The iTENDO is the worlds first intelligent toolholder with real-time process control. In an interview, developers Friedrich Bleicher and Johannes Ketterer explain how the embedded systems solution makes production smart and economical.
A Prime Example for Industry 4.0
Friedrich Bleicher, Johannes Ketterer | Schunk
The iTENDO is the world’s first intelligent toolholder with real-time process control. In an interview, developers Friedrich Bleicher and Johannes Ketterer explain how the embedded systems solution makes production smart and economical.
Why do companies need intelligent solutions for the machine tool?
Bleicher: In automated production in small batch sizes, you cannot know exactly how long you can use a tool until the end of its life has been reached. So companies tend to replace it prematurely. In so doing, they are losing out on 30 to 50 percent of its service life − and in so doing are throwing a lot of money right out of the window! Intelligent solutions based on integrated electronics and sensor technology make it possible to make much better use of the tool, and eliminate such waste. If something unusual happens in the process, the intelligent solution intervenes, makes the process more stable or stops it if needs be. This way, the customer can increase the profitability of their manufacturing processes enormously.
Why did you integrate the sensors into the toolholder?
Bleicher: If the machine is to intervene in the process, we must give it feeling, and bring the sensors as close as possible to the machining process. The logical consequence for us was to integrate sensor technology into the toolholder mountings. Because the closer to the effective working area we record data, the more sensitively the sensors are able to react to it.
How does the iTENDO implement Industry 4.0 in the company?
Bleicher: The iTENDO measures via the built-in sensors accelerations and vibrations directly on the workpiece and transfers the data to the machine control. This can then react in real time and influence the cutting process. If for instance the smart toolholder detects that the tool is driving at the limit, the machine control system intervenes without the need for any human intervention and adequately adjusts the process. So it can prevent excessive tool wear or a machine crash. The iTENDO is the solution that integrates sensors and logics and thus facilitates autonomous action of an automated system in the manufacturing process. It makes the decisions itself and implements them autonomously. In so doing, it brings intelligence into production and is a prime example of Industry 4.0.
What advantages does the iTENDO have over other intelligent solutions in the market, for example process monitoring systems or Industry 4.0-enabled machine tools?
Ketterer: On the market, there are several components equipped with sensors, some of which are also capable of running evaluations or identifying trends with the data. However, the iTENDO is the only component that is capable of autonomously intervening in the process. It goes much further than other systems that only display process information. And it goes far beyond what most people currently associate with Industry 4.0. Compared to other systems and technology providers, it is also considerably cheaper. The “intelligence” of the iTENDO can also be modularly integrated into a large proportion of the existing SCHUNK total tooling toolholder portfolio, and therefore facilitates a wide range of applications in machining regardless of machine type and process. Finally, the iTENDO can be upgraded at any time to all common machine tool control systems.
Where can the iTENDO be used?
Bleicher: In general, companies can use the iTENDO on all machine tools. However, it really demonstrates its strengths in processes with strong fluctuations due to the material or ambient conditions, the production of very expensive components or in processes with high tool wear. Examples of this are the production of very thin-walled components, very expensive components for the aerospace sector, where you have to make sure that there are no rejects, and rough machining of high-strength or hardened materials.
Where is the data stored and where can the customer see it?
Ketterer: The data is exclusively stored locally on the machine; it does not leave the plant. With the app provided, customers can view it on all electronic devices – PC, tablet or mobile phone, and use it for parameterization and trend analysis.
Let’s take another look into the future: what’s the next step?
Ketterer: We need to develop the logic so that we can soon autonomously optimize all processes – be they finishing, roughing or deep hole drilling. To do this, we must teach the logic how it should react to certain process specifics. This will allow machines to produce even more autonomously and efficiently in the future and down to batch size 1.
The content & opinions in this article are the author’s and do not necessarily represent the views of RoboticsTomorrow
Comments (0)
This post does not have any comments. Be the first to leave a comment below.
Featured Product
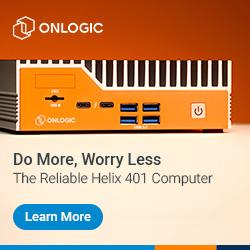