Automotive manufacturer SPAL needed to upgrade its production line to meet changing market demands — including faster cycle times and reduced energy consumption.
Breaking the mould - Shibaura Machine injection moulding machines transform SPAL Automotive’s production
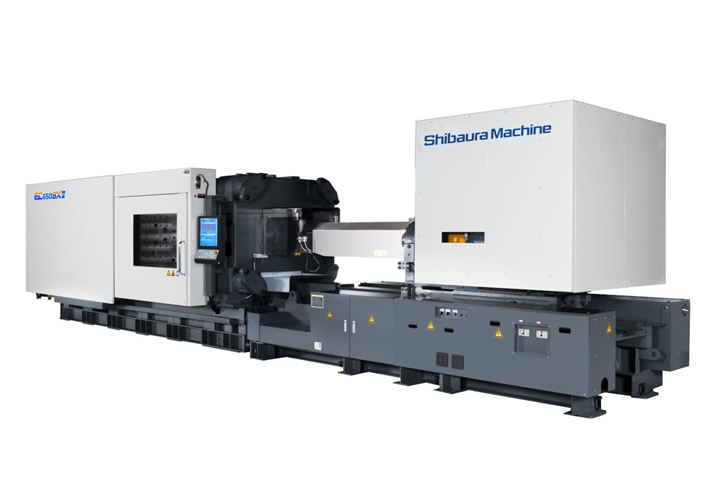
Case Study from | TM Robotics
Automotive manufacturer SPAL needed to upgrade its production line to meet changing market demands — including faster cycle times and reduced energy consumption. This meant upgrading from hydraulic to electric injection moulding machines, which presented several challenges. SPAL turned to EPF, the distributor of Shibaura Machine injection moulding equipment in Italy, for a solution. The results? Significant gains in productivity, efficiency and energy savings with the new, all-electric machines.
Founded in 1959, SPAL Automotive has grown from being a manufacturer of plastic components to a pivotal player in the automotive sector, producing axial and centrifugal electric fans for various vehicles. However, the company realised that it needed to adapt its production processes to evolving market demands.
In particular, SPAL sought to evolve — and also expand — its production line in Correggio, Italy, to achieve faster cycle times, reduce energy consumption and streamline logistics. A crucial step towards this would be upgrading its hydraulic injection moulding systems to all-electric. This would invite several challenges, including the potential of significant capital investment retrofitting complexities and retraining of personnel.
The shift from hydraulic to all-electric presses would mean not only updating production processes, but also revamping infrastructure to seamlessly accommodate the new technology. To support with these challenges, SPAL turned to its longstanding partner EPF, a partner for Shibaura Machine injection moulding equipment.
“SPAL decided to focus firmly on electric presses, which was an ideal solution,” explains Moreno Carvani, managing director, EPF plastic. “The benefits include very low energy consumption, high yields in the moulding process, and high reliability.”
Making the leap
Transitioning to fully electric presses presents significant challenges for automotive manufacturers. Firstly, the initial investment costs can be substantial, encompassing the purchase and installation of more expensive electric presses along with necessary upgrades to the facility's electrical infrastructure. Moreover, specialised training and expertise are essential for operating and maintaining these presses, requiring investment in staff development or recruitment.
Manufacturers must also ensure that the performance and efficiency of electric presses meet production requirements, which may involve testing and optimisation. Integrating electric presses into existing manufacturing systems poses complexities, including compatibility issues and software adjustments. Additionally, sourcing components and adhering to regulatory standards present further hurdles, while the transition period itself can disrupt operations.
However, despite these challenges, transitioning to electric presses offers long-term benefits, such as reduced operating costs and improved sustainability. Overcoming these obstacles demands strategic planning, collaboration with suppliers, and diligent implementation to realise the advantages of electric press technology in automotive manufacturing.
“EPF was able to supply Shibaura Machine — formerly Toshiba Machine — injection moulding machines with a tonnage range of 50 to 1,800 tones, which refers to the range of force or pressure these presses can exert during the moulding process,” added Carvani. With this range, SPAL can perform a variety of moulding tasks, from smaller components requiring less force to larger parts needing higher tonnage.”
Performance tests
To overcome these hurdles, SPAL turned to its strategic partnership with EPF, exclusive distributor and service partner of Shibaura Machine. The collaboration began when SPAL decided to focus on full-electric injection moulding machines. Shibaura Machine, already had the capabilities to supply injection moulding machines of a high tonnage range.
Performance tests conducted by Shibaura Machine ensure the energy efficiency of all-electric injection moulding machines. For example, the Shibaura Machine EC650SX-61B IMM, boasting a clamping force of 650 tons, showcased a notable 51 percent reduction in energy consumption compared to hydraulic servo alternatives. Similarly, the EC1800SX-155B model demonstrated superior cycle time and an impressive 30 percent overall energy efficiency gain compared to rival machines.
The machines offer faster injection speeds and improved cycle times, contributing to enhanced productivity and cost-effectiveness. Furthermore, their user-friendly interface and integration with the Internet of Things (IoT) simplify operations and support preventive maintenance strategies, ensuring optimal performance and longevity.
These performance tests reaffirmed the value proposition of Shibaura Machine's injection moulding machines, providing SPAL with confidence in their ability to deliver both operational excellence and energy efficiency.
SPAL’s collaboration with EPF facilitated an expansion of its production department, equipped with 21 fully electric injection moulding machines ranging from 50 to 1800 tons, with a capability to reach 2500 tons. This expansion enabled SPAL to meet market demands effectively and cater to a broader range of products.
Additionally, the inclusion of Digital Direct Screw Transfer (DST) Control enhanced production flexibility by enabling precise calibration of clamping force, optimising processes, and ensuring consistent product quality.
Moreover, the machines boasted faster injection speeds, resulting in reduced cycle times, thereby increasing overall productivity and throughput for SPAL's manufacturing operations. The user-friendly interface simplified operation, enhancing ease of use for SPAL's production personnel and facilitating seamless integration into existing workflows to minimise downtime and maximise efficiency.
Furthermore, the integration with the Internet of Things (IoT) allowed for remote monitoring and diagnostics, empowering SPAL to proactively identify and address potential issues, thereby reducing the risk of unplanned downtime and ensuring continuous production.
Enhancing efficiency
The adoption of electric presses not only enhanced production capacity but also streamlined logistics within SPAL's production department. Efficient material handling, improved workflow management, and reduced downtime contributed to overall productivity gains.
"Embracing all-electric injection moulding machines brings more than just efficiency gains, it opens the door to more diverse manufacturing,” said Nigel Smith, CEO at TM Robotics, distribution partner of Shibaura Machine. “By providing flexible production capabilities, reduced energy consumption and enhanced performance, Shibaura Machine's machines empower manufacturers to explore new markets, and cater to varied product demands.”
With Shibaura Machine's injection moulding machines at the core of its production processes, SPAL achieved significant gains in productivity, efficiency and energy savings. By addressing challenges such as technology adaptation, production capacity enhancement, efficiency improvement and quality assurance, the collaboration enabled SPAL to position itself as a leader in the industry.
To learn more about how Shibaura Machine's all-electric injection moulding machines support sustainable manufacturing, visit TM Robotics’ website.
The content & opinions in this article are the author’s and do not necessarily represent the views of RoboticsTomorrow
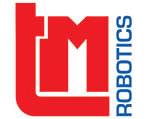
TM Robotics (Americas) Inc
TM Robotics, in partnership with Shibaura Machine, formerly known as Toshiba Machine until 1st April 2020, offers a comprehensive range of industrial robots ideally suited for high-precision assembly, machine loading/unloading and material-handling applications that can be dust proof, clean room, or IP65/67. The company's extensive product line starts with a Cartesian solution available in thousands of combinations from single actuators to four-axis solutions; six-axis solutions that can include precise vision-control; and a complete range of SCARAs from low cost to the industry-leading SCARA with 1200-mm reach that can carry up to 20 kgs. TM Robotics sells and services robots throughout Europe, the Middle East, India, Russia, and Africa, as well as North, Central, and South America, from headquarters in Hertfordshire, England and Elk Grove Village, IL, USA. For more information, visit www.tmrobotics.com or follow us on Twitter, LinkedIn and YouTube.
Other Articles
Giving lens cleaning cloths a robotic hand - Robotic automation for textile processing
Investing in the UK’s injection moulding sector - The case for all-electric machines and robotic integration
Robotic solutions for pharmaceutical packaging - Automated system addresses key limitations of manual processes
More about TM Robotics (Americas) Inc
Comments (0)
This post does not have any comments. Be the first to leave a comment below.
Featured Product
