The Uses of High Purity High Pressure Gas Regulators in Robotics Manufacturing
Shenzhen Jewellok Technology Co., Ltd Is A Control Valves and Pressure Regulators Manufacturer, Manufacturing Single Stage Pressure Regulator, Two Stage Pressure Regulator, Low Pressure Nitrogen Gas Regulator, High Pressure Nitrogen Gas Regulator For Industrial Automation Manufacturing
The Uses of High Purity High Pressure Gas Regulators in Robotics Manufacturing
Introduction
In the fast-evolving landscape of modern manufacturing, precision, efficiency, and reliability are non-negotiable. Robotics has become a cornerstone of this transformation, enabling industries to achieve unparalleled accuracy in tasks ranging from welding to painting. Central to the success of these robotic systems is the high purity high pressure gas regulator—a specialized device designed to control gas pressure with exactitude while ensuring the gas remains free of contaminants. These regulators are vital in applications where even the slightest impurity or pressure deviation can compromise product quality or process integrity.
High purity high pressure gas regulators are engineered to manage gases stored at elevated pressures, delivering them at precise levels suited to specific tasks. In robotics manufacturing—interpreted here as the use of robots in manufacturing processes—these devices ensure that gases are supplied cleanly and consistently. This article explores their critical applications, including robotic welding, laser processing, pneumatic systems, painting and dispensing, and cleanroom operations, demonstrating their indispensable role in automated manufacturing.
Robotic Welding
Robotic welding is a foundational process in industries like automotive and aerospace manufacturing, where robots use welding torches to join metal components with precision. A key factor in producing strong, defect-free welds is the use of shielding gases—such as argon, helium, or their mixtures—which protect the weld pool from atmospheric contaminants like oxygen and moisture. Contamination can cause porosity or weaken the weld, making gas quality paramount.
High purity high pressure gas regulators are essential here. They deliver shielding gas at the precise pressure needed to stabilize the welding arc and maintain optimal flow, ensuring consistent weld quality. The high purity feature prevents impurities from entering the gas stream, which could otherwise introduce flaws into the weld. Since shielding gases are often stored at high pressures, these regulators must also reduce that pressure to a usable level without compromising purity. By enabling a steady, clean gas supply, they enhance productivity and minimize rework in robotic welding operations.
Robotic Laser Processing
Laser processing—encompassing cutting, welding, and engraving—is another domain where robots excel. In laser cutting, a focused laser beam melts or vaporizes material, and an assist gas (e.g., oxygen, nitrogen, or air) expels the molten debris to refine the cut. The type and quality of this gas directly influence the outcome. For instance, nitrogen is used when cutting stainless steel to prevent oxidation and ensure a clean edge, while oxygen enhances cutting speed in mild steel.
High purity high pressure gas regulators ensure that assist gases are delivered at the exact pressure required for optimal performance, free of contaminants that could mar the cut quality, such as discoloration or roughness. High pressure capability is crucial, as some applications demand high flow rates, necessitating regulators that can handle substantial inlet pressures. In laser welding, similar principles apply, with assist gases shielding the weld zone or aiding the process. These regulators thus uphold the precision and consistency that robotic laser processing demands.
Pneumatic Systems in Robotics
Pneumatic systems power many robotic functions, such as actuation, gripping, or tool operation, using compressed air or other gases to drive cylinders and valves. The gas must be supplied at a specific pressure to ensure these components function correctly, making pressure regulation a critical task.
High pressure gas regulators step down the source pressure—often high in industrial settings—to the levels required by pneumatic systems. In sensitive manufacturing environments, like those producing electronics or pharmaceuticals, gas purity becomes equally important. Contaminants in the gas could damage pneumatic components or contaminate the product, as seen in semiconductor fabrication where even trace impurities are disastrous. High purity regulators address this by delivering clean gas, sometimes specialty gases beyond air, without introducing pollutants. This combination of pressure control and purity enhances the reliability and efficiency of pneumatic robots in manufacturing.
Robotic Painting and Dispensing
In sectors like automotive production, robots perform painting and dispensing tasks, such as applying paint, adhesives, or sealants. These processes often rely on gases for specific purposes. In spray painting, compressed air atomizes the paint into a fine mist for uniform application. The air's purity is critical—moisture, oil, or particulates can cause defects like fisheyes or uneven finishes, undermining quality.
High purity gas regulators ensure the air is clean and dry, safeguarding the paint application's integrity. Similarly, in dispensing, gases may pressurize materials or create inert atmospheres to prevent premature curing or contamination, requiring precise pressure and purity control. Given that gas sources are typically high-pressure, these regulators reduce the pressure to usable levels while maintaining quality. In robotic painting and dispensing, they are vital for achieving consistent, high-quality results that meet stringent industry standards.
Cleanroom Applications
Cleanrooms, prevalent in semiconductor, pharmaceutical, and biotechnology manufacturing, demand strict atmospheric control to prevent contamination. Robots are widely used here to handle materials or perform tasks, minimizing human-induced impurities. Any gases employed in these robotic systems—whether for pneumatics or other functions—must meet the highest purity standards to avoid introducing particles or chemicals into the environment.
High purity gas regulators are critical in this context, ensuring that gases used by robots comply with cleanroom cleanliness requirements. Additionally, some cleanroom processes use specific gases to maintain controlled atmospheres, necessitating regulators that deliver both purity and precise pressure. By preventing contamination from robotic operations, these devices protect product quality and uphold the integrity of sensitive manufacturing processes, making them essential in cleanroom robotics.
Conclusion
High purity high pressure gas regulators are a linchpin in robotics manufacturing, supporting a range of applications that drive modern industry. They ensure the quality of welds in robotic welding, the precision of cuts in laser processing, the reliability of pneumatic systems, the excellence of finishes in painting and dispensing, and the purity of cleanroom environments. By delivering gases at exact pressures and maintaining exceptional cleanliness, these regulators enable robotic systems to perform at their best, producing high-quality goods efficiently.
As manufacturing continues to advance, with robotics playing an ever-larger role, the importance of these regulators will only increase. Their multifaceted contributions underscore their critical place in automated manufacturing, ensuring that precision and reliability remain at the forefront of industrial progress. For more,you can pay a visit to Jewellok at https://www.jewellok.com
Featured Product
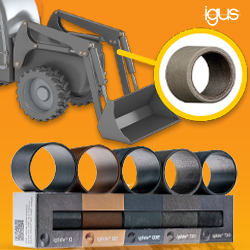
igus® - Free heavy-duty plastic bearings sample box
The iglide® heavy-duty sample box provides a selection of five unique iglide bearings, each suitable for use in heavy-duty equipment due to their self-lubricating, dirt-resistant properties. Each bearing material boasts unique benefits and is best suited for different application conditions, though each can withstand surface pressures of at least 11,603 psi at 68°F.