We’ve talked with many customers who struggled with the cleaning and waste associated with vacuum-based EOAT systems. The air these systems use to attach to a food item is sucked back into the device – and along with it, food particles.
Food Safety in Large Scale Picking of Produce
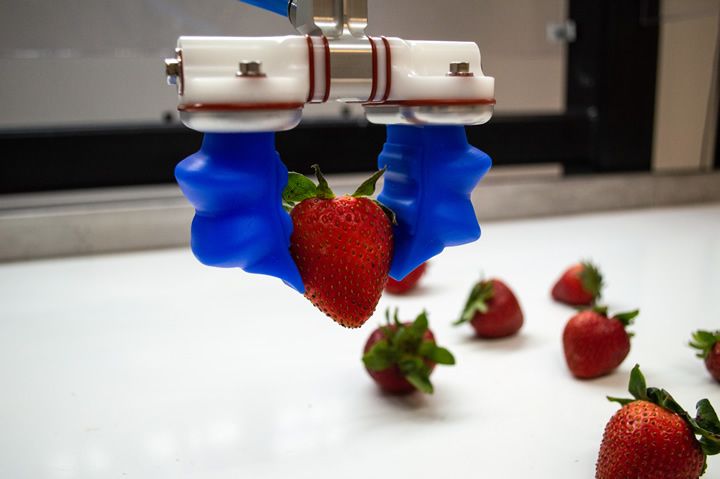
Q&A with Ashley Levesque, Senior Marketing Manager | Soft Robotics Inc.
Tell us about Soft Robotics and your role with the company.
Soft Robotics designs and manufactures advanced technologies which enable our customers to automate the handling of variable products and processes.
Everything starts with our disruptive gripper design. In simplest terms, our technology enables robots to do things they haven’t been able to do before, and automate products and processes that previously were off limits to automation. As the Senior Marketing Manager (Ashley Levesque), I’m responsible for creating and delivering the marketing message to engage our different customer and channel segments on how our technology can deliver immediate ROI. Our technology is different and so is our approach to getting our message out. We’ve developed a bit of a cult following on social media due to our approach to marketing, leveraging the Soft Robotics “Gripper Guys” to deliver edgey, fun & informative marketing pieces on social media and through an email campaign we send on a weekly basis. People can sign up for “The Gripper Guys” right from our website. In addition to this area of responsibility I am also responsible for Demand Generation and Digital Marketing, Marketing Communications, Channel Marketing and Industry Events.
What are some of the challenges with large scale picking of produce when it comes to Food safety and the handling of fragile produce?
The food processing industry presents unique challenges to EOATs in packaging and handling applications. The requirements for chicken handling and processing are very different from muffins or cookies, which are very different from strawberries. Texture, shape, size and density are highly variable across and even within the category as not every strawberry is exactly the same, for example.
There are three main food safety challenges that are of utmost concern to food producers. One: contamination from biological causes such as bacteria, viruses, mold and parasites. Two: there can be cross-contamination due to ineffective or incomplete cleaning. Lastly, foreign matter left in the food product is a safety hazard.
We’ve talked with many customers who struggled with the cleaning and waste associated with vacuum-based EOAT systems. The air these systems use to attach to a food item is sucked back into the device – and along with it, food particles that can be harbored inside breeding bacteria. In addition, as an open loop system, these systems suck up particles of the food product into the overhead system, where, again these particles can breed bacteria, which can be quickly spread throughout the operation. As for handling fragile produce, traditional EOATs poke instruments into a food item in order to pick it up, or use vacuum and suction -- risking damage to the item and more significantly leaving an ingress point in the item where bacteria can enter and transfer possible contamination to the next item handled. You can learn more about the difference between vacuum systems and Soft Robotics systems from this video.
Food Safety has always been important to manufacturers, but it seems to be ever prevalent in today's conversations - why so?
Creating clean and contamination-free production areas that lower the risk of costly food recalls is the driving factor for food safety these days. In 2017, a survey conducted by the Grocery Manufacturers of America found that a single food recall can cost a company, on average, $10 million in direct costs. Far harder to measure, but potentially more devastating, can be the cost to the brand.
Another important factor is the growing pressure of regulations. In the US and the European Union, regulations calling for increased transparency and accountability are on the rise. A third driver is the lack of global labor in the food supply chain. As manufacturers continue to drive their products to market, more and more are turning to automation to stay competitive.
What are you seeing as far as changing needs and demands for Robotic End of Arm Tooling in Food safety?
As labor shortages continue to hamper the food industry, companies are looking for more variety and greater capabilities from their EOATs to further automate operations. This means end effectors that are not only safe, but also can handle items that are delicate or come in non-standard sizes. The human hand can go from picking up a brick to a hammer to an egg without hesitation. Companies are looking for that kind of capability and flexibility in their end effectors.
How would one know if their EOAT is food safe?
Understanding regulations and how to meet their requirements is critical to making the best choice of an EOAT solution. In the United States, the Food and Drug Administration’s (FDA) Title 21 Code of Federal Regulations (21 CFR) sets out the general provisions that are applicable to food contact. Specifically, 21 CFR 175-179 defines what substances may be safely used as components that contact food. The US Food Safety Modernization Act (FSMA) requires that food-processing facilities be able to monitor their compliance with regulations. These facilities commonly request a “Letter of Guaranty” from any food-contact material supplier which assures that the materials used meet the standards defined by the above regulation.
The European Union (EU) defines food-contact materials very broadly—including the packaging material and any other material expected to be in contact with food under normal conditions. Regulation (EC) No 1935/2004 is the EU’s framework regulation and sets out general requirements for all food contact materials. The regulation requires that food-contact material suppliers provide statements in a “Declaration of Compliance”. This “Declaration of Compliance”confirms that migration limits have not been exceeded and that Good Manufacturing Practices have been applied in the supplier’s operations.
You could also try a fun experiment -- pour chocolate syrup all over the EOAT and then take apart the EOAT and see what syrup remains. Where there is syrup, there is opportunity for ingress and harborage, compromising food safety.
What questions should a manufacturer be asking their supplier to make sure the system is food safe?
When evaluating an EOAT solution for food processing and handling these questions will help choose a solution that delivers both the productivity and safety results needed. Below are a handful of questions we recommend asking your supplier:
- Can the solution meet the required rate of the application? Can it accommodate a variety of food items across spectrums of size, weight, shape and more?
- Is the system flexible enough to handle multiple scenarios?
- Is the solution successfully installed already elsewhere and proving value?
- Does the solution conform to the appropriate regulations and Good Manufacturing Practices?
- How can the supplier prove it to me?
- Is there potential risk for ingress or harborage of bacteria?
- How will the system be cleaned?
How is Soft Robotics addressing Food Safety and why do you feel your products offer the best solutions?
Soft Robotics uses advances in material science, material design and Good Manufacturing Practice to innovate the design and functionality of EOATs and to make them the safest for food contact. The gripper fingers, made from a food safe polymer, along with overall design and soft materials, make it possible for the device to envelope food items with a delicate touch, just as with a human hand. And when it comes to ensuring food safety, these systems are intrinsically sealed, protecting the device from ingress of food particles and eliminating the possibility of harborage of pathogens. Our adaptive grasping system can adapt without complex programming or sensors. They also reduce the downtime associated with changeovers, and future-proof operations against SKU-proliferation. You can read more about how Soft Robotics enables the food industry by clicking here.
Where do you see the biggest growth over the next several years in the food handling market?
Safety, quality and maintaining the integrity of food products will continue to be primary business drivers in the food handling market. Historically, the food packaging and handling industries have been the most difficult to automate, primarily due to the variability of the products involved in the operation. In addition, labor challenges continue to plague the food processing and handling industry. There simply aren’t enough people to do the wide variety of food handling tasks in the supply chain, and companies are turning to automation to fill this gap. We see a big area of growth to be in environments that have a high variability of product type and size. Having an adaptable system that doesn’t have to be re-programmed each time a new SKU is introduced will be essential.
The content & opinions in this article are the author’s and do not necessarily represent the views of RoboticsTomorrow
Comments (0)
This post does not have any comments. Be the first to leave a comment below.
Featured Product
