ARC Specialties designed and built a turnkey solution for 3D robotic plasma cutting with the help of essential offline programming tools. With the right partners by your side, no challenge is too steep.
Robotic Plasma Cutting in a 3D World
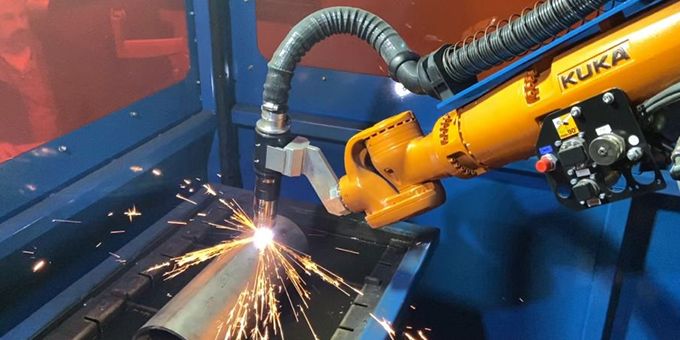
Case Study from | Robotmaster
Automating plasma cutting in three-dimensional space requires everyone involved to be at the top of their game. Programming a robot to maneuver the plasma torch at different angles and speeds, to create steady curves and smooth bevels, in three dimensions simultaneously is a tall order.
ARC Specialties, Inc., thrives on solving problems. Leveraging nearly 40 years of metal joining and cutting experience, the Houston, Texas-based automation integrator has built machines for the consumer, oil and gas, defense and research industries in over 30 countries. Rather than take a one-size-fits-all approach, they create innovative solutions that meet unique operational needs and support sustainable growth. ARC always matches the solution to the problem.
As more industries began to demand manufacturing processes beyond traditional 2D plate cutting, advanced cutting solutions manufacturer Hypertherm, Inc. approached ARC Specialties with the idea to design and build an automated solution for 3D robotic plasma cutting. The result was a collaborative effort.
Essential OLP
This particular puzzle had three parts: the cutting system, the robot and the software. Hypertherm’s advanced plasma cutting systems and KUKA Robotics’ powerful robot controller both use etherCAT communications, making them a good fit out of the gate. Both companies already had a relationship with ARC Specialties and were well aware of the integrator’s motion control expertise. KUKA’s recommendation for ARC to tackle the software side and integrate all the cell components only reinforced the alliance.
The idea was to create a turnkey fabrication system that could quickly and easily convert CAD drawings into three-dimensional plasma cut steel parts without labor-intensive programming. That’s where Hypertherm’s Robotmaster offline programming software became an integral piece to the puzzle.
“Robotmaster is essential,” says ARC Founder and President Dan Allford. “A 3D CAD drawing simply shows what the final part should look like. There is a huge amount of information needed to generate the robot path and parameters to create the part. The plasma torch must be offset to the outside of each cut line and angled in the right direction. Complex curves must be broken down into small spline segments to create a smooth final cut.”
“It could be thousands of lines of code,” says Allford. “No human could possibly do this. That’s all Robotmaster.”
Robotmaster software eliminates the need for point-by-point robot programming, saving time and labor. Offline programming (OLP) also increases uptime, as there’s no need to shut down production while programming the robot for a new job.
With all collaborators on board, ARC Specialties designed and built the FlexFab™ 3D Robotic Plasma Cutting Cell. The system made its debut at the FABTECH Expo in 2019. Showgoers were able to see CAD-to-path in real time and witness firsthand how easy it was with Robotmaster software. While onlookers watched in amazement, you could change the design of a part, push a button and the robot would cut it immediately.
“Anybody can hang a plasma on a robot. But then you still have to teach the robot the pattern,” says Allford. “We take a CAD drawing and import it into Robotmaster software. From there we convert that into robot code and make three-dimensional parts with no programming in between. FlexFab turns 3D drawings into 3D parts without any intermediate steps.”
Integrated Flexibility
The 3D world demands flexibility. So what puts the “flex” in FlexFab? The six-axis robot for one. Another is the software.
Compared to a standard CNC plasma table or a purpose-built machine, this flexible robotic cell is not only proficient at creating three-dimensional parts and complex shapes, you can still use it to cut two-dimensional parts. This is particularly advantageous for low-volume, high-mix applications where fabricators need the flexibility of frequent changeovers and easy programming with Robotmaster software.
ARC’s customers have included fabricators of pipelines for gas and oil and general industrial use, and manufacturers of pressure vessels and filters. But any fabricator cutting plate, pipe, I‑beam, channel or angle can benefit from the FlexFab system.
No matter the application, Robotmaster’s flexibility and ease of use also make the integration process easier.
“Robotmaster allows us to take on more challenging problems,” says Kevin Sevcik, control systems programmer at ARC. “It’s faster than other approaches we’ve taken with cells like this in the past. Some geometries are more complicated shapes that wouldn’t be practical to do from a type-in-a-bunch-of-dimensions standpoint. You really need offline programming software. Robotmaster is the easiest to work with.”
Robust Path Optimization
ARC’s Sevcik was responsible for bringing precision control to the FlexFab system. The cell’s ability to – on the fly – optimize cutting parameters every few millimeters demonstrates ARC’s motion control prowess. Robotmaster’s simulation and path optimization tools help even highly skilled, experienced programmers like Sevcik visualize and optimize error-free robot trajectories for both simple and complex applications.
“Sometimes there are motions you need to do with the robot where you’ll run into a singularity or you’ll run into a limit on one of the axes. Robotmaster’s path optimization makes seeing those limits and working your way around them a lot easier,” says Sevcik.
Robotmaster’s preprocessing tools are designed from the robot programmer’s viewpoint. On the screen before them, users see potential errors before they occur. Angle the torch in this direction, the zone turns red. Try it the other way, it turns green. You’re good to go. Path optimization is visualized.
Future-Proof Partnership
Looking forward, ARC Specialties will be working closely with the Robotmaster team to fine-tune the robot path generation process for 3D plasma cutting. The flexibility of the Robotmaster platform makes it malleable to integrators’ unique needs.
ARC has recently integrated FANUC robots into the FlexFab concept and plans to integrate the system with ABB robots as well. This is easy with Robotmaster, as the single software solution works with any of the major robot brands.
“When we have a problem, we need to know that we can call on somebody that is knowledgeable about the process,” says John Martin, ARC’s vice president of operations. “That’s why these types of relationships with Robotmaster and Hypertherm are so important.”
With the right partners by your side, you can face any challenge.
The content & opinions in this article are the author’s and do not necessarily represent the views of RoboticsTomorrow
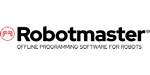
Robotmaster
Robotmaster, a Hypertherm Associates brand, is an offline, is an offline robot programming software that helps manufacturers maximize their robot's productivity with easy and efficient robot programming for a variety of applications such as cutting, trimming, milling, welding, spraying, polishing, sanding, grinding, deburring, and more. Robotmaster uses integrated CAD/CAM functionality to make robotic programming easy and intuitive for everyone, even first-time users.
Other Articles
Have You Looked at Automating Fabrication Tasks in the Past? Why Didn’t You?
Trane® Saves Over 80 Hours of Robot Programming Time
3 Benefits of Working With a Robotic Integrator
More about Robotmaster
Comments (0)
This post does not have any comments. Be the first to leave a comment below.
Featured Product
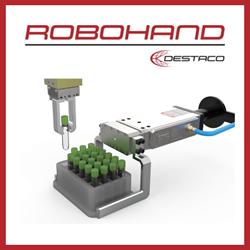