Companies recognize that maintaining a safe work environment is just as important as increasing productivity. Its maximizing the safety and efficiency of a facility that matters most, and SDVs are a tool both manufacturers and warehouses can use to makes this possible
Contributed by | OTTO Motors
Technology has made a significant impact on operational efficiency in factories, distribution centers, and warehouses. Automation through the use of self-driving vehicles has specifically made a difference in material handling. But there is another important benefit to self-driving technology - safety. Self-driving vehicles can create an ideal mix of process improvements and a safer workplace for employees.
Safety First
"We think there's a lot of areas where robots can lend additional safety to factories. They don't get tired or cut corners, and it’s always been a general condition of ours to maintain that benefit, so that we are not only helping with productivity, but also building a safer solution." - Ryan Gariepy
A primary goal of any industrial environment is to provide safe working conditions. Aside from being the right thing to do, it’s a prudent business decision. Unfortunately, accidents with forklifts, racking, and other material handling equipment are common in factories and warehouses.
Plus, ergonomic issues such as strain, overexertion, and heavy lifting, can lead to employee time off and overall higher costs for the employer. Understanding this, many manufacturers continually look for ways to reduce physical stress on workers with the intent of preventing work-related injuries and other problems.
Another deterrent can be the direct financial cost of an unsafe working environment. OSHA penalties for workplace hazards can range from $7,000 for smaller violations up to $70,000 for repeat offenders.
An engaged and happy employee contributes to a safer and more productive workforce as well. A study conducted by Gallup found that the top 25% of the teams they studied (those identified as “most engaged”) had 50% fewer workplace incidents. These employees were also less likely to call out sick or leave the job. When a safe workplace is maintained, the business enjoys the added benefit of satisfied employees - and a stable workforce.
Hazards
A warehouse or distribution center can be full of hazards. According to OSHA, the fatal injury rate for the warehouse industry is higher than the national average for all industries. Causes of accidental injuries can come about from the unsafe use of forklifts, incorrect materials stacking, and failure to use personal protective equipment. Each is a specific function improved or avoided through automation.
There are 96,785 accidents per year related to forklifts. Compared to the estimated number of forklifts in the United States (855,900), that means that each year, more than 1 in 10 forklifts are involved in an accident.
The dock is one area in particular in a warehouse where employees are at risk for sustaining serious injuries. The American Supply Association states that 25% of all industrial accidents happen in this location of the facility, many of which are due to forklifts. OSHA’s dock-related accident report cited common accidents as being fractured legs from being hit by dock plates or falling/ driving off the dock. The control and predictability of SDVs in this specific work location has obvious benefits for individuals and the company.
Self-driving vehicles and other material handling automation can also have applications for preventing other types of injuries that may happen over time, such as from repeatedly reaching into hard-to-get-to storage shelves, lifting heavy boxes onto pallets, or other repetitive use problems.
The Need for Speed
“Our self-driving vehicles could go even faster. OTTO software and hardware allows for significantly faster speeds but for safety reasons, constraints have been put on them. OTTO is designed to work alongside humans, not to race them.” - Ryan Gariepy
Making matters worse for manufacturers and distribution center operators with regards to safety is the general market trend towards greater supply chain velocity. Everything needs to get done faster today - from sourcing to production to shipping - but doing so can create all types of safety risks for employees.
As throughput increases, it can become harder for human workers to physically keep up with certain tasks. Most material handling and production operations require machine to worker handoffs at various points so this is unavoidable. An example could be when a pallet of finished product is complete and must be moved to shipping. An employee with a hand truck or forklift can perform the task, but a properly used SDV can do so more safely and reliably. Forced to move, say, twice the pallets because of faster production creates even greater pressure that can lead to poor decision making by employees when it comes to safety. Higher expectations, and unrealistic quotas, will inevitably have negative consequences and when there is pressure to perform. It’s often safety that gets pushed aside first.
Safe Self-Driving Vehicles
“When an accident happens in an industrial environment with a forklift, there isn’t an immediate thought to remove all forklifts from use. With self-driving vehicles, we want to do even better than that. We want to ensure there are no accidents that ever call into question the safety of our vehicles.” - Ryan Gariepy
Self-driving vehicles can play a key role for companies looking to safely bridge these types of gaps in workflows and other unsafe situations in their operations. It’s a technology perfectly designed for many of the tasks in production and warehouse that put employees most at risk, but the vehicles themselves can integrate seamlessly, and safely, with employees everywhere in the work environment too.
This is possible because self-driving vehicles used as part of the material handling function or anywhere else are fully aware of what’s going on around them. They can see, react, and avoid the people and circumstances around them - creating a safer environment even as the speed of production continues to increase.
Companies recognize that maintaining a safe work environment is just as important as increasing productivity. Ultimately, it’s maximizing the safety and efficiency of a facility that matters most, and SDVs are a tool both manufacturers and warehouses can use to makes this possible.
Published with permission from the OTTO MOTORS blog.
The content & opinions in this article are the author’s and do not necessarily represent the views of RoboticsTomorrow
Comments (0)
This post does not have any comments. Be the first to leave a comment below.
Featured Product
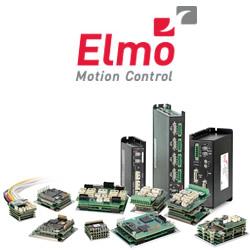