Improving control of conveying systems
Industrial automation specialist Beckhoff Automation UK has launched a new EtherCAT-based controller for motor-driven roller (MDR) conveyor systems. The controller, the EP7402 EtherCAT box, provides complete control of roller motors irrespective of the motor brand or conveyor vendor. This allows enhanced efficiency, improved communication and reducing cabling requirements in multi-zone conveying applications in intralogistics, warehousing and distribution centre environments.
The EP7402 features two motor outputs with an integrated controller for brushless DC (BLDC) motors. These motors can be directly connected to the EtherCAT box, with eight additional M8 input/output ports for peripherals, including sensors, vision systems and switches. Power is supplied to the EP7402 using a single 30A hybrid B23 cable, building on Beckhoff's One Cable Automation (OCA) technology.
With complete control over the roller motor, the EP7402 is readily adaptable based on performance characteristics. Parameters including maximum rated current, acceleration or deceleration ramps and various others can be configured to support adaptations for different applications. This control is completely sensorless and is determined based on programming and motor performance.
The controller also integrates directly into Beckhoff's TwinCAT 3 software, allowing technicians to easily program the EP7402 using motion designer software. This integration also streamlines distributed controller architectures by supporting automation detection and addressing of new networked controllers. All diagnostic data processed by the controller is also transmitted back to TwinCAT Analytics in real-time, supporting the development of predictive maintenance schedules.
"Industry 4.0 has been a term batted around for almost a decade now, but mostly by industrial manufacturing and engineering businesses," explained Stephen Hayes, managing director of Beckhoff UK. "However, these same technologies can be used to significantly improve intralogistics and warehousing operations, bolstering throughput and efficiency.
"Intralogistics and warehousing environments are increasingly turning to multi-zone conveyor systems, and the ability to control the motors underpinning these systems is essential for efficient, scalable operations. The new EtherCAT box is designed to provide this control, as well as in-built diagnostic capabilities and support for integration with TwinCAT and TwinSAFE technologies, that is required to significantly improve the performance of traditional roller conveyors. This is on top of the flexibility of integration provided by Beckhoff's OCA concept."
The OCA concept is based on a single EtherCAT P cable that integrates communication and power supply and streamlines end-to-end connection of components, terminal boxes and machine modules. OCA features two connector types: ECP hybrid connectors are designed to provide an integrated 24 V DC power supply in EtherCAT P specifications, and ENP hybrid connectors for EtherCAT/Ethernet applications without integrated power supply.
The EP7402 EtherCAT box is rated to IP67 standards to ensure suitability for conveying systems in more demanding areas. The controller can also be integrated with Beckhoff's TwinSAFE functional safety solution. As a result, conveying systems can easily incorporate standard e-stops, pull cords, light curtains and other safety devices into the convenient and simplified wiring solution provided by the B23 hybrid EtherCAT P cabling to the central controller running TwinCAT.
To learn more about the EP7402, visit the Beckhoff Automation website. Alternatively, speak to a member of the Beckhoff UK team if you are interested in the company's automation solutions to improve intralogistics operations.
Featured Product
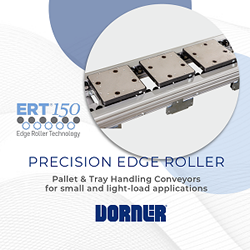