Much like other industries, the automotive industry is changing. With the increase in the variety of vehicle models, variants, and derivatives being produced and the shorter product life cycles in the automotive industry.
Smart Production Lines in Automotive Industry Use Cobots
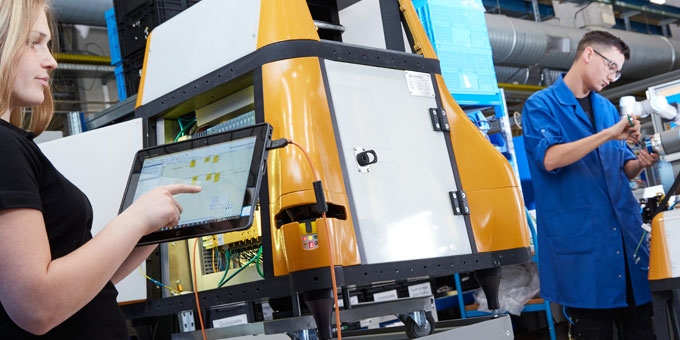
Smart Production Lines in Automotive Industry Use Cobots
Contributed by | SICK USA Blog
Much like other industries, the automotive industry is changing. With the increase in the variety of vehicle models, variants, and derivatives being produced and the shorter product life cycles in the automotive industry. This is causing suppliers like Continental, one of the world’s leading automotive industry suppliers, to take a more dynamic approach. On conventional inflexible production lines, changes or faults at individual stations can have a major impact on the output of the entire line. The more serious the fault, the more difficult it is to compensate for it. This is why Continental has chosen to create smart production lines.
At Continental’s plant in Babenhausen, Hesse, Germany, high-tech components for car dashboards come off the production line at 15-second intervals around the clock. This leaves very little leeway to make up for downtimes. For this reason, Continental is currently replacing its inflexible testing and assembly lines with flexible, redundant, collaborative testing systems by using collaborative robots.
The cobots are named Claus (clever automated universal robot system) and Clara (clever automated robot application). They load the testing machines and can be used wherever needed. If necessary, the employees can help them out. A safety solution from SICK consisting of S300 safety laser scanners, TR4 safety switches, and Flexi Soft software-programmable safety controllers ensures that the employees remain safe in this collaborative environment. There are three test benches on the newly built testing line, which are loaded by the cobots. The cobot takes a component from a conveyor, puts it in the testing machine, then removes the tested part, and places it on the next conveyor.
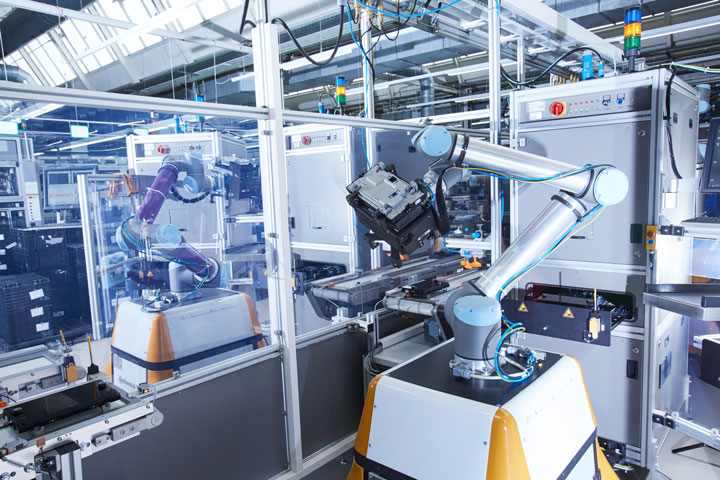
Safety makes human-robot collaboration efficient
“Claus and Clara are semi-mobile, lightweight robots that work in stationary mode, but can be moved around,” explained Heiko Liebisch from the robotics department of the industrial engineering division at Continental, highlighting the benefits of the cobots. “This concept allows us to lift the robots up and move them to another location for a different shift, which means that we can use the same robot on two different machines: one on the early shift and another on the late or night shift.”
Using mechanical indexing, the cobot can be positioned in the ideal location for the testing machine at any time. A TR4 transponder safety switch with a direct unique code sensor verifies the TR4 direct unique code actuator on Claus or Clara.
“Everything in the system that relates to safety is controlled using the Flexi Soft software-programmable safety controller. This means that the Flexi Soft checks whether the coded safety switch is in position. If it isn’t, nothing happens and the safety controller issues an error message. Once the switch has been verified, the safety laser scanners (S300 Advanced) load the field sets that have been stored for the workplace and give the cobot the command to load its program and start work,” said Liebisch, describing the initialization process. “We have the option of fitting several coded switches to the front of the cobots so that we can set them up for several different workplaces.”
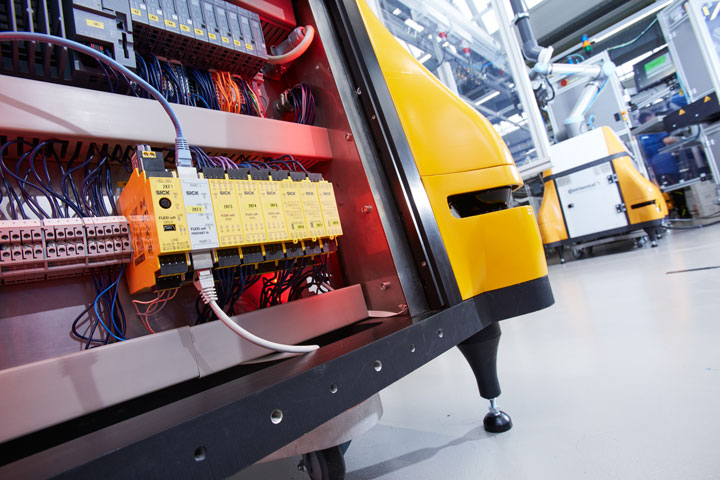
The new production line makes it possible to return rejected test parts to the process while the line is still in operation. An operator goes up to the test machine or the cobot and puts the part down wherever there is space available. The operator then leaves the area and the cobot identifies independently that a part is waiting that needs testing and continues working normally.
The safety laser scanners are installed in a diagonal arrangement to allow for comprehensive monitoring. They also have LEDs in traffic signal colors on the front to indicate the protective fields and any breaches of the fields. To ensure that the operators can see the lights even out of the corner of their eyes, the entire body of the cobot underneath the arm lights up in the traffic signal colors. In collaborative mode, Claus is amber-colored and reduces his speed. In red mode, he comes to a complete standstill. When the operator leaves the red protective field, the system and Claus automatically start up again. The operator does not have to notify the system that he has left the area.
Cobot risk assessment
Although Claus and Clara move relatively slowly, robot arms can come close enough to operators to put their lives at risk.
“You always have to assess the overall concept. This is why the grippers on the front of the robots have been laser-sintered so that there are no sharp edges and everything is rounded off,” said Liebisch.
No two examples of human-robot collaboration (HRC) are the same. This means that an individual risk assessment is needed for an HRC application, even if the robot has been developed specifically to interact with humans, like these cobots, which are designed from the beginning with many inherently safe features. At the same time, the collaboration space also has to meet fundamental requirements, such as minimum distances to neighboring accessible areas where there are potential crushing or pinching hazards. General standards, such as IEC 61508, IEC 62061, and ISO 13849-1/-2, form the foundations for the functional safety of HRC applications. In addition, these systems must also comply with ISO 10218-1/-2, which concerns the safety of industrial robots, and, in particular, ISO TS 15066, which specifies the safety requirements for collaborative robots.
SICK was responsible for advising and training the Continental team on the design, guidelines, legislation, and standards for cobots. “We are very pleased with the system and how it is running,” said Liebisch. “In practice there are a few areas where improvements could be made and we will continue working on these with SICK, our partner for the complete solution.”
Successful pilot line in operation since early 2017
Heiko Liebisch and his colleague, Dejan Pfaff, planned the new smart production line at Continental and designed the cobots. They are the fathers of Claus and Clara, who will soon have siblings in the form of Cora and Kurt. The successful changeover has set a precedent at Continental, which is now planning to introduce more cobots. Claus, Clara, and their fellow cobots are built by apprentices at Continental. The mechanics construct the basic frame and the mechatronics trainees are responsible for the rest.
The content & opinions in this article are the author’s and do not necessarily represent the views of RoboticsTomorrow
Comments (0)
This post does not have any comments. Be the first to leave a comment below.
Featured Product
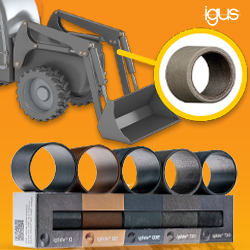
igus® - Free heavy-duty plastic bearings sample box
The iglide® heavy-duty sample box provides a selection of five unique iglide bearings, each suitable for use in heavy-duty equipment due to their self-lubricating, dirt-resistant properties. Each bearing material boasts unique benefits and is best suited for different application conditions, though each can withstand surface pressures of at least 11,603 psi at 68°F.