Micropositioning Stages Ensure High Accuracy, Stability, and Resolution down to 0.005 microns
PI’s L-511 precision linear stage series is available for fast delivery, enabling high-end industrial, and research applications.
Auburn, MA — PI, a global leader in precision motion control and nanopositioning, now offers fast delivery of the L-511 linear micropositioning stage — designed for applications requiring minimum incremental motion down to 20 nanometers, drive forces up to 22 lbs, and multi-axis configuration options.
With linear travel up to 155 mm (6"), the L-511 can be combined to form XY or XYZ motion systems and integrated with rotary stages for enhanced flexibility. A variety of drive and encoder options (stepper and servo motors, rotary and linear encoders) enable ultra-fine sensitivity from 0.6 microns down to 0.005 microns.
The L-511 features high-load recirculating ball bearings for exceptional durability, even under demanding, repetitive cycles. Despite its compact footprint, it handles loads up to 500 N (110 lbs) and achieves travel speeds up to 90 mm/sec. A precision 2 mm pitch ball screw drive is nested in a stress-relieved aluminum base to ensure maximum stability and low drift.
To enhance positioning accuracy and automation throughput, the stage integrates non-contact, direction-sensing optical reference point switches located at mid-travel. Non-contact limit switches are also included to safeguard the mechanical structure.
Custom Calibrations
Custom-tuned, aligned, and error corrected 2-axis and 3-axis stage assemblies are also available, through PI's US engineering and manufacturing team.
Controller Options
PI offers a range of high-performance controllers for stepper, servo and 3-phase motors, in both single- and multi-axis configurations, fully compatible with the L-511 stage. Each controller is supported by PI's comprehensive software suite, enabling rapid start-up and seamless integration into custom automation environments.
Industries Served
Metrology, laser processing, semiconductors, biotech, optical alignment, advanced automation
Featured Product
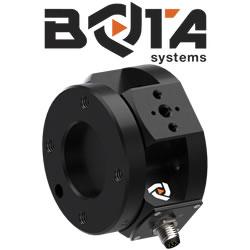
Bota Systems - The SensONE 6-axis force torque sensor for robots
Our Bota Systems force torque sensors, like the SensONE, are designed for collaborative and industrial robots. It enables human machine interaction, provides force, vision and inertia data and offers "plug and work" foll all platforms. The compact design is dustproof and water-resistant. The ISO 9409-1-50-4-M6 mounting flange makes integrating the SensONE sensor with robots extremely easy.
No adapter is needed, only fasteners! The SensONE sensor is a one of its kind product and the best solution for force feedback applications and collaborative robots at its price. The SensONE is available in two communication options and includes software integration with TwinCAT, ROS, LabVIEW and MATLAB®.