Because kinetic mesh is a mobile network, radios can go on any fixed or mobile asset on a manufacturing floor and still provide constant communications.
Artificial Intelligence in the Factory
Geoff Smith | Rajant Corp
Please tell us a bit about your company and its role in the manufacturing industry.
Rajant is a technology innovation company with a focus on delivering leading-edge wireless network solutions that address many of the challenges and deficiencies of modern day Wi-Fi. Headquartered outside Philadelphia, Rajant’s small but highly productive team of developers, engineers, sales and marketing, and support teams all share in the vision of enabling industrial enterprises to implement wireless network infrastructures that ensure highly reliable, scalable and secure communications while delivering on the promises of today’s IIoT.
Incorporated in 2003, Rajant’s Kinetic Mesh® networks are made up of intelligent nodes called BreadCrumbs, which are powered by its proprietary InstaMesh® protocol. These networks have been successfully deployed across the globe and offer customers sustainable investments that change the way they deliver voice, video and data, while bringing real-time data to streamline operations and positively impact decision making.
Rajant is significant for the manufacturing industry because it offers the only technology that supports truly mobile networks.
Other network technologies require fixed cell towers; even Wi-Fi has fixed access points; clients can roam, but the infrastructure cannot. In a Rajant network, everything can roam, which provides multiple points of connectivity. This is ideal for a manufacturing environment, where everything is always changing, and where all devices, processes, people and machines require constant communications. Because kinetic mesh is a mobile network, radios can go on any fixed or mobile asset on a manufacturing floor and still provide constant communications.
Why should manufacturers want to move to smart factories/IIoT? How will Industry 4.0 change the manufacturing space?
IIoT and smart factories will create efficiency and productivity. Some examples of ways they will do this include:
The sheer volume and variety of products being assembled and distributed means that quality control is becoming more challenging. Rather than relying on humans for in-process inspection and quality control, applications like cameras powered by computer vision algorithms can sense defects immediately and identify what caused the issue. Using smart devices for anomaly detection and automated quality control processes allows manufacturers to identify and resolve failures and problems on hundreds of units in seconds, rather than hours, letting them get ahead of failures before expensive delays pile up.
Predictive maintenance not only represents a promising application for IIoT, but it represents a highly demanded application for many industries and one where the results often contribute important variables that play into the ROI model for manufacturing processes. Like a car getting its oil changed every three months regardless of how much it’s been driven, industrial equipment is often serviced on a fixed schedule, no matter the operating conditions or hours it’s been through. When equipment servicing is only scheduled based on a calendar or time model and performance variables are not considered, this can result in increased labor costs and creates the risk of unexpected and undiagnosed equipment failures. Once outfitted with sensors and networked with each other, devices can be monitored, analyzed and modeled for improved performance and service.
Demand-driven production is another area where IIoT can help factories thrive. Errors in estimating consumer demand leads to lost revenues, through either stagnant inventory or lost sales. Instead of producing goods reactively, manufacturers can achieve real-time demand visibility by connecting consumer purchases and industrial IIoT.
Safety is another area that will improve. Even though many different devices, machines and people will be moving around a manufacturing floor, sensors will allow everything to be interconnected. Obstructions or safety issues can be spotted immediately and equipment shut down to protect employees.
What do manufacturers need to do to prepare for new automated applications? What should factories and manufacturing plants incorporate into their strategic plans over the next 1-10 years to get ready?
Incorporating two elements into strategic plans will help manufacturers prepare for automated applications and the future.
The first is a focus on edge computing. Edge computing provides machine learning, which takes into account historical machine performance to optimize the machines, so every IoT device can perform more effectively and these improvements can be made in real-time.
Automated applications and connected devices require both edge computing for real-time decisions and cloud computing for network-wide monitoring and optimization. Providing cloud computing allows the entire network to be monitored, so in the same way as edge devices take into account historical performance, cloud computing does the same for the entire network to optimize performance for the entire production floor, for instance. Manufacturing 4.0 implies intelligence and continuous connectivity and monitoring, so machine learning at the edge and in the cloud are both required to provide this new level of intelligence, and secure, reliable, ubiquitous, any-to-any device connectivity is required to enable this.
The second element is a focus on the network infrastructure that allows you to connect all your devices – not just today, but also 10 years from now, when the manufacturing floor will look very different because of the increase of industrial robots and autonomous applications that will be peppered throughout a factory space. It’s important to invest in a network and communications infrastructure that can grow with a business, giving a manufacturer the ability to benefit from cost and efficiency improvements.
What challenges should manufacturers expect as they transition to IoT applications and Industry 4.0?
Artificial intelligence in a factory requires all devices to be connected in a secure manner, enabling both edge computing for real-time decisions and cloud computing. The typical hub-and-spoke architectures of cellular and Wi-Fi will no longer work in an environment where all devices, both fixed and mobile, need to be connected together.
Consider a manufacturing floor where every machine is being monitored in real time and robots carry the finished goods to the warehouse for storage and shipment. This environment is very fluid and dynamic. Robots, forklifts and manufacturing machines all need to be connected to make sure they are monitored for efficiency to avoid downtime, direct the robots to store the finished goods in the right location, and monitor the forklifts to send them to the right location for pickup and shipping – all while monitoring for machine health. Typical hub-and-spoke technologies require lines of sight that are not possible in such a dynamic environment, and thus standard network technologies will create challenges and require a manufacturer to update to an IIoT-ready network.
Another challenge is separating the hype from the reality. There’s been a lot of hype around IIoT, but we don’t even have a strict definition on what it truly is, so it can be challenging to get past the hype to understand what equipment manufacturers and applications exist today that can also help tomorrow.
So much changes so quickly in the Iot/IIoT space – today you have one solution, tomorrow you’ll have another – so another challenge is determining a network solution today based on what’s available that will lay a foundation for future improvements. Plenty of new applications on the horizon aren’t yet on manufacturers’ radars, so it’s to have a network that can increase its capacity in order to handle the application requirements and data capacity of new future solutions. A network that can scale also can handle more and more devices as they get added to the IIoT, ensuring that the network doesn’t slow down as more devices join it.
How can manufacturers overcome the argument that automation and IoT are job-killers?
While some think that robots are going to take jobs away from humans, there is data that actually shows the opposite may be true. The International Federation of Robotics found that one million industrial robots currently in operation have been directly responsible for the creation of about three million jobs in industries such as consumer electronics, food, solar and wind power, and advanced battery manufacturing.
Robots and autonomous applications are able to work in areas unsafe for humans, accomplish tasks that are impossible for humans and perform jobs that are not economically viable in a high-wage economy. They also allow greater precision, let companies to get the most out of their equipment, and ensure efficient business operations. The ultimate goal is straight out of science fiction: letting robots do all the hard and mundane jobs, freeing humans up for higher-level work and more leisure time.
For another perspective, look at the history of this country and how we’ve handled transitional changes in the past. When the automobile was introduced, manufacturers of buggies and carts thought they would be out of work, but the savvy manufacturers transitioned to new industries or transformed their businesses to meet these new challenges. We’ve seen a century of change in industrial jobs and plants, and we’ve seen that jobs and people can evolve, and manufacturers need to be prepared to roll with the punches to stay relevant.
According to PWC in a report about Industry 4.0, “Robust, enterprise-wide data analytics capabilities require significant change.” Can you provide your perspective on this statement?
Changing to prepare for this kind of enterprise-wide analytics capabilities requires edge computing to be able to process all the different sensors, and a communications infrastructure that can support a mass of end-user devices.
Edge computing is still in its early adoption stage – gaining momentum in some industries more so than others – and we’re just beginning to scratch the surface of the level of data analytics provided by access to so many sensors and devices. Manufacturing floors today have some level of communications connectivity, but not to every single device, and businesses will need to change to support edge computing and enterprise-wide data analytics.
How will constant access to real-time data and data analytics improve operations?
Edge computing can find problems in manufacturing process much faster than humans or current analytics programs can; the networks of sensors and devices can analyze events and activities in real time and provide actionable information. This can help eliminate bottlenecks or show a faster or better way of executing a task or function. It’s not just about monitoring sensors to see problems before they happen; it’s also about analyzing the whole process to make significant improvements based on access to real-time data.
What are connectivity/network requirements for automated applications, IoT and smart manufacturing techniques?
Mobility, always-on connectivity, scalability and future-readiness, and capacity are all network requirements for Iot/IIoT.
Mobility is essential because everything in a manufacturing environment – all people, assets, devices and machines – is constantly moving. A network must be able to move with its environment in order to be truly functional.
The need for always-on connectivity is obvious – for all devices and machines to speak to each other, data flow can never stop without risking errors or injuries.
Scalability and future-proofing mean that a network can grow with a business over time without affecting network traffic – more devices and nodes can be accommodated without impacting network performance and reliability. This ensures the network will work for a manufacturer both now and in the future.
Capacity on all networks will continue to increase over time, especially as more edge devices join a network. Data transmissions/packets will creep from kilobytes to megabytes, so having a network infrastructure that can expand and support that capacity increase is important as well.
About Geoff Smith
Geoff Smith started his career at AT&T Bell Labs developing high speed modem technologies. He has led Modem, DSL and Wireless R&D teams prior to joining Proxim Wireless in 2000 where he held senior executive positions managing R&D, Sales and Marketing enabling indoor and outdoor mobile internet. In 2015, Mr. Smith founded Wave Mobile Solutions, a DSRC V2X radio company focused on Connected and Autonomous Vehicles. He joined Rajant in late 2016 as IIoT strategist and EVP of sales and marketing.
The content & opinions in this article are the author’s and do not necessarily represent the views of RoboticsTomorrow
Comments (0)
This post does not have any comments. Be the first to leave a comment below.
Featured Product
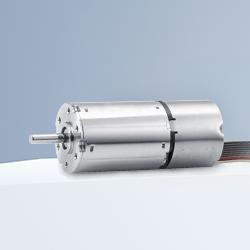