Glass processing, a real challenge!
LASYS 2014: Cutting glass with a laser avoids the need for rework - Use of USP lasers very much in vogue - Fast cutting speeds coupled with high quality
Glass, a fascinating material with its own peculiarities: "It is brittle and tends to crack during uneven heating on account of the tensions or temperature gradients which then occur," explained Thomas Wahl, Senior Developer for Lasers and Optics at Manz AG. "Glass and metals also differ considerably in their interaction with the laser beam due to absorption and thermal conduction," said Christof Siebert, Head of Industry Management for Micro Processing at Trumpf Laser- und Systemtechnik. Glass is transparent for visible light and has low thermal conductivity. It's exactly the opposite with metals. "The characteristic properties of glass," also concluded Dr. Boris Ruffing, Director European OEM/Industrial Sales at Newport Spectra-Physics, "represent a bigger challenge for laser systems and processes to achieve fast production speeds coupled with high quality." According to Ruffing, glass is not just glass. "There is a wide spectrum of parameters such as the composition of the material, the thickness, coatings and hardening methods which play a role here and pose additional challenges," added the expert.
Find solutions at the international trade fair LASYS 2014
Manufacturers of glass processing machines and laser systems are required more than ever to develop suitable methods which can cope with the characteristic properties of glass. "The use of lasers to inscribe glass and drill holes in glass is already well-established," said Norbert Höppe, Sales Manager for Laser System Technology at Reis Robotics, "whereas laser cutting and joining processes have still not been so intensively researched in many areas with glass unlike metals or plastics." An international trade fair such as LASYS 2014, which is specially geared towards laser processing of all kinds of materials, is precisely the ideal platform in this case. Visitors from the mechanical engineering, motor vehicle construction, electrical/electronics, metal working/ processing, optical, glass, semiconductors, plastics and medical technology industries will find answers and solutions at LASYS 2014 from 24 to 26 June 2014. LASYS 2014 will present the entire range of applications of lasers in material processing, as well as special and new application areas in Hall 4 at the Stuttgart Trade Fair Centre. Machines, processes and services will be the clear focal points of LASYS 2014. The trade fair will therefore provide an excellent opportunity to obtain detailed information on new cost-effective production methods and systems, e.g. on laser-based glass processing.
Forgery-proof inscription
In particular, the challenging peculiarities of glass create immense advantages for laser processing compared with conventional processes. "For example, wear-free inscriptions can actually be produced inside the glass. This is very useful in medical technology applications since no ink may be used and special hygienic conditions have to be fulfilled", said Petra Wallenta, Marketing Communication Manager for Europe at Coherent. The size, style or content of the inscription can also be easily changed from product to product during series production. "And the markings are forgery-proof," added Wallenta. Coherent has supplied laser systems here for marking extremely thin display glass and for identification marks on the cover glass for solar cells.
Conventional separation processes reach their limits with displays
To date, glass has mainly been separated by cutting and breaking the material. The disadvantage here is that the breaking edge had to be reworked since the score in the breaking edge leaves behind fine minute cracks. These minute cracks may lead to glass panels breaking easily later during transport, coating or hardening. Laser separation processes prove their advantages in this case: Dr. Ralph Delmdahl, Product Marketing Manager at Coherent LaserSystems: "A laser offers the advantages of non-contact, flexible and environmentally-friendly machining during glass processing. In particular, display glasses with thicknesses of less than 1 mm benefit from the use of a laser for cutting, contouring, marking and drilling holes. This mainly applies to chemically hardened glasses and sapphire glass which can only still be processed by a laser with sufficient quality. Unlike mechanical processes, rework or cleaning steps can often be dispensed with. Small structure sizes of less than 100 µm can also only be produced using a laser."
Trumpf expert Siebert has also experienced something similar: "The glasses in the layer systems of modern displays are often barely thicker than 0.3 mm and are extremely hard. For example, it is almost practically impossible to cut hardened cover glasses of smartphones using conventional methods. The utilised tools subject the thin glasses to mechanical loading and produce minute workpiece-endangering cracks which can only be eliminated by reworking the edges. Efficient and cost-effective cutting processes can only be achieved by using a laser. Cutting using diamond wheels is also inflexible, and it is difficult to produce contours." Thomas Wahl can only concur with this: "Laser processing of glass is worthwhile wherever conventional processes reach their limits, for example with close-contoured processing of freeforms. Another argument in favour of lasers is the faster processing speed." "Compared with mechanical processing of glass," added Petra Wallenta, "we can see increased production and higher process reliability in production."
Spotlight on USP
In order to ensure that low thermal conduction or uneven warming of the glass material does not lead to stresses and, thus, minute cracks, the solution providers for production machines and/or laser systems are relying on processing which is "as cold as possible". Absorption and thermal conduction are very important parameters in laser-based glass processing. "Glass is transparent for light in the visible range and close infrared wavelength range. It firstly absorbs light rays in the far infrared range - as emitted by CO2 lasers - or the ultraviolet range. In the visible range ultra-short pulses can be absorbed through non-linear effects," said Christof Siebert. Short or ultra-short pulse lasers are currently in the spotlight in glass processing.
Future prospects; faster, thinner, but stable!
Laser-based glass processing has a future. An event organised by the Hanover Laser Centre last year especially on the topic of laser processing of glass materials came to the following conclusion: "Laser-based glass processing is now the state of the art in many branches of industry and still harbours great potential for other fields of technology." Intensive work is therefore still being carried out to increase the throughput rates. "Depending on the application areas, this is achieved," said Dr. Delmdahl, "through a higher pulse frequency or higher pulse energy of the utilised laser. In view of the thinner glass thickness and increasingly finer structures, the tendency is still towards improved processing quality." "In particular, the final close-contoured processing of chemically or thermically hardened glasses down from the mother glass," added Senior Developer Wahl, "is a challenge for which quick solutions can, however, be expected. It is also shown that large-area laser processing can optimise the properties of functional layers, for example with heat protection glass. This will also be a task in the near future." According to the expert from Newport Spectra-Physics, there is normally a challenge in that the glass material technology changes very quickly and the laser systems would have to be adapted accordingly. Under the motto "Increasingly thinner, but stable!", the glass industry is trying to find the perfect display glass: "It consists solely of an infinitely hard surface," said Christof Siebert, "and has practically no thickness whatsoever. Display manufacturers are continuing to work on this ideal state, a fact which also poses enormous challenges for us laser system manufacturers."
Exhibitors at LASYS 2014 know what matters!
By way of example, five exhibitors at LASYS 2014 give an overview here of what laser systems can now do in glass processing:
Drilling 1,000 microvias a second in thin glass wafers
Coherent is represented in all areas of industrial laser glass processing and offers a wide range of suitable laser systems for different materials. They include, in particular, high-performance pulsed CO2 lasers for fast separation of displays and production of straight cutting edges and picosecond lasers for flexible production of variable structures in hardened cover glass. Ultra-short pulse lasers are used primarily for precise cutting out of rounded contours in hardened glass or sapphire. And pulsed excimer lasers are used at a wavelength of 193 nm for marking and drilling microvias in thin glass wafers. "Simultaneous drilling of up to 1,000 microvias per second in thin glass wafers for microchip integration is only possible using an excimer laser," said Dr. Delmdahl.
Drilling of triple-glazed interior panes
Manz can demonstrate a high level of competence in automation, measuring technology, laser technology, vacuum coating technology and wet-chemical process technology for cleaning, texturing and etching substrates. The mechanical engineering company provides customer-specific solutions ranging from stand-alone machines through to an integrated production line. "In particular, the integrated approach," argued Thomas Wahl, "offers great advantages for users who obtain everything from a single source and therefore need not worry about any interface problems." A typical stand-alone project implemented by the company consisted of a process tool for drilling pressure compensation holes in triple-glazed interior panes. It was integrated in an existing production line. Manz supplies system solutions, for example integrated production lines in which glasses are processed for touch devices from the mother glass through to the ready-to-install touch sensor.
High-speed micro processing
At Newport Spectra-Physics UV lasers solve the transparency problem, produce high precision, cope with high process speeds and ensure the required cost-effectiveness. However, ultra-fast lasers use non-linear absorption and make high-quality 'cold' micro processing possible. "To ensure that laser systems are accepted by the market, they must be very reliable and have low operating costs coupled with high throughput rates. We develop our laser systems in order to open up new applications and pursue both objectives: low operating costs and high throughput," said Dr. Ruffing. For example, the new Quasar high-performance UV laser has an average power of 60 W and features programmable pulse shapes and high repetition rates. "This opens up an entirely new process parameter area for UV lasers," emphasised the expert and continued: "We developed the laser in order to use new micro processing processes at high speed and cut or drill, for example, hardened glass for mobile devices at speeds of between 1 and 1.5 m/s with very high quality. Programming the pulse shape enables the process to be tailored to generate straight lines, curves, holes or slots in a wide range of glass materials - and all with the same laser."
Ceran glass panes under a laser beam
Reis Robotics supplies both articulated-arm robots and portal and special kinematic systems. They can be equipped with both CO2 lasers and solid-state lasers. "USP lasers will also be possible in future. Our advantages for users are the customer-specific solutions," said Norbert Höppe. The company has produced, for example, a system for laser cutting of ceran glass panes. The expert: "The challenges firstly involved transporting the glass panes, selecting a suitable laser and extractor system, and removing the cutting residues."
Equipped for displays of tablets, smartphones, etc.
The ultra-short pulse lasers from Trumpf operate with pulses in the picosecond and femtosecond range, and are ideal for processing brittle and transparent materials. The ultra-short pulses do not generate any heat. Material can be removed from extremely fine areas measuring just a few millionths of a millimetre - without burr-forming melts or quality-impairing material heating. The company has developed precise regulation of the beam parameters which is necessary for exact processing at the micrometre level: "The patented double feedback controller monitors every individual picosecond pulse and keeps the output and pulse energy, irrespective of external influences, exactly at the required level," said Siebert and added: "Our multi-regulated lasers cut with high process reliability at a high cutting speed. A high throughput rate coupled with high unit numbers is necessary, for example, in highly rationalised semiconductor and electronics production. We were able to fulfil these requirements with our disk laser technology. Our ultra-short pulse lasers are careful but powerful tools which are keeping pace with the conditions in three-shift production at manufacturers of smartphones, tablets, etc."
LASYS 2014 with a first-class accompanying programme
The future will therefore remain exciting along with the international trade fair LASYS which will accompany the laser material processing industries as the most important platform. In addition to the around 200 exhibitors expected in June 2014, LASYS 2014 will again feature an extraordinarily diverse accompanying programme for further training and forging contacts. http://www.messe-stuttgart.de/lasys/besucher/rahmenprogramm/
Featured Product
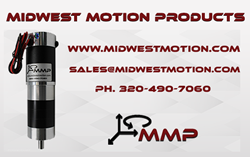