Proximity Probe with Rear and Side View Target Protection
Condition monitoring specialists SENSONICS have added a new option to their established range of proximity probes which virtually eliminates the detrimental effects on measurements caused by both side and rear targets. The PRSVBeam proximity probe has an innovative tip design which overcomes the problems associated with traditional probe designs, such as poor accuracy, system non-linearities and extended set-up time.
Condition monitoring specialists SENSONICS have added a new option to their established range of proximity probes which virtually eliminates the detrimental effects on measurements caused by both side and rear targets. The PRSVBeam proximity probe has an innovative tip design which overcomes the problems associated with traditional probe designs, such as poor accuracy, system non-linearities and extended set-up time.
In certain monitoring applications, for example where the probe tip is installed close to the machine casing or in a counter bore where the side view can distort readings, the effectiveness of proximity probes can be compromised. Also, in many applications, such as those requiring accurate measurement of thrust bearing wear or shaft position, probe access to the target is restricted. While the probe face can be fixed opposite the main target (end of a shaft or collar), it is likely additional side and rear targets will also impact the measurement and this situation worsens as the designated target moves away from the probe face, hence system non-linearities and extended set-up time.
Proximity probes operate on the principle of eddy currents set up in the surface of a conductive target material perpendicular to the axis of the probe tip. Proximity to the target affects the eddy current magnitude and therefore field strength which is detected through the probe driver as a linearised distance from the probe face. Traditional probe tip designs are exposed to not only the target, but also side and rear views.
The new PRSVBeam offers a fully protected rear and side view through complete metallic encapsulation of the probe sensor assembly and its unique tip design provides a beam effect towards the target resulting in excellent linearity, even if fitted with the tip flush to the machine case or mounting assembly. At the extreme end of the probe range the effect is a 0.5% measurement error which reduces to less than 0.2% in the middle of the probe measurement range. Another benefit of this tip design is its ability to withstand pressures up to 300bar and to provide sensor tip protection when utilised in heavy particle based fluids.
The introduction of this new probe option provides a measurement range spanning 0.2mm - 1.7mm and linear within 1% in a 10mm diameter tip probe, providing micrometre resolution for both critical fluid film bearing vibration and shaft position applications. Another advantage of the probe is it's suitability for use in 'blind-hole' measurement situations where certain applications restrict the ability to calibrate the in-situ probe system and rely on the bench calibrated performance to set the target gap and sensitivity. Thanks to the performance of the PRSVBeam when subjected to multiple targets the measurement accuracy can be guaranteed and therefore can be recommended for these types of application.
The new PRSVBeam can be supplied with a choice of fixed cable lengths of 2m, 5m, 7m, 9m, 14m and with a separate driver module in accordance with the API670 standard.
Featured Product
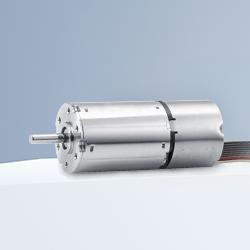