Rapid Robot Rollouts — NexCOBOT GRC Gets Robots From Concept to Completion Faster
NexCOBOT's General Robot Controller (GRC) is a fully-integrated EtherCAT-based general robot controller package for industrial robot development, streamlining the industrial robot development process and helping enterprises accelerate time-to-market.
NexCOBOT's General Robot Controller (GRC) is a fully-integrated EtherCAT-based general robot controller package for industrial robot development, streamlining the industrial robot development process and helping enterprises accelerate time-to-market.
Slated to reach USD 74.1 billion by 2026, at a CAGR of 17.45%, a report by Mordor Intelligence shows robots have bucked recent downward trends. As automation industries drive demand by incorporating more robots into their production lines, robot makers are pushing to expand their customized service offerings.
Automation industries, especially production lines, often struggle to find robots to match their unique optimization use case. Sometimes, even the wide selection of off-the-shelf robots on the market fail to satisfy application requirements. Specially designed robot systems may be the only option for end-users who cannot or don't want to use a ready-made robot. However, custom designs are challenging for robot designers. Robot makers and system builders' biggest obstacle has been supplementing their existing hardware and mechanical design skills with software expertise for motion control, communication module integration.
Now, the NexCOBOT GRC provides robot makers and system builders with a feature-packed easy-to-configure toolkit for EtherCAT network and module setup, a user-friendly teach pendant UI, and open platform development.
Easy-to-use Development Toolkit
The GRC includes an EtherCAT master controller that supports many of the most popular EtherCAT modules and NexMotion Studio software that provides an intuitive 6-step process to help engineers set up the EtherCAT motors, sensors, DIO and AIO modules, and 3rd party I/O modules.
For SMEs with limited development budgets and resources, or larger enterprises looking to reduce the effort required to complete complex robot hardware setup, this mostly-done-for-you approach eliminates the most time-consuming steps in the setup process.
NexMotion Studio enables both EtherCAT and motion setting configuration. EtherCAT settings include scanning and offline editing, master parameters, PDO settings, SDO settings, CiA 402 regulated devices operation, and EtherCAT Network Information (ENI) file export. NexMotion Studio supports multiple robot types and includes settings for single and grouped axes, I/O mapping and operation, robot operation and simulation, and robot configuration (NCF) file export.
Intuitive and Friendly UI
The GRC's NexTPUI is a touch-based UI for robot operation that integrates into many of the pendants available on the market, including NexCOBOT's Teach Pendant, and supports programmable physical buttons. NexTPUI enables setup, configuration, and monitoring of the robot arm and provides built-in features including jog, I/O, monitor, configuration adjustment (tool, base, home, program, jog, track), message logs, and settings (network, system, maintenance, about, language, account).
For precision industrial automation and robot motion control, the NexTPUI includes the NexMotion Real-time Programming Language (NRPL), a C-like programming language for robot arm programming. NRPL includes projects, tasks, and points which mimic the program, function, and variable syntax of regular C while providing multi-task to simplify complex tasks, and built-in motion objects that combine group, object, and motion controls. Other functions include variables, arrays, structures, indexing, subroutines, and calls. Finally, the included math library provides calculation capabilities needed for accurate angles and positioning in precision robot motion applications.
Flexible Open Platform Development
NexMotion Studio has APIs to extend the GRC's core functions, enabling integrators and end users to use their algorithms or AI without adding separate devices, simplifying the resulting system for easier setup and a more integrated experience.
Specialized projects requiring customizations and adjustments to add functionality, such as industrial cameras for AI and AOI applications, often require additional vision control systems that complicate the overall setup and add unnecessary overhead to the system. The NexMotion Studio API can bundle these functions into the final application without complex workarounds or additional systems.
NexCOBOT GRC provides the essential components for easier setup of EtherCAT devices and modules, enhancing user experience through its intuitive NexTPUI user interface, putting complete control in users' hands through the powerful yet familiar programming experience of NRPL, and allowing for customization through the NexMotion Studio API.
NexCOBOT GRC brings faster robot development to enterprises that want to spend less time troubleshooting compatibility issues and shift their focus to value-added application development, so they can get their robot systems from concept to market in the shortest possible time.
Featured Product
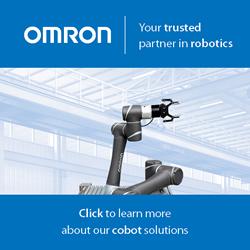
Discover how human-robot collaboration can take flexibility to new heights!
Humans and robots can now share tasks - and this new partnership is on the verge of revolutionizing the production line. Today's drivers like data-driven services, decreasing product lifetimes and the need for product differentiation are putting flexibility paramount, and no technology is better suited to meet these needs than the Omron TM Series Collaborative Robot. With force feedback, collision detection technology and an intuitive, hand-guided teaching mechanism, the TM Series cobot is designed to work in immediate proximity to a human worker and is easier than ever to train on new tasks.