How to Communicate PLC to VFD
PLC (Programmable Logic Controller) and VFD (Variable Frequency Drive) play an important role in industrial production and technological development. They have been widely used in the field of industrial automation and mechanical automation. The control of the PLC and VFD is quite intelligent and automated, which brings great convenience to industrial production and life. The PLC and VFD will perform intelligent calculation, control and output according to the predetermined program. Today we will focus on how the PLC and the VFD communicate, and in what ways? First, let's take a look at their respective basic structures.
picture showing programmable logic controller wiring cable communication and socket connection
PLC (Programmable Logic Controller) and VFD (Variable Frequency Drive) play an important role in industrial production and technological development. They have been widely used in the field of industrial automation and mechanical automation. The control of the PLC and VFD is quite intelligent and automated, which brings great convenience to industrial production and life.
The PLC and VFD will perform intelligent calculation, control and output according to the predetermined program. Today we will focus on how the PLC and the VFD communicate, and in what ways? First, let's take a look at their respective basic structures.
1. Basic Structure of PLC
The memory of the PLC programmable controller can be divided into three types: system program memory, user program memory and working data memory.
PLC's basic structure including microprocessor, system program memory, user program memory, etc
Figure 2: Basic structure of PLC.
System Program Memory
The system program memory is used to store the system program written by the programmable controller manufacturer. It is solidified in the ROM (Read Only Memory), and cannot be directly modified by users. The quality of the system program determines the performance of the PLC to a large extent.
Its content mainly includes three parts. The first part is the system management program, which mainly controls the operation of the programmable controller and makes the entire programmable controller work step by step. The second part is the user instruction interpretation program. Through it, the programming language of the programmable controller is changed into machine language instructions, and these instructions are executed by the CPU. The third part is the standard program module and system call program.
User Program Memory
The application program compiled according to the control requirement is called the user program. The user program memory is used to store various user programs written by the user in the specified PLC programming language for specific control tasks. At present, the more advanced programmable controllers use flash memory that can be read and written at any time as user program memory. The flash memory does not need a backup battery, and the data will not be lost when the power is cut off.
Working Data Memory
The working data memory is used to store working data, that is, the ON/OFF status and numerical data used in the user program. There are component map registers and data tables in the work data area. Among them, the component map register is used to store the switch quantity, output status, and the ON/OFF status of internal devices such as timers, counters, and auxiliary relays. The data table is used to store various data during the execution of the user program, such as some variable parameter values, the digital quantity obtained by A/D conversion and the result of digital operation.
2. Basic Structure of VFD
VFD's basic structure including rectifier, filter, inverter, etc
Figure 3: Basic structure of VFD.
The VFD is a device that converts utility frequency power (50Hz or 60Hz) into AC power of various frequencies to achieve variable-speed operation of the motor.
The control circuit controls the main circuit, and the rectifier circuit converts AC power into DC power. The DC intermediate circuit smoothes and filters the output of the rectifier circuit, and the inverter circuit inverts the DC into AC. For vector control VFDs that require a large amount of calculations, sometimes a CPU for torque calculation and some corresponding circuits are needed.
3. Difference between PLC and VFD
Both PLC and VFD can complete some specific instructions to control the motor. PLC is a kind of program input execution hardware, and VFD is one of them. Therefore, the PLC covers a larger range than the VFD, and can be used to control more things, with a wider application field and more powerful performance. Of course, the PLC control accuracy is also greater.
The VFD cannot be programmed to change the frequency, voltage and other parameters of the power supply. Its output frequency can be set to a fixed value, or dynamically controlled by the PLC. PLC can be programmed, used to control electrical components or complete communication tasks.
The communication between the PLC and the VFD needs to follow the universal serial interface protocol (USS), and the method of access is determined according to the principle of master/slave communication of the serial bus.
A bus can connect a master station and up to 31 slave stations. The master station selects the slave station which needs to transmit data according to the address characters in the communication message. When the master station does not require it to communicate, the slave station itself cannot send data first, nor can it directly transmit information between each slave station.
4. Three General Connection Methods between PLC and VFD
picture shows how to wire the PLC and the VFD
Figure 4: PLC and VFD wiring diagram.
4.1 Analog Output Module of PLC
People can use PLC's analog output module to control the VFD. PLC outputs 0~5V voltage signal or 4~20mA current signal, which is used as the analog input signal of the VFD to control the output frequency of it.
The wiring of this control method is simple, but it is necessary to select a PLC output module that matches the input impedance of the VFD. The price of the PLC analog output module is relatively expensive. In addition, it is necessary to take voltage division measures to let the VFD adapt to the voltage signal range of the PLC. When connecting, attention has to be paid on separating the wiring to ensure that the noise on the side of the main circuit is not transmitted to the control circuit.
4.2 Switch Quantity Output of PLC
The switch quantity output of PLC can generally be directly connected with the switch quantity input of the VFD. This control method has simple wiring and strong anti-interference ability. The switch quantity output of PLC can control the VFD like its start/stop, forward/reverse rotation, jog, rotation speed, and addition and subtraction time. It could realize more complicated control requirements, but only regulate the speed in stages.
When the relay contacts are used for connection, there may be malfunctions due to poor contact. When a transistor is used for connection, it is necessary to consider factors such as the voltage and current capacity of the transistor itself to ensure the reliability of the system.
In addition, when designing the input signal circuit of the VFD, it should be noted that improper connection of the input signal circuit may sometimes cause the VFD to malfunction. For example, when the input signal circuit adopts an inductive load like a relay and the relay is switched on and off, the noise caused by the generated surge current may cause the VFD to malfunction, which should be avoided as much as possible.
a new universal VFD controlling industrial current and power
Figure 5: Micro drive.
4.3 Connection between PLC and RS-485 Communication Interface
Each type of PLC host has a built-in standard configuration of 2 communication interfaces, that is, an RS-232 and an RS-485 communication interface. The RS-232 interface is mainly used to upload and download programs or to communicate with the upper computer and touch screen. The RS-485 interface is mainly used to build a network using the RS-485 protocol to realize communication control.
All standard Siemens VFDs have an RS-485 serial interface (some also provide RS-232 interface), which uses two-wire connection and whose design standards are suitable for application objects in an industrial environment. A single RS-485 link can connect up to 30 VFDs. And according to the address of each VFD or the use of broadcast information, the VFD that needs to communicate can be found. A master controller (master station) is required in the link, and each VFD is a slave control object (slave station).
wiring diagram of motor's stop, forward and reverse rotation controlled by PLC and VFD
Figure 6: Motor forward and reverse wiring diagram.
5. Six Ways of Communication between Mitsubishi PLC and VFD
5.1 Using Switch Quantity Signal
The switch quantity refers to the collection and output of discontinuous signals, including remote control acquisition and remote control output. It has two states: 1 and 0. This is the nature of switching in digital circuits, and in the electricity area it refers to the on and off of the circuit or the connection and disconnection of contacts. "On" and "Off" are the most basic and typical functions of electrical appliances.
Generally, the switch quantity device realizes the switch quantity output through the internal relay. The way to simplify the switch quantity of the analog signal DIY is to install a relay that uses the corresponding control voltage at the output end. It can reflect the "existence" and "nonexistence" of the analog signal and realize the conversion of the switch quantity.
The output point and COM point of PLC (type MR or MT) are directly connected to the STF (forward rotation start), RH (high speed), RM (medium speed), RL (low speed), input terminal SG and other ports of the VFD.
The PLC can control the start, stop, and reset of the VFD through the program. It can also control the different combinations of the VFD's high-speed, medium-speed, and low-speed terminals to achieve multi-speed operation.
However, it uses a switch quantity to implement control, and its speed control curve is not a continuous and smooth curve. It cannot achieve fine speed adjustment.
5.2 Using Analog Signal
If you choose Mitsubishi FX1N or FX2N PLC host as the hardware, you can configure one-channel simple FX1N-1DA-BD extended analog output board, analog input and output mixed module FX0N-3A, two-channel output FX2N-2DA, or four-channel output FX2N-4DA module, etc.
This PLC programming is simple and convenient. The speed control curve is smooth and continuous, and the working is stable.
In a large-scale production line, the control cable is long, especially when the DA module uses voltage signal output. At that time, the circuit has a large voltage drop, which affects the stability and reliability of the system.
a technician in blue is seriously programming in front of a computer
Figure 7: A technician is programming.
5.3 Using RS-485 Communication Method
This is the most commonly used method. PLC uses RS serial communication instructions to program.
It has the advantages of simple hardware, strong anti-interference ability, high transmission rate, long transmission distance and low cost. It can control 32 VFDs.
But the programming workload is relatively large. It is necessary to solve a series of technical problems such as data encoding, obtaining checksums, framing, sending data, receiving data parity, overtime processing and error retransmission. Sometimes the programmer wants to let the VFD perform a simple operation instruction, but he needs to write dozens of PLC ladder diagram instructions. So the programming workload is large, cumbersome, and daunting.
5.4 Using RS-485 Modbus-RTU Communication Method
Mitsubishi's new F700 series VFD uses RS-485 terminals to communicate with PLC using Modbus-RTU protocol.
PLC programming in Modbus communication mode is simpler and more convenient than RS-485 protocol-free mode.
PLC programming workload is still relatively large.
close-up of modern programmable logic controllers, their interfaces, wires, switch, operation panel, indicator light showing in this picture
Figure 8: Close-up of modern programmable logic controllers.
5.5 Using Fieldbus
Various types of communication options can be built in Mitsubishi VFDs, such as the FR-A5NC option for CC-Link fieldbus, the FR-A5AP (A) option for Profibus DP fieldbus, and the FR-A5ND option for DeviceNet fieldbus and so on. Mitsubishi FX series PLC has a corresponding communication interface module to connect with it.
It features fast speed, long distance, high efficiency, stable work, and simple programming. A large number of VFDs can be connected.
However, it costs more.
5.6 Using Extended Memory
Here is a very simple way to control the VFD in Mitsubishi FX series PLC communication mode. It only needs to install an RS-485 communication board or hook an RS-485 communication module on the PLC host, and embed a "function expansion storage box" under the PLC panel, which costs a little money. Then after the programmer writes 4 extremely simple PLC ladder diagram commands, the PLC can control 8 VFDs of their reading and writing of parameters, monitoring and control of various operations. The communication distance can reach 50m or 500m.
It is characterized by low cost, easy to learn and use, and reliable performance.
It can only be used in a system with no more than 8 VFDs.
Featured Product
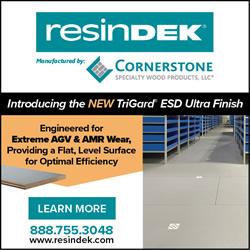