Mining practices have remained largely unchanged over the past 30 years. Accessible deposits are becoming harder to find with valuable deposits increasingly found only in remote areas of the world or in locations down hundreds of feet. These are expensive and dangerous to reach. Mining companies are going to have to deal with that and the best way is to automate the systems so that the human becomes the supervisor, rather than the direct worker.
Len Calderone for | RoboticsTomorrow
For many years now, robots have taken on the role of humans in many jobs, especially the more dangerous ones, like mining. Technicians and engineers can monitor and control the mine of the future from thousands of miles away. With the coming of robotic haul trucks, trains/conveyers, drilling, and blasting rigs, the human miner will disappear from the mines as robots take over.
Remember the miners that were trapped in the 2010 Copiapó mining accident in Chile? They were trapped for 69 days as workers performed a dangerous operation to rescue the miners. Using robots in mines will eliminate the threat of a mine disaster taking the lives of mine workers. In the last ten years there were 316 coal mine deaths in the U.S., but in China 43,575 men lost their lives during that same time period.
Sandia National Labs designed their Gemini-Scout, a remote-controlled rolling robot to lead search-and-rescue efforts in the event of a mining disaster. When a mine collapses, information is essential for a speedy search and rescue effort. Mining accidents have many dangerous conditions, such as structural weaknesses within the shafts themselves, poisonous vapors, explosive gases, and flooded tunnels. Without proper information, the rescue crews risk worsening the situation.
Gemini-Scout is designed to cope with all of these things so it can get down into a mine quickly, searching for survivors and assessing threats. Its tracked propulsion and articulated suspension allows it to climb rubble piles and crawl over uneven terrain. Gemini can roll over obstacles and into the sand and gravel pits, as well as turn in tight circles. It can make 45° climbs, and at less than two feet tall, it can maneuver through tight spaces with ease.
This rescue robot can move through water up to 18” deep while sampling the air for toxic fumes to notify rescue personnel what vapors are lingering in the mine, such as explosive methane gas. The robot can be equipped to carry food, air tanks or other supplies to trapped miners. The control is a standard Xbox 360 remote, so virtually anyone familiar with Xbox games can control the Gemini-Scout.
Rather than needing the Gemini-Scout, some mines are employing more robotic equipment, which will eliminate the danger posed by mines.
Six Caterpillar 793F autonomous trucks will begin working at the Solomon iron ore mine run by Fortescue Metals Group in Western Australia. When the mine is at full operational capacity, it is anticipated that the mine will have 45 autonomous trucks, operating without a worker onboard. The fleet of autonomous trucks will work around the clock at the mine site while a technician supervises the trucks from the comfort of a control room.
An autonomous truck can follow an assigned lane through the landscape of the mine or decide what the best path is from its current location to where the control center wants it. If something gets it its way, the truck knows to stop, making working around these monstrous trucks safe.
The truck is automatically guided to the loading spot after computing the position of the bucket of the GPS fitted hydraulic excavator or wheel loader. The truck interacts with manned equipment including excavators, graders, wheel dozers, bulldozers and light vehicles. Manned equipment is also fitted with GPS and communications software.
Navigating a prearranged work area and completing designated tasks are accomplished by on-board computer systems. Highly developed perception technologies allow the trucks to work flawlessly around other mine equipment and personnel, even in congested areas. Autonomous trucks use a radio infrastructure and GPS technology, which most mines have in place.
A control system divides a manually defined dumping area and tells the truck exactly where to dump each load. After the ore is delivered from the trucks to the crusher, an impact hammer automatically fragments oversized rocks for crushing.
Automated trains have been around for some time, but not on long-haul railway networks but this may change as ore will need to be shipped to ports many miles from the mines and there is a shortage of drivers.
Rio Tinto is moving to a driverless automated rail network to transport its iron ore
Because fewer people are needed, the environmental footprint is lower. The operation can be managed remotely with less people on a site, eliminating the need to build water lines, buildings and other things that it takes to support a person in a remote area. Autonomous mining vehicles are more energy efficient, which will have a positive effect on the environment.
Because of labor shortages and deposits that are increasingly harder to get to, mining companies are now taking steps to take humans out of harm’s way and put robots in their place.
The rail-veyor®, built by Rail-Veyor Technologies Global, Inc., combines train, conveyor, and truck hauling features into a single system. A machine loads train cars with ore deep within a mine. The automated train then travels back to the surface where the control center is located. Since humans are not involved, the tunnels are much smaller than standard mine tunnels. The train cars are pushed along the tracks by electrical drive stations. Multiple trains can operate on the same track as their movements are coordinated. When the trains exit the mine, they turn into conveyor belts, hugging the light rail and inverting at the end to dump the ore. Then, they head back to the mine for another load.
Rail-veyer dumping ore
To get at the ore, mining companies will use drilling robots, but these robots will not only drill in the mines but they will scoop-up and offload ore onto the automated trains or conveyers for transportation to the surface. The operators will be outside in a control center and direct the machines remotely using a three-dimensional scanner attached to the robots.
Atlas Copco introduced the production drilling rig Simba W6 C to the market, which is equipped with a rig control system that optimizes the performance for in-the-hole hammer applications. The Simba W6 C rig has unattended drilling in full automation, enabling the operator to supervise several drill rigs at the same time.
An important feature is the water pump system which gives high efficiency, low water spillage with a low overall cost. An air venting system ensures long pump life, and the pump pressure control optimizes hammer efficiency and life length.
Atlas Copco’s drilling rig, Simba W6 C
One of the vehicles central to open-pit mining operations is a surface drilling rig. This large tracked vehicle drills holes into the ground that are filled with explosives and detonated. The fragmented rock is then extracted. Drill motions are not arbitrary, as hole locations are carefully planned in regular patterns. Underlying geology determines the form of preferred maneuvers.
An autonomous drill can move smoothly from one hole location to the next, and drills faster than a manned drill with a position accuracy within six inches. It can be switched from rotary to hammer percussion drilling as required, and can stabilize a hole by collaring, injecting water and back-reaming. It drills to its assigned depth within a 0.4” tolerance. It can produce straight rows of holes, or it can drill holes in complex patterns. An operator can switch the rig between manual, remote and autonomous operation, depending on the terrain and complexity of the required task.
With all of the autonomous equipment in operation, the operations center will receive a mind-boggling amount of data from these sources, including a large number of mine site-based CCTV cameras. The TV cameras will transmit all relevant aspects of the production process at the mine, including watching the ore as it tumbles off the conveyor belt onto the stockpile or into the crusher.
To handle all this data, the primary communications link between the operations center and the mine operations will be by optic fiber cable. There will actually be two cables, which are physically separated to ensure redundancy in case of significant systems failure. There will also be a satellite-based back-up, as an added contingency
Mining practices have remained largely unchanged over the past 30 years. Accessible deposits are becoming harder to find with valuable deposits increasingly found only in remote areas of the world or in locations down hundreds of feet. These are expensive and dangerous to reach. As experienced miners retire, the number of skilled workers is decreasing, creating a labor shortage of trained personnel. Mining companies are going to have to deal with that and the best way is to automate the systems so that the human becomes the supervisor, rather than the direct worker.
For further information:
- http://www.infomine.com/library/publications/docs/InternationalMining/Chadwick2010b.pdf
- http://www.baeconomics.com.au/wp-content/uploads/2010/01/Mining-innovation-5Feb12.pdf
- https://mining.cat.com/command
The content & opinions in this article are the author’s and do not necessarily represent the views of RoboticsTomorrow
Comments (0)
This post does not have any comments. Be the first to leave a comment below.
Featured Product
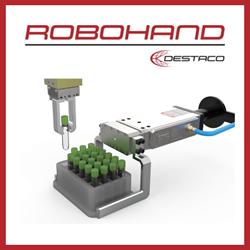