Food traceability is not just a matter of compliance, it’s also essential for maintaining customer trust and brand reputation.
Building Customers’ Trust With Robots - Advanced 3D Vision Systems Improve Food Traceability
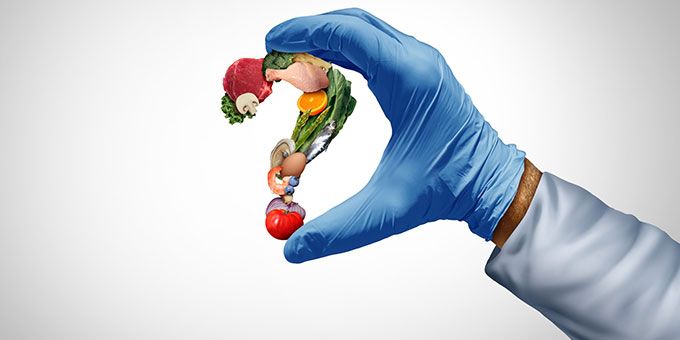
Ryan Guthrie,Vice-president | TM Robotics
Among the many worries currently surrounding the rapid evolution of AI is a potential lack of transparency and accountability. A report by the AI Now Institute, titled The State of AI 2019: Divergent Trends in AI, discusses how many AI systems are opaque and difficult to understand, which can make it challenging to hold them accountable for their decisions.
However, AI could help improve transparency and accountability for food manufacturers — particularly against one of the food industry’s biggest challenges, maintaining traceability. Manufacturers need to know where their products are coming from, where they are going, and who handled them in between. Being able to track a product from its origin through to the end consumer is critical, especially in the event of a recall or outbreak. Earlier this year, the US Food and Drug Administration (FDA) linked a Salmonella Infantis outbreak back to a specific flour manufacturer.
Automated traceability can help, here. For example, sensors and Internet of Things (IoT) devices can monitor environmental conditions such as temperature, humidity and light level. Or, barcoding and radio-frequency identification (RFID) allow for the easy tracking and identification of products as they move through the supply chain, providing real-time information on their location and status.
However, automated traceability has aways been a particular challenge in the food industry due to the variability of products. An obvious example is that no two bananas are exactly the same, and can vary significantly in shape. Any other given foodstuff can have its own unique set of ingredients, production processes and packaging requirements. An automated traceability system needs to be flexible enough to accommodate these variations and capture relevant data accurately.
The food industry also deals with complex supply chains and multiple stakeholders such as farmers, suppliers, distributors and retailers. The industry is also heavily-regulated, with strict rules and guidelines that manufacturers must comply with to ensure food safety and quality.
Previously, automated traceability systems that could deal with these complex factors were expensive to implement and maintain, requiring significant investments in hardware, software and training. The automated systems themselves were complex, requiring specialised knowledge and expertise to design, implement and operate effectively. They were also difficult to integrate with existing manufacturing processes and IT systems, requiring careful planning and coordination. So, what’s changed since then? The answers include robotics, AI and machine learning.
The TSVision3D system from Shibaura Machine is designed for industrial robots, and can recognise objects without the need for complex CAD data.
Affordable technology
Advances in vision systems, processing power and machine learning algorithms mean that manufacturers can now identify and sort different cuts of meat, fruits, and vegetables.
While these technologies are nothing new — the meat packing industry has been using X-rays to scan carcasses for robotic trimming for well over a decade — they were previously only accessible to higher-echelon manufactures. Automated traceability requires the integration of various technologies such as sensors, radio-frequency identification (RFID) tags, barcodes and data analytics tools. These technologies have traditionally required technical expertise and were expensive.
But this is changing. The adoption of automation technologies is increasing among small-medium-sized manufacturers due to improved accessibility and affordability. Additionally, the cost of IoT sensors, which are crucial for enabling automation, is decreasing rapidly. In fact, according to a report by IoT Analytics, the average cost of IoT sensors has dropped by 50 per cent over the past decade, making them more accessible to smaller businesses.
Storing large amounts of data used to be expensive, and difficult when dealing with large volumes of data from multiple sources. Costs have since lowered with the proliferation of cloud-based software and services, businesses can now access automation solutions on a pay-as-you-go basis, without the need for large upfront investments.
With the latest advancements in technology, it is now easier for manufacturers to access these technologies, reducing the need for manual labor and ensuring that every product is sorted correctly. But, how do robotics help in the traceability of food products?
Put simply, robots are designed to move products from one location to another safely and repetitively.
Adding scanners and RFID tags on each of the individual crates will help identify and trace products from one location to another, which is essential for ensuring the safety of the food supply chain. This way, manufacturers can scan the RFID tag and know that a particular container belongs to a specific pallet and, as the pallet leaves the factory, they could scan that the pallet was taken away by a certain delivery truck. This information helps manufacturers trace products and ensure that they are delivered to the right location at the right time.
TM Robotics offers a range of services and offerings to help manufacturers integrate robotics into their manufacturing processes. Its Shibaura Machine robots are designed to be flexible and can be customised to fit a range of applications. With its robots, manufacturers can improve the accuracy and consistency of their operations while reducing labour costs.
Improved sorting accuracy
Robot-assisted quality-sorting is one of the most effective ways to improve food traceability. The process uses robots to sort food items based on specific quality standards, and involves using advanced technologies such as AI and machine learning to ensure that the sorting is accurate and efficient.
The robots are programmed to recognise various shapes, sizes, colours, and defects in the food items and sort them accordingly. Machine learning algorithms enable the robots to continuously improve their sorting accuracy by learning from past data. This process ensures consistent quality control, reduces waste, and increases efficiency in the food manufacturing industry.
Advanced 3D vision systems, including Shibaura Machine’s TSVision3D, can read barcodes, check for defects such as in engine parts or wood quality, inspect packaging and inspect the end product.
The latest addition to vision systems is the TSVision3D system from Shibaura Machine, which is designed for industrial robots. This system is capable of recognising objects without the need for complex CAD data. The TSVision3D system uses two high-speed stereo cameras to capture real-time 3D images continuously. It can detect any object that appears in its field of vision, even non-uniform products such as bananas.
To ensure that a cheese manufacturer's robot-assisted quality sorting system was accurately picking up and placing the cheese in the correct place, Elliptical Design, a design and manufacturing company, turned to TM Robotics. However, the cheese's softness and unusual non-round shape created a margin of error. TM Robotics developed an ultrasonic cutting system specifically for this task.
TM Robotics' engineers utilised their collaboration with Shibaura Machine to identify the appropriate algorithm within the vision program that enabled the robot to accurately select the cheese. The outcome was an automated quality-sorting system that not only improved efficiency but also reduced waste.
As the food industry grows, it's essential to keep up with the latest technological advancements. Robotics and AI help manufacturers meet the demand for transparency in the food supply chain and ensure the safety and quality of our food supply.
The content & opinions in this article are the author’s and do not necessarily represent the views of RoboticsTomorrow
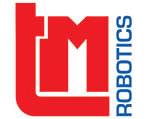
TM Robotics (Americas) Inc
TM Robotics, in partnership with Shibaura Machine, formerly known as Toshiba Machine until 1st April 2020, offers a comprehensive range of industrial robots ideally suited for high-precision assembly, machine loading/unloading and material-handling applications that can be dust proof, clean room, or IP65/67. The company's extensive product line starts with a Cartesian solution available in thousands of combinations from single actuators to four-axis solutions; six-axis solutions that can include precise vision-control; and a complete range of SCARAs from low cost to the industry-leading SCARA with 1200-mm reach that can carry up to 20 kgs. TM Robotics sells and services robots throughout Europe, the Middle East, India, Russia, and Africa, as well as North, Central, and South America, from headquarters in Hertfordshire, England and Elk Grove Village, IL, USA. For more information, visit www.tmrobotics.com or follow us on Twitter, LinkedIn and YouTube.
Other Articles
Giving lens cleaning cloths a robotic hand - Robotic automation for textile processing
Investing in the UK’s injection moulding sector - The case for all-electric machines and robotic integration
Robotic solutions for pharmaceutical packaging - Automated system addresses key limitations of manual processes
More about TM Robotics (Americas) Inc
Comments (0)
This post does not have any comments. Be the first to leave a comment below.
Featured Product
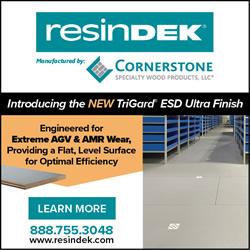