Flexxbotics Provides Robot Compatibility with Hardinge Turning, Milling, Grinding, Honing and Multifunctional CNC Machines
Flexxbotics’ unique FlexxCORE technology enables robots to securely connect and communicate with Hardinge equipment in the smart factory to provide more powerful, flexible and open robot connectivity than previously available.
Boston, MA - November 20, 2023 - Flexxbotics, delivering workcell digitalization for robot-driven manufacturing, today announced robot machine tending connectivity compatible with the full line of Hardinge's automation equipment. With Flexxbotics manufacturers that have precision CNC operations using robotics with Hardinge machinery achieve greater throughput, higher yields and increased profit per part.
Flexxbotics' unique FlexxCORE technology enables robots to securely connect and communicate with Hardinge equipment in the smart factory to provide more powerful, flexible and open robot connectivity than previously available.
Robot compatibility is enabled by Flexxbotics for all different Hardinge machine types including turning, milling and multifunctional machinery from Hardinge, Bridgeport and Weisser, along with the full line of grinding equipment from Hardinge brands including Hauser, Jones & Shipman, Kellenberger, Tschudin, Usach and Voumard, as well as, WPT's laser welding and OTW / Ohio Tool Works vertical & horizontal honing. Flexxbotics compatibility includes both the Hardinge Fanuc and Mitsubishi controllers with connectivity for both current and older models.
"When robots are unable to communicate with the CNC machines they are tending the efficiency gains are minimal and quality issues occur," said Tyler Modelski, Co-founder & CTO of Flexxbotics. "We understand the complexities of robot-machine communication and control which is why we built such robust capabilities in Flexxbotics to give the robots the ability to optimize each machine's operation."
In addition to compatibility with Hardinge's Fanuc FOCAS2/FOCAS and Mitsubishi MELSEC controllers Flexxbotics is compatible with a wide range of open standard protocols including OPC/UA, MTConnect, Modbus-TCP, TCP/IP, Ethernet/IP, and DeviceNet along with Profibus/Profinet and other proprietary controllers and interfacing protocols.
Flexxbotics workcell digitalization is the backbone of the Smart Factory, delivering robot-driven manufacturing at scale with autonomous process control for advanced machining operations. Flexxbotics' SaaS/hybrid architecture also runs both online and offline so production continues with or without internet access, and Flexxbotics works with existing business systems such as CAD/CAM, SCADA/HMI, IIoT, MES, ERP, PLM and others for complete synchronization.
A full set of bidirectional communication, transform and routing capabilities are available in Flexxbotics for the robots and Hardinge machinery that are connected including loading PLC programs, sending instructions, updating parameters and status awareness depending on the equipment's capabilities so the robots drive the machines in the smart factory.
"Flexxbotics enables the robots to do more than simply monitor CNC machines, the robots communicate and instruct the machines for coordinated and optimized operation," said Tyler Bouchard, Co-founder & CEO of Flexxbotics. "We believe robots must be not just intelligent, but empowered to deliver on the promise of robot-driven manufacturing."
About Flexxbotics
Flexxbotics workcell digitalization is the backbone of the Smart Factory delivering autonomous process control for next generation machining environments. Flexxbotics SaaS/hybrid solutions enable robot-driven manufacturing at scale. Flexxbotics breakthrough, the FlexxCORE™ technology, seamlessly connects and coordinates robots with existing automation equipment, IT systems and people. More powerful, flexible and open, Flexxbotics revolutionizes the use of robotics in complex production. Visit www.flexxbotics.com to learn more and follow us on LinkedIn.
Featured Product
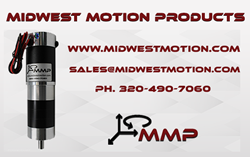