‘Squishy' Motors and Wheels Give Soft Robots a New Ride
Rutgers engineers, in a breakthrough, create a soft motor that could power versatile soft robots
A small, squishy vehicle equipped with soft wheels rolls over rough terrain and runs under water.
Future versions of the versatile vehicle might be suitable for search and rescue missions after disasters, deep space and planet exploration, and manipulating objects during magnetic resonance imaging (MRI), according to its creators at Rutgers University.
Their most important innovation is a soft motor that provides torque without bending or extending its housing, said Aaron D. Mazzeo, assistant professor in the Department of Mechanical and Aerospace Engineering, who coauthored the study.
The Rutgers engineers breakthrough study was published online this week in the journal Advanced Materials. The lead author is Xiangyu Gong, who earned a masters degree in mechanical engineering at Rutgers in 2015 and is now a doctoral student at Rensselaer Polytechnic Institute in Troy, New York. Aside from Gong and Mazzeo, other authors include current or former Rutgers students Ke Yang, Jingjin Xie, Yanjun Wang, Parth Kulkarni and Alex Hobbs.
"The introduction of a wheel and axle assembly in soft robotics should enable vast improvement in the manipulation and mobility of devices," Mazzeo said. "We would very much like to continue developing soft motors for future applications, and develop the science to understand the requirements that improve their performance."
According to Mazzeo, innovations by Gong and the other Rutgers researchers include:
• Motor rotation without bending. "Its actually remarkably simple, but providing torque without bending is something we believe will be advantageous for soft robots going forward," Mazzeo said.
• A unique wheel and axle configuration that is not found in nature. The soft wheels may allow for passive suspensions in wheeled vehicles.
• Wheels that use peristalsis, the process people use to push food to the stomach through the esophagus.
• A consolidated wheel and motor with an integrated "transmission."
• Soft, metal-free motors suitable for harsh environments with electromagnetic fields.
• The ability to handle impacts. The vehicle survived a fall eight times its height.
• The ability to brake motors and hold them in a fixed position without the need for extra power.
To create the vehicle, the Rutgers engineers used silicone rubber that is nearly 1 million times softer than aluminum, Mazzeo said. Its softness is somewhere between a silicone spatula and a relaxed human calf muscle.
The motors were made using 3-D printed molds and soft lithography, and a provisional patent has been filed with the U.S. government.
"If you build a robot or vehicle with hard components, you have to have many sophisticated joints so the whole body can handle complex or rocky terrain," Gong said. "For us, the whole design is very simple, but it works very well because the whole body is soft and can negotiate complex terrain."
Future possibilities include amphibious vehicles that could traverse rugged lakebeds; search and rescue missions in extreme environments and varied terrains, such as irregular tunnels; shock-absorbing vehicles that could be used as landers equipped with parachutes; and elbow-like systems with limbs on either side.
"We think these robots also would be useful for working around children or animals, and you could envision them being helpful in hospitals," Mazzeo said. "There are opportunities also for toys and for creating educational science or engineering kits."
Funding for the project was provided by the Rutgers School of Engineering, the Department of Mechanical and Aerospace Engineering, the Rutgers Research Counciland an A. Walter Tyson Assistant Professorship Award.
Featured Product
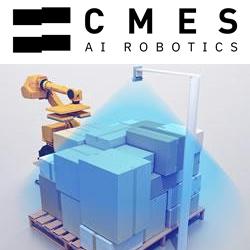
CMES - AI-Powered 3D Robot Vision
Powered by AI, CMES Robotics enables 3D vision for factory robots. CMES AI vision software enables robots to recognize unstructured, flexible, or deformed objects, pick them up, and loading and unloading. CMES Vision software has been deployed worldwide for random palletization and depalletization along with void filling applications. CMES Robotics automates your warehouse, logistics, and supply chain. For more information, please visit: cmesrobotics.com or email info@cmesrobotics.com.