TRUMPF develops smart, self-programming robot that sets its own weld path
TRUMPF will present arc-welding robot that programs its own weld path at world’s leading trade fair for joining and cutting // Smart sensor enables robot to determine weld spots automatically // Technology will help tackle shortage of skilled workers
TRUMPF will be showcasing a robot that uses sensors to program its own weld path at "Schweissen & Schneiden", the world's leading trade fair for joining, cutting and surfacing technology, which will be held in Essen, Germany. The robot makes use of TRUMPF's new smart seam-tracking technology, which the high-tech company developed in collaboration with the Fraunhofer Institute for Manufacturing Engineering and Automation IPA. "We've basically developed a way for the welding robot to program itself. For users, that means a much easier transition into automated arc welding - plus a clear competitive edge," says TRUMPF R&D manager Sven Klingschat. Housed in the head of the welding torch, the sensor automatically calculates the weld path for each part.
Robot ready to go in seconds
With conventional welding robots, production workers have to program a new weld spot into the software each time they want the robot to change direction. This is a time-consuming business, especially when it comes to complex parts with many curves or corners. Fortunately, the new smart seam-tracking function makes the whole process a whole lot simpler. All the user has to do is to place the welding robot in the start position, and the technology takes care of the rest. The robot uses the sensor to determine the weld path automatically. The system software quickly calculates the weld spots and creates the welding program for the respective part. So the robot is good to go in a matter of seconds.
This solution makes it far easier to program the robot. "The whole process takes seconds to complete, even for complex parts such as spiral arcs. And it doesn't require any specialist knowledge on the part of production workers," says Klingschat. What's more, the intuitive user interface can be used to carry out a whole range of welding tasks, such as sealing runs and identical weld seams.
Less scrap and a more stable process
Smart seam tracking helps companies save time and cut costs while also making life easier for workers on the shop floor. The robot's ability to automatically correct its weld path makes the whole process more stable. It also simplifies the task of handling tighter tolerances and dealing with warping or distortion. This is the right solution for any business looking to harness automation in order to boost productivity. It's particularly useful for fabricators who weld large and complex parts. And the creation of a customized weld path for each individual part is an excellent way to achieve consistently high quality. Components for wind turbines and screw conveyors for the animal-feed industry are just two examples of areas that can benefit from this innovative and efficient method. TRUMPF will be incorporating the solution in its TruArc Weld 1000 arc-welding machines. It can also be retrofitted to existing TruArc Weld systems.
Digital photographs in print-ready resolution are available to illustrate this press release. They may only be used for editorial purposes. Use is free of charge when credit is given as "Photo: TRUMPF". Graphic editing - except for cropping out the main motif - is prohibited. Additional photos can be accessed at the TRUMPF Media Pool.
Featured Product
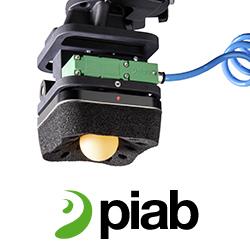