Upgrading existing systems or basing new designs on plug-and-play USB3 Vision-compliant video interfaces, designers can produce a winning combination of performance, ease-of-use, and cost advantages.
Kimm Krueger | Pleora Technologies
Once relegated to the minor leagues of machine vision video interfaces due to its limited bandwidth and lack of standardization, USB may turn out to be the home run designers need to reduce the cost and complexity of sophisticated vision systems for robotics.
Machine vision applications rely on the real-time delivery of lossless video from an image source to a computing platform to perform time-sensitive analyses and decision-making tasks. Designers have typically met this requirement by deploying legacy video interfaces, such as Camera Link®, or developing custom solutions. The evolution to SuperSpeed USB, in combination with the development of the USB3 Vision™ standard, provides designers with an alternative that delivers bandwidth, cost, and ease-of-use advantages.
This article provides an overview of the USB3 Vision standard and looks at some of its benefits for designers and end-users in video interfaces for robotics applications.
The Video Interface Challenge
Advanced vision systems must transfer high-resolution images from cameras or image sensors to computers used for analysis and display in real-time, and with low, consistent latency (or delay). A bin-picking robot on a manufacturing line, for example, requires instantaneous transfer of imaging data from a camera to a processor to precisely locate and choose parts from a storage container. Within milliseconds, the vision system must detect an object, model it and the surrounding environment, accurately select the part, and then plan its next path.
The video interfaces in these systems – the hardware and software used to format image data and transmit it to a computer or display – are often based on a Camera Link standard or custom design. Both of these approaches have significant downsides. While Camera Link video interfaces provide the bandwidth required for high-resolution sensors and fast frame rates, the tradeoff is complexity and cost. Each camera or sensor requires a PCIe frame grabber at the computing endpoint to capture data, as well as a discrete power supply. In addition, Camera Link cabling is expensive, heavy, and difficult to manage.
With custom solutions, manufacturers often underestimate the time, standards expertise, and knowledge required. These solutions are often costly to develop and maintain, introduce integration challenges in multi-vendor systems, and can sidetrack internal R&D resources from more valuable core projects.
Basics of USB3 Vision
USB interfaces have been widely adopted in consumer and PC applications, but the bandwidth supported by earlier versions was insufficient for machine vision applications requiring uncompressed, raw data for real-time image analysis. This changed with the third major version of the USB standard – USB 3.0 or SuperSpeed USB – which provides 10 times the bandwidth of USB 2.0 while addressing power and processing usage.
Recognizing the potential of USB 3.0 for real-time video connectivity, the machine vision industry introduced the USB3 Vision standard in 2013. USB3 Vision provides a framework for designers to address performance, cost, and usability requirements in real-time imaging systems. Data is transmitted directly to existing ports on computers with sustained throughputs approaching 3 Gb/s, surpassing the performance of Camera Link Base configurations and rivalling Medium configuration but without requiring multiple cables or specialized PCIe frame grabbers at endpoints to capture data. By eliminating the need for frame grabber cards, designers can choose from a wider range of computing platforms, including laptops, tablets, and embedded processors.
USB 3.0 video interfaces deliver advantages beyond raw speed to help lower costs and boost performance. The flexible, lighter USB cables cost less and are simpler to install than the bulky cabling and connectors of legacy interfaces. To enhance reliability and ease-of-use, the USB3 Vision standard specifies locking connectors for the cables. Video, control data, and power are transmitted over a single cable, reducing cabling complexity and eliminating the need for an external power supply for cameras, resulting in reduced cost and system footprint.
USB 3.0 also reduces system overhead and CPU usage by using asynchronous signaling, rather than the polling mechanism of USB 2.0, and direct memory access (DMA) transfers. As a result, more processing power can be dedicated to the vision application. In multi-camera applications, multiple USB 3.0 cameras can operate in parallel on a single bus by employing an off-the-shelf USB 3.0 hub. In comparison, each Camera Link camera would require its own dedicated cable and frame grabber. Distance remains the last hurdle for USB 3.0 interfaces, with multiple vendors now introducing repeaters and active copper and optical cabling solutions that extend the potential distance between imaging sources and processing units for beyond the initial three meter range described in the USB3 Vision standard.
USB3 Vision and Robotics
As the USB3 Vision standard gains wider adoption, an increasing number of standards-compliant video interface products are becoming available as off-the-shelf solutions. For retrofit projects, external frame grabbers make it relatively straightforward for designers to convert feeds from existing cameras into more manageable USB3 Vision-compliant video. For new projects, embedded hardware products allow manufacturers to integrate USB3 Vision-compliant video connectivity directly into cameras and imaging systems, including custom sensors and smart camera heads for specialty applications.
The iPORT CL-U3 External Frame Grabber reduce design and cabling complexity by treating Camera Link cameras like plug-and-play USB 3.0 products.
In application diagram 1, a Pleora iPORT™ CL-U3 External Frame Grabber converts the image feed from an existing Camera Link camera in a bin-picking robot into USB3 Vision-compliant video. The uncompressed video – along with power and control – is transmitted with low, consistent latency over a USB 3.0 cable directly to existing ports on a computer used for analysis and display. The thinner, lighter USB 3.0 cable allows faster setup and teardown of work cells for different products and short production runs.
By eliminating the need for a frame grabber in a PCIe slot, designers are free to choose from a broad selection of small form factor and low-power computing platforms, including laptops, embedded systems, and tablets. In this example, video is being transmitted to a laptop for analysis and display. Leveraging an onboard programmable logic controller (PLC), the CL-U3 external frame grabber uses input signals to accurately and deterministically control and trigger the camera and other vision systems elements, such as area sensors and lighting sources.
USB3 Vision video interfaces reduce component count, costs, and system complexity while extending the operating life of battery powered service robots.
Increasingly, robotics manufacturers are migrating to embedded processing to help deliver footprint, weight, and power-saving advantages. However, as form factors shrink there is no room for an internal frame grabber. Diagram 2 illustrates how USB3 Vision-compliant external frame grabbers simplify the design of robots used for medical service or telepresence applications by employing a small form factor computing platform.
In this example, images from Sony Block cameras used for inspection and navigation in a medical service robot are converted to USB3 Vision-compliant video streams by Pleora’s iPORT SB-U3 External Frame Grabbers. Alternatively, iPORT NTx-U3 Embedded Video Interface hardware provides system and camera manufacturers with a straightforward way to integrate USB 3.0 video connectivity directly into their products. Video is then transmitted over high-bandwidth, flexible, low-cost USB cables directly to ports on an integrated single-board computing platform. By eliminating PCIe frame grabbers within the robot, designers can reduce system complexity, component count, and costs. In addition, decreasing the weight and power consumption of the robot extends battery life, translating into more patient visits between charges.
A Winning Combination
The industrial sector was among the first to recognize that machine vision could automate routine tasks and enable faster, more accurate quality inspection to boost productivity and profit. As processing power increases and image systems evolve to support complex real-time analysis, the video interface is under increasing pressure to keep pace with new performance demands. Upgrading existing systems or basing new designs on plug-and-play USB3 Vision-compliant video interfaces, designers can produce a winning combination of performance, ease-of-use, and cost advantages.
About Kimm Krueger
Kimm Krueger is Vice President of Marketing with Pleora Technologies, the world’s leading supplier of video interfaces for system manufacturers and camera companies serving the industrial automation, military, medical, and transportation sectors. Find out more at www.pleora.com.
The content & opinions in this article are the author’s and do not necessarily represent the views of RoboticsTomorrow
Comments (0)
This post does not have any comments. Be the first to leave a comment below.
Featured Product
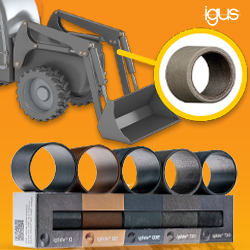