As manufacturers adopt smart manufacturing, robotic systems are getting a lot of attention; however, the engineering and expertise required to design these systems is holding back many manufacturers.
Contributed by | NEXCOM
Robotics are playing a major role in making manufacturing processes more productive and less labor intensive, which is especially important in China, where there is a labor shortage in some regions. But impeding many manufacturers is the complexity of robotic system design, which is made more difficult by the need to identify and integrate subsystems from multiple vendors.
Greatly simplifying the robotic design process, NEXCOM, working closely with various solution providers, developed pre-integrated and pre-validated solutions for a range of robotics applications. NEXCOM controllers based on Intel® processors perform precise robotics control and run essential industrial application software. This paper describes several robotics use cases and corresponding proven designs that use components from NEXCOM, Intel, and other vendors.
Smart Factory
Robotics is a perfect example of the move to computerize industrial manufacturing and the smart factory vision put forward by Industry 4.0 and the Internet of Things (IoT). Almost all aspects are digitized, spanning machine control, monitoring, management, and data reporting and analysis. Even operators interact with machines digitally using a human machine interface (HMI).
The smart factory provides many benefits, including a reduction in operator hours and opportunities to increase throughput, boost yields, improve efficiency, and reduce downtime through insights gained from advanced data analytics. Read an Intel solution blueprint to learn about a real-world example.
Robotic System Components
A robotic production line involves many aspects beyond the robots, some of which can be challenging. There are actuation controls, sensing, data processing, and operational intelligence that may present issues around system integration, machine-to-machine communication, and information integration. Taken a step further, smart manufacturing based on IoT, smart robots, cyber-physical systems, and big data technologies introduce additional layers of complexity.
Although robotics systems come in all shapes and sizes, they will typically include the types of subsystems shown in Figure 1 and described in the following:
Figure 1. Typical Robotic System Components
Robot Body
Made of high-strength materials and designed for harsh environments, the robot body plays a “hands on” role in the manufacturing of goods by performing tasks, such as welding, painting, packaging, inspecting, etc.
Robotic Control
Robot control systems are typically responsible for sensing, motor driving, and movement functions that require sophisticated algorithms. The design of these rather complicated systems also requires vast experience in remote teaching, application know-how, and networking technology suited to industrial environments (e.g., EtherCAT). Control system components may include:
- Controller: PC-based system controlling the robot body.
- Algorithms: Application software running on the controller.
- Teach Pendant: Input device (HMI) enabling process control customization.
- Communications: Devices supporting advanced communications capabilities (e.g., EtherCAT).
Devices and Equipment
In addition to the robotics, other systems are needed to complete the production line, and some examples are:
- Remote I/O: Peripheral devices communicating with sensors, actuators, networks, etc.
- HMI: Panel PCs enabling operators to interact with the production equipment.
- Conveying System: A variety of equipment for moving goods along the production line.
Distributed Control System
This architecture is used to flexibly connect distributed I/Os, sensors, and drives so developers can implement robot design without concern for signal wiring length limitations.
Domain Know-How
In addition to robotics, production lines may require special functions, such as vision inspection, that require particular expertise.
Robotics Deployment: Wet Wipes Production
A company producing wet wipes required between 12 and 15 workers for each production line, with eight of them performing detail-oriented packing tasks. Seeking to reduce the labor content, the company turned to NEXCOM to design an automated system, comprising delta robots and EtherCAT master stations to coordinate PLCs, conveyers, sensors, gluing, and labeling equipment (Figure 2).
Figure 2. Wet Wipes Production Line
The automated system, depicted in Figure 3, is expected to reduce manpower requirements by about thirty percent. The company is planning to replicate this model to other assembly lines for different products in order to duplicate their success.
Figure 3. Wet Wipes Robotics Solution
The solution contained many of the components previously listed, which are described in more detail in the following:
Robot Body
Hiwin RD403 is a four-axis parallel robot utilizing a parallel linkage mechanism to perform extremely high-speed motions with stability, high accuracy, and a short cycle time. Applications include pick-and-place, assembly, alignment, and packaging.
Robotic Control
Controller: NEXCOM IPPC 1632P, based on Intel® Atom™ processor, controls auto-pasting process, gathers system information, and serves as the HMI of the auto-pasting system. The IPPC 1632P controls two conveyors—one transports wet wipe packs and the other feeds covers, determines the position and orientation of wet wipe packs with machine vision, and sends the information to the NEXCOM NISE 3600E controlling the delta robot. The NISE 3600E, based on the Intel® Core™ i5 processor, is designed for graphics-intensive and computing oriented applications, including object tracking and robot control.
Algorithm: NEXCOM-supplied algorithms define a moving path for the delta robot to make sure a cover is pasted in the right place on the pack.
Communications: NISE 3600E serving as an EtherCAT master station is installed with NEXCOM nexECM to allow for robot control programming; IPPC 1632P is installed with Codesys software to control the conveyors.
Teach Pendant: Hiwin system.
Drive and Motor: Panasonic Minas A5B Series server motor driver offers unique features such as safety functions, a fast frequency response of 2.4 kHz, a minimum cycle time of 250 us, and real-time communications, which contribute to high overall system performance and reliability.
Device and Equipment
Application Specific: The assembly requires a conveying system and mechanical engineering support, which was provided by a partner.
Human Machine Interface (HMI): NEXCOM IPPC 1632P panel PC, based on Intel® Atom™ processor D2550, has a 15.6-inch widescreen multi-touch monitor to show the status of the system, including robot and conveyors, and provides information required by NISE 3600E to calculate a moving path for the delta robot. The JMobile software offers full vector graphic capabilities and many connectivity options.
Remote I/O: NEXCOM AXE-9200 is a digital I/O module with 16 inputs and 16 digital outputs.
Distributed Control System
Industry-standard EtherCAT supports distributed control.
Domain Know-How
Customer provides auto giving and paste on-the-fly expertise.
Other Robotic System Examples
In addition to the previously discussed wet wipe making deployment, Table 1 provides a list of key components for seven pre-integrated and pre-validated robotics solutions supported by NEXCOM. Here is a brief summary of the applications.
Intelligent Robot Controller: The NEXCOM NISE 104 supports 4- to 7-axes robots with payloads from 5-300 kilograms.
Automobile painting: Three hundred robotic systems have been installed in an automaker’s car painting line.
Gantry: A 6-axes, high-speed system supports machining devices travelling on a frame.
Subsystem |
Component |
Application |
|||
Wet Wipe Making |
Intelligent Robot Controller |
Auto Painting |
Gantry |
||
Domain Know-How |
Auto Giving and Paste on-the-fly |
Robotic Control |
Auto Painting |
Advanced Motion Control |
|
Robot Body |
Hiwin* RD403 |
Third-party 7-Axes Robot |
KUKA* KR 16-3 L8/ KR 100 TITAN |
6-Axes Gantry |
|
Robotic Control |
Controller |
NEXCOM* NET 3600E |
NEXCOM NISE 104/105 |
Siemens S7-300 |
NEXCOM NISE 3140 |
Algorithm |
NEXCOM |
Third-party |
KUKA |
TwinCAT |
|
Communications |
EtherCAT (NEXCOM nexECM) |
Third-party |
Ethernet |
EtherCAT |
|
Teach Pendant |
Hiwin |
Third-party |
KUKA |
N/A |
|
Drive and Motor |
Panasonic* A5B |
KUKA |
HIWIN D2 |
||
Device and Equipment |
Application Specific |
Conveying System and ME Partner |
Customer Choice |
Car Painting |
Conveying System |
HMI |
NEXCOM IPPC 1632P |
Rockwell* RSLogix 5000 |
NISE 2100A |
N/A |
|
Remote I/O |
NEXCOM AXE-9200 |
Siemens PLC |
VIPA I/O |
||
Distributed Control System |
Controller |
NEXCOM IPPC 1632P |
NEXCOM NISE 104/105 |
NEXCOM NISE 2100A |
NEXCOM NISE 3140 |
Communication |
EtherCAT CODESYS* |
Ethernet/IP |
Ethernet |
EtherCAT |
PC-based DCS and Robotic Arms
Seeking a higher level of automation in manufacturing of smartphone chassis, electronics contract manufacturers often employ PC-based distributed control systems (DCS) and robotic arms (Figure 4). Commonly used in electronics manufacturing for process flow control, a PC-based DCS closely monitors and controls the surface treatment process. As the process involves a series of complicated chemical reactions, the DCS keeps a close eye on values of the process variables, and throughout the process, adjusts inlets and outlets accordingly, ensuring quality outcomes.
In the cutting process, two types of robotic arms are collaborating with NIFE 100-enabled CNC machines, per Industry 4.0 smart manufacturing, to deliver efficiency improvements and assure high quality. To reduce machine idle time, a NIFE 100-enabled CNC machine notifies the pick-and-place robot when a cutting cycle is about to finish so the robot picks up the finished piece and places another workflow. The finished piece is then transported to a 6-axis robot for quality inspection. If a defect is identified, the 6-axis robot, based on NEXCOM NISE 3600 controller, traces the piece back to the CNC machine cutting the piece and tracks the machine’s subsequent output quality. If defects persist, the 6-axes robot provides feedback to the CNC machine so the CNC machine can make an adjustment. If necessary, the 6-axis robot requests a CNC knife replacement.
Figure 4. Industry 4.0 Example: Electronics Manufacturing
Why Intel?
NEXCOM takes advantage of the tremendous scalability Intel® processors offer by creating a family of controllers that run the same code base and satisfy multiple cost/performance (C/P) points. For example, the high-end NISE 3600E is a fanless system with Intel® Core™ i7, Intel® Core™ i5, and Intel® Core™ i3 processor options.
Still powerful enough to address the computation, communication, and control requirements in many manufacturing environments, the NEXCOM NIFE 100 is designed with the power-efficient Intel® Atom™ processor E3800 product family. The NIFE 100 controller may run the Intel® IoT Gateway software stack, developed in collaboration with McAfee and Wind River. The controller can connect to legacy and new industrial devices, thereby enabling seamless and secure data flow between field devices and the cloud. The Intel IoT Gateway software stack, on which application-specific software can run, integrates technologies and protocols for networking, embedded control, enterprise-grade security, and manageability.
NEXCOM also chooses Intel processor-based components for other reasons, including performance, long-life support, generational compatibility, and scalability. Moreover, multi-core Intel processors run at high clock speed and can perform multiple jobs simultaneously – carrying out a major task with one computing core, while performing additional tasks on the other cores. This enables one Intel processor to replace several legacy processors, improving the overall C/P value of the solution.
For robotics solutions requiring vision, Intel® RealSense™ Technology takes perceptual computing to the next level by understanding sensory input and movement-supported platforms. It supports facial and speech recognition, speech synthesis, and a depth sensor that enables operation in a 3-D space, such as detecting and avoiding obstacles, and planning a collision-free path.
NEXCOM follows the Intel® Embedded Product Roadmap, benefiting from the Intel commitment to long-time product availability. This enables NEXCOM customers to reduce inventory for the typical 10-year life cycle of robotics controllers.
Since NEXCOM’s solutions employs Intel® processors end-to-end, from edge devices to cloud servers, the same development, validation, and test tools can be used throughout, which reduces costs and streamlines these engineering tasks.
NEXCOM Simplifies Robotics System Design
As manufacturers adopt smart manufacturing, robotic systems are getting a lot of attention; however, the engineering and expertise required to design these systems is holding back many manufacturers. NEXCOM solves this problem by offering pre-integrated and pre-validated solutions for a range of robotics applications that incorporate components many leading vendors. NEXCOM will also install the robotics systems in factories per customer request. Now manufacturers can deploy robotics systems with much less development effort and risk, thereby making their manufacturing processes more productive and less labor intensive.
Resources
Intel® Internet of Things Solutions Alliance
Members of the Intel® Internet of Things Solutions Alliance provide the hardware, software, firmware, tools, and systems integration that developers need to take a leading role in IoT.
Intel® IoT Gateway Development Kits
Intel® IoT Gateway development kits enable solution providers to quickly develop, prototype, and deploy intelligent gateways. Available for purchase from several vendors, the kits also maintain interoperability between new intelligent infrastructure and legacy systems, including sensors and data center servers.
For more information about NEXCOM solutions for machine automation, visit www.nexcom.com/applications/DetailByDivision/machine-automation.
Read more about Intel’s Automation Technologies for the Internet of Things www.intel.com/iot/industrial
*Other names and brands may be claimed as the property of others.
The content & opinions in this article are the author’s and do not necessarily represent the views of RoboticsTomorrow
Comments (0)
This post does not have any comments. Be the first to leave a comment below.
Featured Product
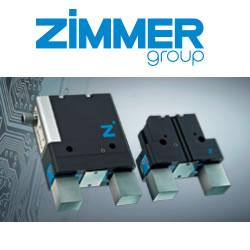