For manufacturers, the reliability of the quality control of industrial parts of all kinds is crucial, because defective parts due to non-conformity have serious effects on production performance.
IDS Imaging Case Study - Automatic Quality Control in Car Body Construction in Real Time
Case Study from | IDS Imaging Development Systems
In the automotive industry, bonding has become a key technology that is increasingly replacing other joining technologies. Both engine and body parts are bonded, and for good reason: bonded cars generally perform better in crash tests than welded cars - provided the quality of the components and bonded areas is flawless. Modern adhesive systems have thus become a safety factor in the automotive industry. For manufacturers, the reliability of the quality control of industrial parts of all kinds is crucial, because defective parts due to non-conformity have serious effects on production performance.
Higher costs, longer production and delivery times, greater risks and a possible damage to one’s image are just a few of them. But because the human eye is fallible, defects or anomalies are easily overlooked. Automatic search for nonconformities thus holds great potential.
The French company PRODEO, based in Caen, has developed an innovative digital solution in this context. The CAMEO system enables automated image acquisition, file management and image storage as well as real-time image processing and quality diagnosis - directly at the production site.
CAMEO precisely validates components with regard to their geometric conformity as specified by CSR (Compliance, Safety, Regulation) and documents the control result. The individual components are photographed during the production process. They are verified in real time to ensure that they meet the relevant legal, safety and quality requirements. A reliable image processing solution as well as a special file management provide for the evaluation of the images and enable the results of the image analysis to flow directly into the production process.
Application:
CAMEO was initially developed for the automotive industry, for example to check compliance with the so-called manual bead application of adhesives. Manufacturers such as RENAULT ALPINE, RENAULT NISSAN, VOLVO TRUCKS and CARL have already implemented CAMEO and use it especially in the construction of car body components.
Figure 1 Image capture for components of VOLVO trucks
The system works autonomously. The system components such as mast, camera with protected optics, computing unit, screen and keyboard are completely integrated. CAMEO can be connected to a backup network for long-term backup of diagnostic data. The configuration is carried out with customer-specific image processing algorithms to optimize the image evaluation and thus enables the best possible reference for part inspection
Figure 2 CAMEO image processing system with USB 3 uEye ML
User-friendly system:
Usability played a major role in the development of the system: The user interface of the software is easy and intuitive to use. The operator can start CAMEO control at the touch of a button. Image processing takes place immediately after acquisition, and the diagnosis of deviations is recorded in real time and displayed on the screen. The diagnostic data and photos are stored in the software. Specific naming, local archiving and special network functions contribute to data security.
Figure 3 Results of the CAMEO test software: Green lines = compliant
The image processing algorithms use holes and structural points of the components as reference for checking the dimensional accuracy. "The bead position of the adhesive is calculated relative to these references. Due to the high resolution of the camera we are able to check presence, position and dimensional accuracy, especially the width, every 0.7 mm. For this we only need to take a single picture. This avoids post-processing and above all increases the quality and thus the safety of the end product, in this case the vehicle body," explains Georges LAMY AU ROUSSEAU, Director of Image Processing at PRODEO. CAMEO minimizes the manufacturer's risk considerably by the conscientious collection of control certificates and the traceability of the products. In order to maximise the performance of the system, PRODEO has opted for image capture by IDS cameras.
Cameras:
"uEye cameras from IDS are especially adapted to our industrial needs due to their wide range of applications on the same software basis," underlines LAMY AU ROUSSEAU. A mixed operation of USB 2.0, USB 3.0 and GigE uEye cameras is possible without any problems because the IDS Software Suite is an identical software package for all IDS cameras.
Due to the large number of housing and on-board level variants, it is possible to select the camera model according to the available space and the configuration of the integration environment. In addition, many matching C-mount or CS-mount lenses are available. The various IDS camera series each offer a range of powerful sensors and thus high frame rates and resolutions as well as numerous additional functions.
IDS' USB2, USB3 and GigE camera communication protocols enable both local use and integration into complex multi-camera systems where multiple cameras are used simultaneously. Thanks to the software tools included in the SDK, system prototyping can be performed independently of the selected camera model.
This saves valuable time, because the communication protocol is not stopped when switching from one camera model to another or when mixing different camera models. The downward-compatible software package, which is identical for all uEye cameras, enables exchange or mixed operation without changing a single programming line.
The current system solution primarily uses the model USB 3 uEye ML (UI-3580-ML) .This easy-to-integrate compact camera for equipment and machine construction is lightweight yet stable: Weighing in at only 41 g with a size of 47 x 46 x 28 mm the USB 3 uEye ML is the perfect camera for all space critical applications. Yet the camera also offers all benefits one would expect from a proper industrial camera: a maximum range of applications thanks to comprehensive connectivity. Two GPIOs as well as opto-decoupled trigger and flash outputs are available thanks to an 8-pin Hirose connector. Its C/CS lens mount allows for a great selection of lenses, wide-angles lenses included. Camera integration is particularly easy, based on Plug&Play and USB's one cable solution for data transfer and power supply. It is available either with the IDS Software Suite or with USB3 Vision standard.
Prodeo has developed a sophisticated protection system for the camera: The camera and lens are protected by a sturdy aluminium cover, which is fastened with two simple screws. The system allows the user to position the camera in the desired direction and access the lens adjustment rings (focus and iris).
For Georges LAMY AU ROUSSEAU, the use of IDS cameras in CAMEO image analysis systems is ideal: "The versatility and robustness of these cameras enables us to respond quickly to the requirements of the industrial environment in which they are used.”
Outlook:
The system significantly improves quality assurance by minimizing errors, thus reducing production time, costs and manufacturer risk. "Several major automobile manufacturers are relying on our innovation," emphasizes Georges LAMY AU ROUSSEAU. Bonding will continue to assert itself, LAMY AU ROUSSEAU is not the only one to be sure. And: "Every manual drop application system has the same quality problem that we can solve with our image processing solution.”
But systems such as CAMEO cannot only focus on glued components - such an image processing solution thus becomes a versatile and reliable aid in quality control for manufacturers. Such a simplified and reliable determination of error causes saves time and money. And in this case, at the end of the day, even serves the safety and security on the roads.
Client
French software company PRODEO helps manufacturers accelerate digital transformation. PRODEO develops and implements software for companies with the aim of improving their efficiency and competitiveness by increasing productivity and optimizing production processes. Based on the expertise of five joint planning offices, Prodeo offers a range of digital tools that meet the specific and concrete needs of each individual.
Camera
USB 3 uEye ML - The easy-to-integrate compact camera for equipment and machine construction
Interface: USB 3.0
Name: UI-3580-ML
Sensor type: CMOS
Manufacturer: ON Semiconductor
Frame rate: 15,2 fps
Resolution: 4,92 MPixel
Shutter: Global-Start-Shutter, Rolling-Shutter
Sensor format: 1/2"
Dimensions: 47.0 mm x 46.0 mm x 28.0 mm
Weight: 41 g
Connector: USB 3.0 micro-B, screwable
Applications: Industrial image processing/machine vision, Microscopy, Medical technology, Security, Embedded systems
The content & opinions in this article are the author’s and do not necessarily represent the views of RoboticsTomorrow
Comments (0)
This post does not have any comments. Be the first to leave a comment below.
Featured Product
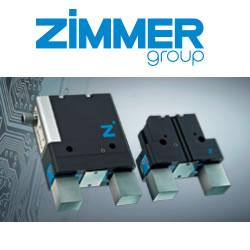