond any notion of science fiction, ISO, the International Organization for standardization, defines an industrial robot as an automatically controlled, reprogrammable, multipurpose manipulator programmable in three or more axes. Leaders at Carnegie Mellon University have suggested that the field of robotics may be more practically defined as the study, design, and use of robot systems for manufacturing.
Typical applications of robots include: transportation, welding, painting, assembly, picking and placing products, packaging and palletizing, product inspection, and testing. All of these robotic tasks are accomplished with high endurance, speed, and precision.
Robots Taking Over the Plant Floor
Most robots are designed to be a helping hand or a high-tech tool. They help people with tasks that would be difficult, unsafe, boring, or repetitive for a human to perform. The first industrial robots performed tasks that were, “Hot, Heavy, or Hazardous,” the three-H’s, performing tasks that were too difficult or too dangerous for people. Robots exhibit varying degrees of autonomous behavior; many robots are programmed to faithfully carry out specific repetitive actions without variation and with an extremely high degree of accuracy. These actions are determined by programmed routines that specify the direction, acceleration, velocity, deceleration, and distance of a series of coordinated motions. Sometimes they mimic the motions of humans exactly, and other times they improve upon it, moving faster, more precisely, or more smoothly than humans.
Some industrial robots have increased flexibility regarding the positioning and orientation of the object on which they are operating, or even the overall task that has to be performed. Industrial robots often use precise guidance; many contain machine vision sub-systems linked to powerful computers or controllers. Artificial intelligence, which is still perceived as science fiction, is actually becoming an increasingly important factor in the modern day, more adaptable industrial robot. Industrial Truck Association President, Jeff Rufener, predicts that by 2025, fully automated and guided forklifts will account for 50% of industrial sales.
According to Cathy Doe, in a presentation on robots in manufacturing, more than 90% of all robots used today are found in factories. These robots are referred to as the classical industrial robots. Ten years ago, nine out of ten robots were purchased by automotive companies. Today, 50% of robots manufactured are used by car manufacturers. Robots have made huge strides into warehouses, laboratories, energy plants, and hospitals. Robots are used to assemble products, handle dangerous materials, weld metal, spray finishes, inspect parts, fabricate components, assist in operating rooms, and even manage livestock. Robots are used for cutting and polishing as well as welding. The scope and range of robots and usage will continue to grow and expand. Ac- cepting this truth is based on embracing inevitable change.
Histrionics Versus History
The cry of the fearful has been that robots will be job killers, taking away good jobs from people in need of work. Even today, robots are frequently vilified and considered the cause for causal to high unemployment rates. The historical data does not substantiate these claims. In fact, the historical trends reflect job shifts rather than job elimination. The events of 9/11 created an agency which employs 50,000 security officers, inspectors, direc- tors, air marshals, and managers who protect the nation’s transportation systems so people can travel safely. TSA.gov is a direct response to a historical event that created jobs for people to look for bombs at checkpoints in airports, inspect rail cars, patrol subways with law enforcement partners, and work to make all modes of transportation safe.
Similarly, prior to the development of the highway and rail system in the United States, the need for barns, black- smiths, and covered wagons were significant and employed many people. New technologies have driven new job requirements and skills. The workforce has seen this before when blacksmiths became rare and steelmak- ing and railroad employment soared. The composition of the current workforce is changing rapidly due to the urgency and expectations that accompany these robotic technologies. In the 1970s and 80s when manufac- turing started to shift from the USA to Japan, Japan employed ten times as many robots as the USA with nearly zero unemployment. The utilization of robots, information processing and automation raises productivity, making companies more competitive globally, and increases their opportunities to grow and employ more workers. Com- panies that do not increase productivity become less competitive and MUST shed jobs to protect the bottom-line.
Scenario Planning: Robots Shift with Job Market
Will robots reduce the need for some warehouse workers and manufacturing plant floor employees? Yes, that is the truth. Will other jobs replace the functions assumed by robots? Yes, that also is the truth. Just as the re- quirements of the soldier of WWII was namely the ability to lift a certain weight and shoot a gun, today’s military personnel are highly trained, highly skilled, and adept beyond the imagination of Brokaw’s, “Greatest Generation” of warriors and American heroes. Today’s soldiers are needed more for their brains than brawn. The factory or warehouse worker of tomorrow will not be needed for the ability to lift heavy packages, but for the ability to find the most efficient way to satisfy the customers’ needs.
Role of Manufacturing Optimism
Manufacturers have played an important role in U.S. economic growth since the recession ended in 2009. Since then, the sector has added nearly 500,000 net new workers and provided an outsized role in its contributions to real gross domestic product (GDP). However, the stronger production activity experienced at the beginning of this year has slowed in recent months. While manufacturing production continues to expand, the pace of growth has eased. Challenges in Europe are one factor, with other uncertainties—including tax and regulatory policies facing businesses in 2013 and beyond—becoming a growing concern.
The most recent NAM/IndustryWeek Survey of Manufacturers noted that more than 83% of responding manu- facturers were either somewhat or very positive about their company’s outlook.
Manufacturers are cautiously optimistic about production and employment over the next 12 months. Industrial production is up 5.8% year-after-year, and the results of the NAM survey suggest 3 to 4% growth in industrial production. With modest economic growth in 2012, including real GDP expected to increase around 2.5%, manufacturing sales, employment, and capital spending should continue to expand in the coming months. Manufacturers anticipate 4.3% gains in sales over the next year on average. It is notable that half of the respon- dents said that their company’s sales are expected to grow by 5% or more.
IndustryWeek Executive Editor Steve Minter suggested other measures of manufacturing activity continue to expand. Capital spending and employment should increase by 2.5% and 1.9%, respectively, in the next 12 months. Nearly 20% of those completing the survey plan to increase capital spending over the next year by 10% or more. Meanwhile, on the employment front, more than one-third of manufacturers plan to hire up to 5% more workers.
Manufacturing wages are expected to rise by 1.8% over the next 12 months; 60% of respondents planned to provide raises of up to 3%, with another 20% planning wage increases between 3 and 5%. The manufacturing sector has benefitted tremendously from international trade, with almost 40% of the IndustryWeek respondents suggesting that overseas sales are one of their major drivers of future growth.
Robots Create More Jobs
The population in almost every developed nation is aging. People are living far beyond their retirement age. The multi-generational household is a thing of the past. This aging, retired, leisure seeking population will need more services and support. Instead of working at repetitive jobs moving boxes for meager wages, people will be employed to support, interact with, or care for the newly retired or elderly. Additionally, as productivity increases, there is more spending available for leisure activities such as travel, the arts, and outdoor activities; these will all drive new opportunities in businesses we are not even thinking about. Who would have believed five years ago the thousands of jobs created by the concept of “social networking”?
Other workers will be deployed to positions of greater efficiency, effectiveness, and optimized productivity. The shift in workforce needs is part of American history and will continue because we live in a dynamic society and social structure.
Robots are not the cause or blame for these workplace shifts. In fact, robotics has created an entire new work- force dynamic. Although difficult to quantify, Bureau of Labor Statistics data culled reveals that robotic compa- nies are employing more than one million Americans in the material handling, manufacturing, and best-practice plant management. A study conducted by Metra Martech, a market research firm, concluded 2 to 3 million jobs created in the world of manufacturing were due to robotics. Furthermore, Metra Martech foresees 700,000 to 1 million new jobs to be created by robots in the next four years.
According to Jerome A. Mark, in a paper prepared for the Bureau of Labor Statistics, “Studies indicate that the pace of technological change varies considerably by industry; affected workers are more likely to be transferred to new jobs. Technological change and its impact on the work force have become a focus of attention in the United States and abroad. The innovations include advanced communication systems, industrial robots, flex- ible manufacturing systems, computer-assisted design (CAD), and computer-assisted manufacturing (CAM). These modern technologies incorporate powerful and low-cost microelectronic devices that have the potential to increase productivity in office and factory production tasks. They share widespread appeal and are being diffused throughout the world. Some experts say that the pace of technological change is accelerating and that thousands of workers in plants and offices are affected as laborsaving innovations are diffused more widely. Some analysts assert that technological change is beneficial for all groups in our society, that the changes are more evolutionary than revolutionary in nature.”
Stressed Workforce Equals More Injuries: Robotics Solve Challenges of Increasing Demands on the Workforce
The single greatest source of workers’ comp claims comes from repetitive lifting, lowering, and moving of materials. Injuries and illness cost North American businesses $250 million each year according to The Millbank Quarterly. This amount does not include the costs incurred from fatalities. Robots automate those tasks significantly reducing the potential for injuries and costly downtime. Robots do not call in sick. Robots are not disgruntled; robots don’t file workers’ compensation claims or lawsuits.
As widely reported over the past several years, layoffs have swept through all industries including manfac- turing, service, retail, construction, office services, and trade industries. The Labor Department continues to report weakness in the labor market. Recent data shows that new workers’ compensation claims increase during recessionary periods even though the number of employees decrease and total work hours decline. The cost per claim and the total system costs also increase during these periods. Studies find that layoffs and changes in employment increase the duration of temporary total disability, higher permanent partial disability, and increased claims for occupational disease or cumulative injuries.
Robotic industrial tools and trucks are innovative products improving the health and welfare of material handling workers and manufacturing laborers. Reducing injuries improves not only the bottom-line for the employer, but the quality of life for the worker.
In production, “zero defects” is a frequent quality metric, but zero worker injuries, while a stated goal of most manufacturing plants and distribution centers, has not made it to the gold standard. There is no disputing that defective products cost companies millions of dollars in repairs, reshipments, and bad customer relations. Ironically, however, cost containment through fewer workers’ compensation claims, litigation, absenteeism, and employer reputation has a more significant impact on the bottom-line than all other quality initiatives combined.
Unlike traditional employees, industrial robots do not take scheduled breaks, eat lunch, talk to fellow co-workers, need smoke breaks, text on their cell phones, get sick, or take a vacation. Warehousing and manufacturing companies integrating industrial robots into their workflows see an increase in operational efficiency and profit- ability.
All employers will agree in principle that workforce health and safety is paramount and affects quality, yet, the documented physical labor processes in most companies continue to reveal that repetitive lifting, lowering, and moving injuries cost businesses millions of dollars each year. Automating those tasks with robotics significantly reduces the potential for injuries and downtime. One approach has been found for totally eliminating back inj- uries—robots. Robots do not eliminate the need for effective safety control programs and ergonomic design of work tasks, however, the elimination of costly injuries easily allows for justification of enterprise-wide purchases of robotic industrial equipment.
The National Safety Council documented that a disabling injury occurs every 1.3 seconds in the United States, more than 63,000 every day, and the Social Security Administration predicts that three out of ten workers enter- ing the workforce today will acquire some type of disability before they retire. Preventing these injuries is core to impact, quality, and productivity of the entire manufacturing environment, not just the individual who is harmed. With the introduction and adoption of robotics, industrial engineering professionals and corresponding shift man- agers are able to oversee operations focused on accomplishing on-time, accurate manufacturing and shipping deadlines.
The National Safety Council reports that a single work-related disabling injury costs an employer an average of $48,000. The National Council on Compensation Insurance estimates that medical costs account for nearly 60% of the overall costs of a lost-time claim, and the data is getting more alarming. Ironically, workers worried about keeping their jobs are more likely to file a claim, which may account for some of these increases.
Safety and Quality Should be Synonymous
A decade-long study by the Occupational Safety and Health Administration (OSHA), and noted in U.S. Depart- ment of Labor, Fact Sheet No. OSHA 89-09, concluded that back injuries are the nation’s number one workplace safety problem and that preventing them is a major workplace safety challenge. According to the Bureau of Labor Statistics, more than one million workers suffer from back injuries each year, and account for one of every five workplace injuries or illnesses. Further, one-fourth of all compensation indemnity claims involve back injuries, costing the industry billions of dollars on top of the pain and suffering borne by employees.
Documented standard operating procedures rarely include robotic lifting devices. Avoiding just one work-related injury claim would offset the costs of a fleet of robotic industrial trucks. Indeed cost-effective robotic lifting devices, which combine the best standard of durability and functionality with automatic lifting and lowering capabilities, are likely to have the greatest impact on quality, safety, and return on investment.
Whether used in deliveries, moving product in a warehouse, or on the manufacturing plant floor, quality robotic industrial trucks must be designed with proper ergonomics and safety in mind. The Millbank Quarterly reports the cost of back injuries is more than $250 billion annually; these injuries are avoidable. Eliminating these inju- ries should be part of what every C-level executive, human resources, safety and quality professional examines for continuous process improvement both today and every day.
Estimated Costs of Occupational Injuries and Illnesses and Estimated Impact on a Company’s Profitability Worksheet
OSHA and the Department of Labor provides a calculation tool for employers; the “$afety Pays” tool is a mecha- nism to assess the impact of occupational injuries and illnesses on profitability. This program uses a company’s profit margin, the average costs of an injury or illness, and an indirect cost multiplier to project the amount of sales a company would need to generate to cover those costs. The program raises awareness regarding oc- cupational injuries and illnesses as well as the impact on profitability.
Eliminating Waste and Measurement with Robotic Industrial Solutions
Manufacturing firms intent on capturing and distilling rich streams of data will find them. Companies will often look at an Excel capability maturity model (CMM) in rows and columns—a format common across many indus- tries and many applications. Most data dumped from a database ends up in a grid, whether it’s manufacturing or transactional data.
Each row may represent a part that is inspected, each column a dimension or reading. Most engineers see these data tasks as junk work that takes hours to prepare and maintain. One manufacturing executive reported that it took twenty-four PowerPoint slides to document this activity, including forty-three discrete steps, in two loops—one of seven steps, and one of nineteen steps.
Data collection can seem endless, yet Six Sigma’s moniker is to be data-driven; truth in the form of objec- tive statistical analysis of reliable data trumps personalities and politics. What companies require is real-time access to accurate, actionable data. Six Sigma teams often develop a list of critical-to-quality characteristics (CTQs) for a more efficient data collection-and-analysis system.
Statistical Process Control (SPC) is the ability to automate data collection and real-time alarms in all manufactur- ing processes. Use existing quality data-collection processes wherever possible, as well as better support for automatic gauging, and more transparent data sharing. Process owners must be able to respond instantly to process shifts or special cause variation.
Collected data is much more accessible, traceable, and reported most accurately with robots. Human reporting ALWAYS has a degree of subjectivity.
The entire value of the lean manufacturing principle does require real-time shop floor data. Improving overall equipment effectiveness (OEE), predictive and preventive maintenance, and quality initiatives across all industries is essential to lean effectiveness. Without real-time data reporting on the efficiency of the robots, companies are relegated to subjective, plant-floor reporting after each shift.
The Trouble with AGVs…High Risk at Too High a Price
Traditional automated guided vehicles (AGVs) are overkill for all but 2% of the entire industrial marketplace. The bells and whistles of these robots, while highly engineered, are at odds with the lean processes demanded in tight margin operations. AGVs are simply expensive automation, when most of the marketplace simply wants to find safe, effective, and affordable solutions to move product from point A to point B inside a plant or warehouse.
The solution that addresses the industry-demanded metrics, safety, effectiveness, and affordability is robotic industrial trucks which prove to drive better results. The decision-making process for a plant choosing AGVs is often more than one year. Plant interruptions occur to accommodate AGV installations. There is still a demand for driverless industrial robots to transport goods horizontally without wire, tape, laser, or other costly infrastruc- ture modifications to support AGV systems. The lead time to install an AGV is often greater than six months, whereas robotic industrial trucks can be in a plant or warehouse a week after ordered, providing the immediate benefit of unmanned trucks. The same time differential occurs at installation: six months or more for AGVs to be live and productive versus just one week for typical robotic industrial trucks (RITs).
YUSA Corporation, an early adopter of robotic industrial trucks, started investigating AGVs as an alternative solution to manned forklifts and pallet trucks for reducing labor costs and increasing productivity. The company found that AGV solutions on the market required significant investment for the AGVs as well as an ongoing investment for the addition and changes of routes due to lasers, tape, or buried wires the AGVs require.
Even the 2% of the manufacturing and warehouse executives who might want an AGV solution are choosing RITs because the time to break even on AGVs exceeds three years, rather than eight months for robotic indus- trial trucks. Positive cash flow is accomplished just over ten months with RITs, and shockingly more than five years with AGVs. Bottom-line, AGVs are not lean, nor best-practice.
Cultural Acceptance of Robotic Technology vs. AGVs
The best technology is ineffective if unused. Adoption of any new technology will meet with some resistance in any operation. New software, new equipment, new work schedules—new is not the status quo. Overcoming employee resistance is critical to ensuring use and adoption of new solutions. RITs are less threatening to the workforce and often meet far less resistance which directly impacts bottom-line improvements.
AGVs scare many workers because these purpose-built vehicles and systems require extensive pre-installation and are difficult to operate and work around. Robotic industrial trucks resemble standard pallet trucks and tow tractors with unmanned travel capabilities. Operators see RITs as much less of a threat because robots are built off familiar truck platforms, do not require extensive pre-installation, and work side-by-side with facility employees.
With robots performing repetitive job duties, operators are redeployed to value-added work functions that are greatly needed, challenging, and often result in pay raises due to increased responsibility.
Flexibility and Scalability Proves Advantage of Robots vs. AGVs
Due to the very long lead time required to design, install, deliver, and implement an AGV solution, there is very limited scalability possible. There is no, “try it, you’ll like it” mentality with an AGV decision. It’s all or nothing. It’s millions of dollars of high upfront costs and offers no flexibility.
The shift in RIT adoptions by some of the largest manufacturing and warehousing distribution centers is the ability to add robots as needed. High growth cycles can justify the purchase of additional robots without the multi-year forecasting for product demand. Because routes can be easily changed using RITs, and difficult to change with AGVs, there is additional flexibility achieved when new plant floor streamlined functionality is devel- oped. The additional ability for a single operator to interface with multiple robots creates maximized efficiency.
Facility Modifications Rule Out the Value of AGVs
Robots are set up in hours, not weeks or months. AGVs require months, even years, of planning for implemen- tation and installation. AGVs necessitate extensive IT integration, whereas RITs do not.
Any capital equipment purchase boils down to one question: How much risk is being assumed? The long-term, big-ticket price tag of automated guided vehicles is simply not worth the risk when functionality can be achieved with robotic industrial trucks without risk.
Nothing to Fear From Robots
Fear is an acronym: False Evidence Appearing Real. Robots are real, the evidence is real. Robots can help immediately in the transition to lean efficiency and cost-reductions. Perhaps ahead of his time, President Roos- evelt could have been referencing robots during his first inaugural address: “The only thing to fear is fear itself.” Robots are here, they are a force for positive change in society.
About Seegrid Corporation
Seegrid provides simple, affordable, flexible vision-guided automated guided vehicles (AGVs) to the material handling industry. Seegrid robotic industrial trucks, flexible AGVs, are revolutionizing the movement of materials in manufacturing and distribution environments. Seegrid automated pallet trucks, tow tractors, and walkie stackers optimize workflow processes by increasing productivity and reducing costs, creating economic and operational advantages. Robotic industrial trucks deliver a rapid return on investment, improve facility safety, and reduce equipment and product damage. Seegrid’s vision-guided technology transforms industrial vehicles into unmanned, automated pallet trucks, tow tractors, and walkie stackers that operate without the need for wire, laser, tape, or magnet. Fast Company magazine named Seegrid as one of the Top 50 World’s Most Innovative Company in 2013 and among the Top 10 World’s Most Innovative Robotics Company in 2013.
The content & opinions in this article are the author’s and do not necessarily represent the views of RoboticsTomorrow
Comments (0)
This post does not have any comments. Be the first to leave a comment below.
Featured Product
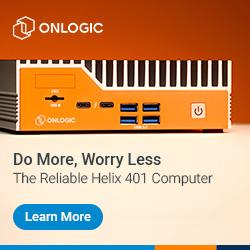