Implementation of a current transducer is typically a straightforward affair. In the event that the output is not as expected, it must be understood that the source of the challenge may be rooted in the mechanical, magnetic or electric nature of the device.
Current Transducer Implementation Phenomena
Contributed by | LEM Energy & Automation
There are technical underpinnings to challenges encountered when implementing current transducers. Some of these challenges are intermittent and difficult to reproduce. This difficulty and intermittent nature raise these issues to the status of phenomena; where challenges cross disciplines or enter into parts of electrical engineering knowledge that are less commonly understood.
This document is not an exhaustive review of the contained subjects, but more of an informative review of some known phenomena. Some phenomena can get quite sophisticated with overlapping effects. The goal of this document is to hopefully help a design engineer in the future. Perhaps the impossible event being observed is possible when certain uncommon technical effects are taken into effect.
Primary Conductor Positional Error
The location and size of the primary conductor within the aperture of the transducer have an impact on the accuracy of the measurement. The more centered the conductor and the more the conductor fills the aperture, the better the measurement.
Fig. 1 Primary Conductor Positioning and Size
The magnitude of error is difficult to quantify when the two criteria are not met. For most Open-Loop and Closed-Loop applications, the introduced uncertainty will be less than 0.1% full scale error.
Overload Effects
The transducer will have a current rating or a nominal and maximum rating. Regardless of the data sheet structure, there are events that can drive the primary current beyond the maximum rating of the transducer.
Transducers manufactured with a magnetic core are designed to operate within the linear range (or mostly linear) of the magnetic material. Driving the core beyond the linear region into saturation has consequences. The core will pick up a magnetic remanence, which will manifest as a DC offset at the transducer output. The magnitude of the remanence is core material dependent.
The magnitude of this offset is very difficult to estimate. The magnitude of the primary current overload and duration of the overload both impact the remanence. Typical overloads would be three to ten times nominal rating resulting in a DC offset from 0.1% to 2.5% of the nominal transducer rating. Closed-Loop transducers appear to have smaller remanence after a 3x excursion of around 0.1%-0.25%. Open-Loop transducers have a larger remanence after a 3x excursion of 0.5% or greater.
This remanence may dissipate over time in an AC current application, as the primary current rotates through the hysteresis curve. In a DC current application, the remanence will remain constant over time and will not dissipate.
Return Conductor Effects
The return conductor generates a magnetic field just as the primary conductor does. Since all electrical circuits are a loop by nature, there will be a return conductor somewhere. Depending on the location of the air gap and Hall cell in the transducer (with respect to the magnetic plane of the return conductor), the transducer output can be impacted. The right-hand rule is useful in making this analysis. Distance is important with the return conductor, keeping a distance proportional to its current away from the transducer. The field generated is not linear with distance. A distance of 10cm is generally accepted as a distance contributing negligible error. As this distance would be prohibitive in most applications, a transducer width can also be used as an example of acceptability if less than optimal spacing. A return conductor right next to the transducer may not have an effect if its magnetic plane does not interact with the air gap and Hall cell.
Fig 2. Optimal Return Conductor Positioning
Localized Saturation.
A unique phenomena is localized saturation. A nearby conductor outside the aperture of the transducer impacting the magnetic core. This does not necessarily need to be the return conductor. The conductor causing the localized saturation may not be in the magnetic plane that would interact with the air gap. The magnetic field generated within an adjacent magnetic core, combined with the field generated by the primary conductor may at times sum to a saturation level. This effectively ‘pinches off’ the circular continuity of the magnetic field within the core resulting in a lower field at the Hall cell than the primary current should generate. The effects of localized saturation and saturation in general is an attenuation of the Hall cell measurement. The output of the transducer will be lower than what the primary current should produce. This will have a dramatic effect in control situations where the transducer is used for feedback. As the transducer becomes increasingly non-linear and attenuated as it is driven into saturation, more current may be called for to reach setpoint. Eventually, the non-linearity is so great that a failure can occur due to the current being dramatically more than what the transducer says it is.
Dv/dt Effects
The coupling between two conductive surfaces is well known. This capacitive effect happens when the voltage on the primary conductor changes rapidly. Depending on the capacitive coupling between the primary conductor and any part of the secondary circuit, the primary dv/dt can appear on the secondary output (either voltage or current). This is true in both open-loop and closed-loop transducers. The issue may be more pronounced in a closed-loop application as the secondary winding provides more conductor area for coupling. Some dv/dt effects are just the superposition of the dv/dt, scaled to a degree, on the secondary output. Other dv/dt effects can be overshoot or noise effects, which are difficult to determine the source. Rotating the primary conductor or rotating the transducer can make a difference. Changing the surface area of the primary conductor facing the secondary winding can improve performance. Moving the secondary winding away from the suspected point of coupling can also help.
Surrounding Magnetics
Transducers do not actually measure current. The typical transducer measures the deflection of current on a Hall cell. This deflection is proportional to the magnetic field orthogonal to the Hall cell. This magnetic field can be interfered with: by positional error, return conductor effects, remanence and localized saturation. The primary current and the transducer may not be the source of the error. Outside magnetics and close proximity of magnetic materials can influence the magnetic field. Large inductors positioned closely to the transducer can impact transducer accuracy. The right hand rule can help determine if the direction of the B field will intersect the Hall cell in a way that might impact the measurement. Another unusual effect seen with transducers utilizing a square magnetic circuit is flux leakage. The magnetic field wants to manifest as a circle. The square magnetic circuit allows for ‘leakage’ of flux and reduced flux with respect to the primary current as seen by the Hall cell. This becomes more pronounced as the current increases towards the maximum linear capability of the core. Ferromagnetic material near the Hall cell can cause flux to manifest outside the line of the magnetic core with the Hall cell in it. This can result in non-linear operation of the transducer. This will not be seen during operation within data-sheet limits. However, a square core transducer operating within its data sheet limits when mounted on a ferro-magnetic material (sheet steel) may exhibit non-linear characteristics beyond that of saturation effects expected when approaching the maximum current
Fig 3. The effects of surrounding ferromagnetic material
Transducer Positioning With Respect to Other Transducers
Placing transducers side by side is not optimal. There should be spacing between transducers or the transducers should be staggered. This prevents the fields created by the primary conductors from interacting with nearby transducers. This spacing or staggering, combined with respecting the Hall cell position within the transducer, will result in better current measurements.
Fig 4. Positioning of transducers with respect to each other
PCB Mount Transducer Heat Dissipation
When observing the cross sectional area of the primary bus bar in a PCB mount current transducer, it becomes apparent that thermal dissipation is the limiting factor. The copper can handle the current (75A/mm2) if the heat can be dissipated. Normally the designer would not push the limits with heat. However, the size of the transducer is important. Typically, the smaller the transducer size, the less space and cost. If the heat can be removed, an LEM HLSR 50-P can measure 150A continuously. That is a significant capability in a device the size of a postage stamp. Even the 200uOhm of resistance of the HLSR’s busbar requires removal of the heat. Since all heat is moved by either conduction, convection or radiation, optimizing for one or two of the three is best. The temperatures involved preclude much in the way of radiation being involved. Convection will be improved by adding a fan and moving air across the transducer and its nearby primary conductor planes on the PCB. Therefore, conduction from the primary bus bar to the PCB and convection will remove the heat from the PCB. Many times, the primary conductor traces on the PCB are minimized. By increasing the size of the primary conductor traces, more heat can be removed. There is a trade off between size of the primary bus bar/transducer and the amount of surface area of trace that is available for heat removal. Going for the absolute minimum connection traces to the transducer is probably sub-optimal.
Conclusion
Implementation of a current transducer is typically a straightforward affair. In the event that the output is not as expected, it must be understood that the source of the challenge may be rooted in the mechanical, magnetic or electric nature of the device. The interaction between the different disciplines can result in symptoms that can be difficult to diagnose. By understanding some of the implementation phenomena presented here, it will make finding a solution less time consuming. Please keep in mind that transducers use different magnetic core materials with different linearities and saturation characteristics. The numbers given above in the examples are in percentage of full scale and can vary by material and method of compensation (Open vs Closed). However the numbers given will stay well within an order of magnitude of the number given.
Many of these phenomena are taken into account in the transducer design process. A rigorous design process will attenuate many of these effects. A ‘me too’ product or a manufacturer with a less robust engineering group may not have a scope of design that covers these phenomena.
About LEM
LEM is a market leader in providing innovative and high quality solutions for measuring electrical parameters. Its core products – current and voltage transducers - are used in a broad range of applications in industrial, traction, energy and automotive markets. LEM’s strategy is to exploit the intrinsic strengths of its core business, and develop opportunities in new markets with new applications. Together with production plants in Geneva (Switzerland), Machida (Japan), Beijing, (China) and our regional sales offices, LEM offers a seamless worldwide service. LEM has been listed on the SIX Swiss Exchange since 1986. The company’s ticker symbol is LEHN.
The content & opinions in this article are the author’s and do not necessarily represent the views of RoboticsTomorrow
Comments (0)
This post does not have any comments. Be the first to leave a comment below.
Featured Product
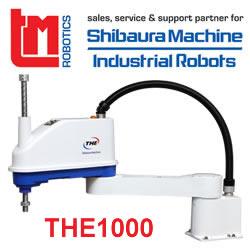