ABB Pack Expo 2017 exhibit showcases leading edge product advancements that provide the flexibility to quickly adapt to evolving customer preferences
The Collaboration, Simplicity and Digitalization unique to ABB allow manufacturers to efficiently and safely handle multiple product and package variations
Chicago, Illinois: (September, 19, 2017) - ABB will feature a broad range of robotic and motion technologies for packaging and warehouse distribution applications at Pack Expo 2017, September 25-27 at the Las Vegas Convention Center (#C-5242).
The exhibit highlights the advanced level of collaboration, digitalization and simplification unique to ABB, which provides manufacturers the flexibility to efficiently adapt production and packaging as evolving consumer preferences require a shift from mass production to mass customization.
Collaboration comes in the form of YuMi®, the industrys first truly collaborative robot, and SafeMove2, the latest generation of ABBs safety certified robot monitoring software, providing a new level of human-robot interaction that enhances both productivity and workplace safety. Simplification is exhibited by the breadth of ABBs portfolio as a single-source automation supplier for food and beverage applications, and a robotic parcel singulation system that reduces the cycle time for a difficult task.
Digitalization ties it all together, with ABB Ability™ delivering timely and actionable information to drive better decisions that help manufacturers increase productivity, flexibility and efficiency along the manufacturing value chain.
"ABB has a comprehensive food and beverage portfolio, and we're excited to talk with customers about how ABB can help food and beverage producers optimize operations by cost-efficiently managing manufacturing complexity and flexibility to quickly and efficiently meet changing consumer demands," said Cliff Cole, the ABB leader of the Food & Beverage Program in the United States.
Further detail of the ABB Pack Expo 2017 exhibit:
• Food & Beverage Solutions Cell with FlexPicker and SCARA Robots: Highlights the power of integration and the breadth of ABBs portfolio as a single-source automation supplier for food and beverage applications. The demo features an IRB 360 FlexPicker® with PickMaster™ software and an IRB 910SC SCARA robot working together to collate tokens from a randomized infeed flow. An ABB N-Series servo motor and an E-180 servo drive equipped with an encoder track collate product on an outfeed conveyor for a continuous motion label application. The infeed and outfeed conveyors are driven by ABB washdown electric motors, washdown gearboxes and ACS380 drives. The entire cell is controlled with an ABB AC500 PLC with a CP600 HMI, and features a complete ABB safety system.
• Robotic Parcel Singulation System: Features an ABB IRB 1600 robot (1.45m reach/10kg payload) equipped with a 3D perception system to identify and pick a single object from a bin, tray or pile of identical, similar or varied products. The perception system delivers pick locations from a bin of randomly sized and weighted parts to the robot, which picks and places the parts onto a downstream sortation system. The system can work with any ABB robot, with the throughput performance determined by the payload and speed of the selected robot. This unique configuration enables ABB customers to experience industry leading speeds and is capable of working from a live feed chute.
• Flexible Robotic Palletizing: The ABB IRB 460 is the fastest palletizing robot in its class, specifically designed to meet the high throughput requirements of end-of-line applications. The cell features the new FlexGripper Vacuum with 100 lb payload capacity and two adjustable vacuum rails. Ten vacuum zones allow the picking of multiple case sizes and up to five cases at a time, with the ability to individually place the cases where complex pallet patterns are required. The gripper includes claws for pallet handling as well as separate vacuum cups for reliable slip sheet handling. The combination of a high speed palletizing robot, flexible end-of-arm tool and integrated palletizing software provides a simple and economical automated palletizing system. Mixed layer palletizing is also supported.
• YuMi Collaborative Robot: Packaging applications for YuMi are widespread, including kitting of multiple components into packages, component assembly and packing of fragile materials. YuMi can operate in very close collaboration with humans due to its inherently safe design and human-like dimensions and movements, and is very easy to program. At the booth YuMi is tending a single serving coffee machine, placing cups and coffee capsules into the machine, pressing the brew button and presenting fresh coffee to booth visitors. YuMi is utlizing integrated vision to select the chosen coffee flavor.
• IRB 1200 with SafeMove2: The IRB 1200 is the smallest ABB robot to feature SafeMove2, the latest generation of ABBs safety certified robot monitoring software. At the booth the small footprint, large work envelope IRB 1200 is utilizing a sanitary SoftRobotics gripper to present produce for inspection. SafeMove2 eliminates the need for full fencing and allows the robot to work collaboratively with human operators. The safety software is available on ABB 4- and 6-axis robot models from the IRB 1200, all the way up to the IRB 8700, ABBs largest robot. The IRB 1200 is now available in a Food Grade Lubrication model that includes Clean Room ISO Class 3 and IP 67 protection ratings, providing uncompromised safety and hygiene for food and beverage applications.
• ABB Ability: A wide range of optimization and automation solutions that bring increased quality and precision to even the most complex manufacturing processes. From software that streamlines production to predictive maintenance that lowers operating costs, ABB Ability enables manufacturers to know more, do more, do better, together. A key feature is the myABB Portal, a single online entry point where ABB customers can access information and services for their entire base of ABB equipment.
• ABB JOKAB SAFETY: A full array of machine safety products and systems for the food and beverage, packaging and material handling industries. The demo displays the new Sentry Safety Relays, the Orion Safety Light Curtain and the Hot Swap capabilities of the Pluto Safety PLC. Members of the Machine Safety Services team will be available to explain how JOKAB can help industrial organizations complete plant and machine safety assessments to insure that all equipment meets safety standards, while protecting personnel.
Further information for editors:
ABB (NYSE: ABB) is a pioneering technology leader in electrification products, robotics and motion, industrial automation and power grids, serving customers in utilities, industry and transport & infrastructure globally. Continuing a more than 125-year history of innovation, ABB today is writing the future of industrial digitalization and driving the Energy and Fourth Industrial Revolutions. ABB operates in more than 100 countries with about 132,000 employees. ABBs Americas business is headquartered in Cary, North Carolina. Since 2010, ABB has invested $11 billion in the United States, and the company continues to expand and localize its offerings for customers. ABB operates 60 manufacturing facilities and employs approximately 20,000 people across the U.S. www.abb.com
ABB Robotics is a pioneer in industrial and collaborative robots and advanced digital services. As one of the worlds leading robotics suppliers, we are active in 53 countries and over 100 locations and have shipped over 300,000 robot solutions in a diverse range of industries and applications. We help our customers to improve flexibility, efficiency, safety and reliability, while moving towards the connected and collaborative factory of the future. www.abb.com/robotics
Featured Product
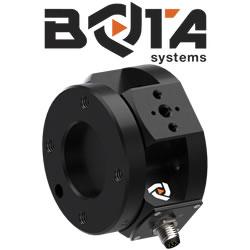
Bota Systems - The SensONE 6-axis force torque sensor for robots
Our Bota Systems force torque sensors, like the SensONE, are designed for collaborative and industrial robots. It enables human machine interaction, provides force, vision and inertia data and offers "plug and work" foll all platforms. The compact design is dustproof and water-resistant. The ISO 9409-1-50-4-M6 mounting flange makes integrating the SensONE sensor with robots extremely easy.
No adapter is needed, only fasteners! The SensONE sensor is a one of its kind product and the best solution for force feedback applications and collaborative robots at its price. The SensONE is available in two communication options and includes software integration with TwinCAT, ROS, LabVIEW and MATLAB®.