A Better Alternative to Additive Manufacturing
Offering Next-Generation Injection Molding Processes, with lead times that rival additive manufacturing.
CLINTON TOWNSHIP, Mich., Nov. 24, 2014 -- Xcentric Mold & Engineering's innovative injection molding process offers developers a competitive advantage in part creation.
Fast time to market is crucial in product development. It's the difference between innovators and imitators. So it's only natural for designers and engineers to want to partner with a manufacturer that gives them a competitive advantage, both in terms of technology, experience and the flexibility to produce parts efficiently and of high quality.
That's what Clinton Township, Michigan-based Xcentric Mold & Engineering excels in, but not in the way you might think. While most manufacturers have invested heavily in additive processes for rapid prototyping purposes, Xcentric has put its resources into revolutionizing injection molding and the way parts are built with the process - a move that has positioned the company five years ahead of the curve in manufacturing proficiency.
"Our goal was to create a system that brings injection molded parts to the customer in days - not weeks," starts Brendan Weaver, President, Xcentric Mold & Engineering. "With our process, we can create an injection mold faster than it can be 3D printed, a savings which is passed on to the customer in costs and time."
The process includes the creation of a custom-built injection mold and the industry's first lifetime warranty. It's a computerized injection process that assures stress-free molding and the most consistent shot-to-shot repeatability in the industry today. Customized and automated, from top to bottom utilizing a fast quoting system also helps with its accelerated part creation.
With innovations such as these, Xcentric boasts turnaround times as short as one day, depending on part complexity. But unlike additive processes, this next-generation injection molding process is also capable of creating highly complex parts with incredible accuracy, which may take anywhere from 1 to 15 days to ship.
"Rapid prototyping is nearing its limitations - but we've just reached the tip of the iceberg with our process. We will continue to make advancements moving forward so our customers can further benefit from the speed and quality of our process so that they can move their products into the market faster than ever before."
For more information on Xcentric Mold & Engineering, contact the company at 586-598-4636 or visit Xcentric online at www.xcentricmold.com.
About Xcentric Mold & Engineering
Xcentric specializes in low-volume custom injection molding and CNC machined parts. Their approach has become a vital process to many organizations, small businesses and inventors alike. They provide quick-turn manufacturing solutions for product development professionals or anyone looking to bring a new idea to market utilizing plastic or metal materials.
Featured Product
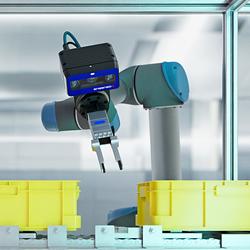
3D Vision: Ensenso B now also available as a mono version!
This compact 3D camera series combines a very short working distance, a large field of view and a high depth of field - perfect for bin picking applications. With its ability to capture multiple objects over a large area, it can help robots empty containers more efficiently. Now available from IDS Imaging Development Systems. In the color version of the Ensenso B, the stereo system is equipped with two RGB image sensors. This saves additional sensors and reduces installation space and hardware costs. Now, you can also choose your model to be equipped with two 5 MP mono sensors, achieving impressively high spatial precision. With enhanced sharpness and accuracy, you can tackle applications where absolute precision is essential. The great strength of the Ensenso B lies in the very precise detection of objects at close range. It offers a wide field of view and an impressively high depth of field. This means that the area in which an object is in focus is unusually large. At a distance of 30 centimetres between the camera and the object, the Z-accuracy is approx. 0.1 millimetres. The maximum working distance is 2 meters. This 3D camera series complies with protection class IP65/67 and is ideal for use in industrial environments.