PACK Expo - Shuttleworth to Showcase Innovative Collaborative Conveyor with Fenceless Technology at Pack Expo 2016
The collaborative conveyor with innovative fenceless technology features the FANUC LR Mate 200iD robot, and meets critical safety standards. (Shuttleworth Pack Expo Booth # S-3730)
Shuttleworth, powered by Pro Mach, is a premier manufacturer of material handling solutions, and the company will showcase its collaborative conveyor with the innovative fenceless technology featuring the FANUC LR Mate 200iD robot during Pack Expo 2016, November 6-9 at McCormick Place in Chicago, Illinois. (Shuttleworth Pack Expo Booth # S-3730)
"Generally, collaborative robots work with a human operator side-by-side, but the difference between fenceless technology and collaborative is the speed," stated Michael Liu, Engineering Manager for Shuttleworth. "Our work cell demonstrates the robot running at 100% speed in normal operating zone. If human intervention is required, the robot will reduce speed and go to zero speed to allow for any correction or inspection needed. No access buttons or reset are required."
Shuttleworths collaborative systems meet Safety Category 3 PLd and the requirements of ANSI/RIA/ISO/EN 10218-1 for safety performance.
For those interested in automating their material handling process and improving productivity and efficiency along the packaging line, stop by and visit Shuttleworth at Pack Expo, booth #S-3730. For more information on Shuttleworth, call (800) 444-7412 and visit http://www.Shuttleworth.com.
About Shuttleworth
Since 1962, Shuttleworth has served as a leading designer, consultant, and manufacturer of solutions to solve whatever material handling challenge you might face. When you need a conveyor system that will accumulate, flip, stack, rotate, push, divert, or index your products between manufacturing or packaging processes, we can design and build it. Year after year, we continue to revolutionize our industry with Slip-Torque® technology and conveyor system and equipment innovations that are as unique as your product line. Shuttleworth is headquartered in Huntington, IN and also operates a manufacturing facility near Gent, Belgium and maintains a sales and engineering office in Kuala Lumpur, Malaysia. For more information about Shuttleworth, visit http://www.Shuttleworth.com.
About Pro Mach
Pro Mach is a leading provider of integrated packaging and processing products and solutions for food, beverage, consumer goods, pharmaceutical, and other diverse companies. Through multiple brands, Pro Mach provides product packaging and processing equipment, PMMI certified trainers, installation, parts, and service in Bottling & Capping, Primary Packaging, Pharmaceutical Packaging, Flexible Packaging, Material Handling, Labeling & Coding, and End of Line, as well as Integrated Solutions for complete packaging lines.
Pro Mach has a diverse customer base, from Fortune 500 companies to smaller, privately held businesses worldwide, which depend on reliable, flexible, technologically advanced equipment and integrated solutions. Pro Mach is headquartered near Cincinnati, Ohio, with manufacturing facilities and offices throughout the United States, Canada, Mexico, Europe, United Arab Emirates, and China. For more information about Pro Mach, please visit http://www.ProMachInc.com.
Featured Product
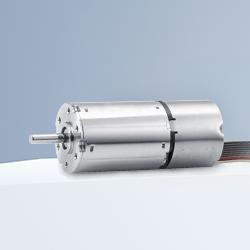
FAULHABER Drive Systems at the Robotics Summit & Expo in Boston from April 30 to May 1 in Hall C at Booth 534
Faulhaber will be presenting their drive systems for robotics and smart technology. Robots are versatile and can be found in many areas, for example, transporting goods, operating on patients or supporting the agriculture industry. With the help of robots, processes can be automated, the flow of materials optimized and employees relieved. Equipped with FAULHABER drive systems, these robots can take on tasks where the demands on function and applications are high.