ROBOTS EMERGING AS AGRICULTURAL CO-WORKERS
The technology is mature and ready for the field, say experts
Advanced engineering could be the solution for the sustainable intensification of agriculture, as technology for producing service robots reaches maturity. Experts in robotics from University of Cambridge, University of Lincoln and Harper Adams University will be discussing the latest developments during Agri-Tech Easts ‘Pollinator event on 11 October 2016.
So what exactly is a robot? Dr Andre Rosendo, a Research Associate at the University of Cambridge, believes that there are two critical factors that separate a robot from a machine - the capacity to be autonomous or to act with some degree of decision, and presence of actuators, which allow a machine to alter its environments. This precludes computers and fridges from being called robots.
He explains: "We are using our knowledge of soft robotics to create deformable manipulators, or ‘hands, that can manipulate ‘fragile produce, such as broccoli, strawberry and mushrooms. Currently, we are working on Vege bot; a harvesting robot can handle and cut iceberg lettuces with the same handling care as human harvesters. In the future the robots will have the potential to help elderly people from their beds, to handle glasses as a bartender or to interact with children."
Dr Rosendo will be speaking at the Agri-Tech East event alongside Professor Tom Duckett, who leads the Lincoln Centre for Autonomous Systems at the University of Lincoln.
Professor Duckett says that agricultural robotics bring benefits of reduced labour costs, economic sustainability, less waste and better use of natural resources. The technology has the potential to be deployed at any time of day and impact positively on the productivity and life quality of agricultural workers.
The Lincoln team, part of the Universitys Lincoln Institute for Agri-food Technology, has been working on multiple projects in this area including 3D mapping techniques for improving the precision of agricultural sprayers and a new project in 3D imaging for broccoli harvesting, which is producing strong results and attracting interest from end users such as the Brassica Growers Association.
Prof. Duckett continues: "Already we can envisage agricultural robots that could perform multiple tasks, for example, inter-changeable tools would allow switching between tasks such as seeding, tillage, spraying and harvesting.
"You could also have robots for agriculture and food production that would perform other useful tasks at the same time such as surveillance, keeping a watchful eye on crops, livestock and expensive farm machinery, while carrying out their primary duties on the farm or in the factory."
A number of machinery companies are investing in the technology and a project in 3D imaging for robotic weeding is currently being carried out with a local company, Garford Farm Machinery, world leaders in automated weeding equipment.
Prof. Duckett believes that the underpinning technologies for robotic perception, learning and action are already reaching the required level of maturity to leave research laboratories. So what steps need to be taken to transition from lab to work on the farm or in the factory?
"The big challenge now is how to cross the so called ‘Valley of Death between the development of useful prototypes by researchers and the mass production of agricultural robots which are available to the farmer, " he says. "We need investors to come forward and believe in what we are doing. There is also a need to convince farmers that we can produce robust and effective machines that can really do the job."
Dr Rosendo agrees that it is important to cultivate a greater understanding between all parties: "It is often said that academics are only interested in publishing papers, but the research can provide competitive advantage for early adopters. We are interested in talking to companies that see a more strategic benefit in developing potentially disruptive technologies."
Despite all these exciting advances, Prof Duckett believes that full automation is "not necessarily desirable", and instead sees a future of environmentally friendly ‘robot helpers:
"Robot helpers will increase the productivity and life quality of agricultural workers and help to deliver the sustainable intensification of agriculture that will be needed to help feed a growing population while minimising the impact on the environment. Smart robots that run on battery power rather than fossil fuels could also be part of the solution for a cleaner, greener future."
Dr Belinda Clarke, Director of Agri-Tech East, says:
"We now have the capability to use robotics efficiently in agriculture; this is no longer a sci-fi concept, but one rooted in reality. The current status and latest technological developments will be discussed at the upcoming Pollinator meeting."
Professor Duckett, Dr Rosendo and Professor Simon Blackmore of Harper Adams University are scheduled to speak at NIAB Park Farm, Cambridgeshire for an Agri-Tech East ‘Pollinator event on 11 October 2016 (‘Robo-Cropping - The Potential for Precision Robotics in Agriculture).
About Agri-Tech East: www.agritech-east.co.uk
Agri-Tech East is a business-focused cluster organisation. The East of England is home to the business, technology and research powerhouses of Cambridge and Norwich as well as some highly innovative growers and producers who manage much of the UK's most productive and profitable agricultural land. By creating a global innovation hub, Agri-Tech East aims to improve the international competitiveness of plant and crop-based agriculture and catalyse economic growth.
About ‘Pollinator: http://bit.ly/29sDUBT
Agri-Tech East has monthly ‘Pollinator network meetings. The aim is to inspire and facilitate discussions between participants with new ideas and fresh thinking. People from all sectors and disciplines are welcome, including growers, researchers, technologists and entrepreneurs.
Featured Product
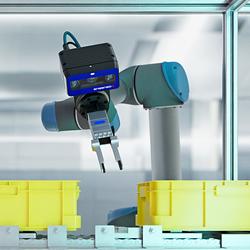
3D Vision: Ensenso B now also available as a mono version!
This compact 3D camera series combines a very short working distance, a large field of view and a high depth of field - perfect for bin picking applications. With its ability to capture multiple objects over a large area, it can help robots empty containers more efficiently. Now available from IDS Imaging Development Systems. In the color version of the Ensenso B, the stereo system is equipped with two RGB image sensors. This saves additional sensors and reduces installation space and hardware costs. Now, you can also choose your model to be equipped with two 5 MP mono sensors, achieving impressively high spatial precision. With enhanced sharpness and accuracy, you can tackle applications where absolute precision is essential. The great strength of the Ensenso B lies in the very precise detection of objects at close range. It offers a wide field of view and an impressively high depth of field. This means that the area in which an object is in focus is unusually large. At a distance of 30 centimetres between the camera and the object, the Z-accuracy is approx. 0.1 millimetres. The maximum working distance is 2 meters. This 3D camera series complies with protection class IP65/67 and is ideal for use in industrial environments.