In his search for a suitable camera, he came across IDS NXT - a complete system for the use of intelligent image processing. It fulfilled all requirements and, thanks to artificial intelligence, much more besides pure gesture recognition.
Robot plays "Rock, Paper, Scissors" - Part 1/3
Case Study from | IDS Imaging
Gesture recognition with intelligent camera
Sebastian Trella is passionate about technology and robotics. In his own blog, he is always taking on new tasks. But he has hardly ever worked with image processing. However, a colleague's LEGO® MINDSTORMS® robot, which uses several different sensors to detect the gestures of a hand, gave him an idea: "The robot should be able to "see”." Until now, the gesture had to be made at a specific point in front of the robot in order to be reliably recognized. Several sensors were needed for this, which made the system inflexible and dampened the joy of playing. Can image processing solve this task more "elegantly"?
From the idea to implementation
In his search for a suitable camera, he came across IDS NXT - a complete system for the use of intelligent image processing. It fulfilled all requirements and, thanks to artificial intelligence, much more besides pure gesture recognition. Trella's interest was piqued. This is because the evaluation of the images and the communication of the results took place directly on or through the camera - without an additional PC. The IDS NXT Experience Kit also came with all the components to get started with the application right away - no prior AI knowledge required.
Trella took the idea further and began to develop a robot that would play the game "Rock, Paper, Scissors" in the future - with a process similar to the classical sense: The (human) player is asked to perform one of the familiar gestures (scissors, rock, paper) in front of the camera. The virtual opponent has already randomly determined his gesture at this point. The move is evaluated in real time and the winner is displayed.
The first step: Gesture recognition by means of image processing
But until then, some intermediate steps were necessary. Trella began implementing gesture recognition using image processing - new territory for the robotics fan. However, with the help of IDS lighthouse - a cloud-based AI vision studio - this was easier to realize than expected. Here, ideas evolve into complete applications. For this purpose, neural networks are trained by application images with the necessary product knowledge, such as in this case the individual gestures from different perspectives, and packaged into a suitable application workflow.
"The training process was super easy and I just used IDS Lighthouse's step-by-step wizard after taking several hundred pictures of my hands using rock, scissor, or paper gestures from different angles against different backgrounds. The first trained AI was able to reliably recognize the gestures directly," explains Sebastian Trella. This works for both left- and right-handed users with a recognition rate of about 95%. Probabilities are returned for the labels "Rock", "Paper", "Scissor" or "Nothing". A satisfactory result. But what happens now with the data obtained?
Further processing
The further processing of the recognized gestures could be carried out by means of a specially created vision app. For this, the captured image of the respective gesture - after evaluation by the AI - must be forwarded to the app. The latter "knows" the rules of the game and can thus decide which gesture beats another. It then determines the winner. In the first stage of development, the app will also simulate the opponent. All this is currently in the making and will be implemented in the next step to the "Rock, Paper, Scissors"-playing robot.
From play to everyday use
Initially, the project is more of a gimmick. But what could come out of it? A slot machine? Or maybe even an AI based sign language translator?
To be continued... Read Part 2/3 here.
The content & opinions in this article are the author’s and do not necessarily represent the views of RoboticsTomorrow
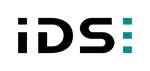
IDS Imaging Development Systems Inc.
World-class image processing and industrial cameras "Made in Germany". Machine vision systems from IDS are powerful and easy to use. IDS is a leading provider of area scan cameras with USB and GigE interfaces, 3D industrial cameras and industrial cameras with artificial intelligence. Industrial monitoring cameras with streaming and event recording complete the portfolio. One of IDS's key strengths is customized solutions. An experienced project team of hardware and software developers makes almost anything technically possible to meet individual specifications - from custom design and PCB electronics to specific connector configurations. Whether in an industrial or non-industrial setting: IDS cameras and sensors assist companies worldwide in optimizing processes, ensuring quality, driving research, conserving raw materials, and serving people. They provide reliability, efficiency and flexibility for your application.
Other Articles
2D cameras for positioning and inspecting ultra-fine wires in semiconductor production
Picking the right chart - (Semi-)Autonomous surface and underwater mapping for rivers and lakes
Pallet by pallet - Intelligent robotic vision system destacks up to 800 objects per hour
More about IDS Imaging Development Systems Inc.
Comments (0)
This post does not have any comments. Be the first to leave a comment below.
Featured Product
