When separating aluminum sheets prior to loading into the press, they can stick together due to a suction effect that occurs as the sheets are lifted. Most methods for destacking aluminum are very slow compared to steel destacking ...
Güdel Integrates Tool Changers in Multi-Purpose Metal Forming Solution
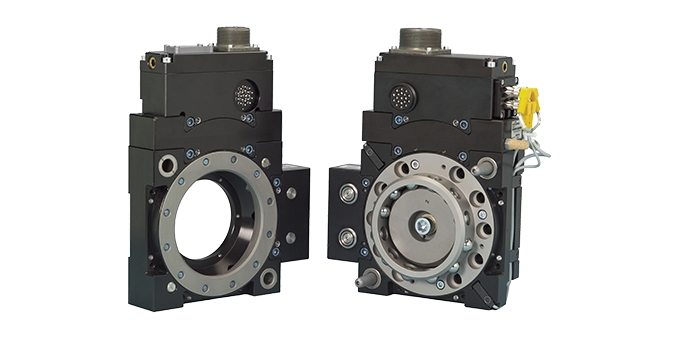
Contributed by | ATI Industrial Automation
Güdel specializes in designing and developing intelligent technologies for motion. Since 1954, Güdel has served the automotive, aerospace, logistics, heavy industrial, and power generation industries with a wide variety of motion solutions. Their mission is to bring the concept of flow into industrial automation.
One-piece flow is a goal of many automated processes; it allows for just-in-time production without excess inventory, enabling high responsiveness to changes in demand. When one of Güdel's customers, a major automotive manufacturer, experienced a surge in demand for aluminum automotive components, Güdel was challenged to create a more seamless process for working with aluminum vehicle components.
There are many advantages of using aluminum automotive components as their high strength, but lower weight can improve vehicle performance and gas mileage. One of the drawbacks includes high cycle times of forming processes. When separating aluminum sheets prior to loading into the press, they can stick together due to a suction effect that occurs as the sheets are lifted. Most methods for destacking aluminum are very slow compared to steel destacking and often result in lower throughput for the same duration of production.
Güdel wanted to help automotive customers increase capacity and devised a destacking solution to accelerate blank separation. They reconfigured the popoular suction cup design and included a pneumatic blast; the resulting destacking device lifts the top aluminum blank asymmetrically, while the puff of air discards additional sheets that may be stuck to it. This prevents multiple sheets from accidentally getting loaded into, and potentially damaging, the forming machine.
Güdel didn't stop there—they implemented ATI Industrial Automation's Tool Changers into the system to allow customers to destack both aluminum and traditional steel blanks in the same machine. The respective aluminum and steel destacking devices are mounted to ATI Tool Changers and exchanged automatically to accommodate either type of material. The system prioritizes the flexibility of Güdel's automotive customers and has led to significant increases in productivity. With this system, manufacturers can process 18 parts per minute while the industry standard hovers around 12.
Instead of multiple metal forming machines to accommodate steel and aluminum, Güdel delivered a time- and space-saving solution that does both. This new hybrid sheet destacking solution allows users to realize high throughput with quick changeover between materials. For automotive manufacturers, it provides better process flow and minimizes human-machine interaction. Switching from aluminum blanks to steel during production, with minimal downtime, increases profitability for Güdel's metal-forming customers.
Brenda Crampton is the Manager of Systems Proposals for Güdel, and is keenly aware of the value ATI Tool Changers contribute. She cites ATI's proven reliability and robustness, mentioning, "They have been designed to withstand the rigors of automation setup and connectivity misalignment, and perform with high repeatability throughout production." Güdel and its customers experience less downtime-related repairs and delays as a result of using ATI’s Tool Changers. She goes on to say, "The reliable changeover is worth much more than just the cost of the ATI assembly."
Both ATI and Güdel have built reputations on superior quality and strive to provide customers with low-maintenance solutions that encourage higher levels of efficiency and productivity. By implementing ATI Tool Changers, Güdel transformed their metal destacking application into a multi-media forming solution and increased the system's value for users.
Güdel's destacking tools exchanged automatically with ATI's Heavy Duty Tool Changer.
The content & opinions in this article are the author’s and do not necessarily represent the views of RoboticsTomorrow
Comments (0)
This post does not have any comments. Be the first to leave a comment below.
Featured Product
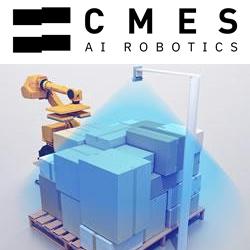