Flexxbotics Announces Robot Compatibility with SICK Vision Solutions for Quality Inspection
Now, companies can enable robot-driven manufacturing with Flexxbotics using SICK to achieve closed-loop quality and six sigma consistency in unattended operations.
Boston, MA - June 11, 2024 - Flexxbotics, delivering workcell digitalization for robot-driven manufacturing, today announced advanced robotic machine tending compatible for quality inspection connectivity with the full line of SICK machine vision technologies including 2D and 3D vision sensors and vision cameras. Now, companies can enable robot-driven manufacturing with Flexxbotics using SICK to achieve closed-loop quality and six sigma consistency in unattended operations.
Flexxbotics' breakthrough innovation, the FlexxCORE technology, enables the robots to securely connect and communicate with SICK equipment. With Flexxbotics the robots receive direct feedback based on automated inspection results enabling real-time adjustments to CNC machine programs for autonomous process control. With in-line inspection, Flexxbotics orchestrates the fleets of robots in the smart factory to achieve continuous operations enabling significant defect reductions while improving throughput and increasing profit per part.
Flexxbotics compatibility includes SICK's AI-powered Inspector83x vision system, as well as, InspectorP61x, InspectorP62x, InspectorP63x, InspectorP64x, InspectorP65x, Visionary-T Mini, Visionary-S, Ruler3000, Ranger3, picoCam2 and TriSpector1000.
"We understand that the robots need to work with the latest next-gen inspection technologies and CNC machines, as well as, older equipment that manufacturers already have in their factories," said Tyler Modelski, CTO & Co-founder of Flexxbotics. "That's why our compatibility extends to over a 1000 different makes & models of inspection equipment and other factory machinery."
Flexxbotics robotic workcell digitalization is the backbone of the Smart Factory, delivering robot-driven manufacturing at scale with autonomous process control for continuous operations. Flexxbotics solution runs both online and offline so production continues with or without internet access, and Flexxbotics works with existing business systems such as CAD/CAM, DNC, SCADA/HMI, IIoT, MES, ERP, PLM and others for comprehensive process integration.
A full set of bi-directional communications, transforms and routing capabilities are available in Flexxbotics for the inspection tools, robots, and machinery that are connected including loading programs, sending instructions, updating parameters and status awareness depending on the machinery's capabilities so the robots drive the SICK equipment along with the CNC machines and other asset in the smart factory.
"We believe that the inspection equipment serves as the ‘eyes and ears' for the robots in the smart factory running production in ‘lights out' manufacturing," said Tyler Bouchard, CEO & Co-founder of Flexxbotics. "By integrating inspection vision system capabilities to robots with Flexxbotics, global companies are able to achieve continuous operations through robot-driven manufacturing with autonomous process control."
About Flexxbotics
Flexxbotics robotic workcell digitalization is the backbone of the Smart Factory delivering autonomous process control for next generation machining environments. Flexxbotics SaaS/hybrid solutions enable robot-driven manufacturing at scale. Flexxbotics breakthrough, the FlexxCORE™ technology, seamlessly connects and coordinates robots with existing automation equipment, IT systems and people. More powerful, flexible and open, Flexxbotics revolutionizes the use of robotics in complex production. Visit www.flexxbotics.com to learn more and follow us on LinkedIn.
Flexxbotics, 12 Channel St, Boston, Massachusetts 02210, United States, 1 (877) 456 1576
Unsubscribe Manage preferences
Featured Product
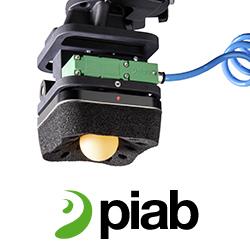