Introducing Sonair, a breakthrough 3D ultrasonic sensor for autonomous robots
Sonair, previously operating in stealth mode, today revealed its developments in sensor technology that improves safety in industrial automation. The company also announced the upcoming launch of its first evaluation kit this summer, signaling a significant advancement in the field of robotics and machine autonomy.
(Oslo, Norway, May 29, 2024) Sonair, previously operating in stealth mode, today revealed its developments in sensor technology that improves safety in industrial automation. The company also announced the upcoming launch of its first evaluation kit this summer, signaling a significant advancement in the field of robotics and machine autonomy.
• Sonair's 3D ultrasonic sensor delivers safe autonomous navigation, cost-effectiveness and very low power consumption in a miniature size that allows for hidden integration
• Enabled by ADAR (acoustic detection and ranging), an ultrasonic 3D technology based on patented research from SINTEF - a leading research institute.
• First evaluation kit to be made available to selected partners summer 2024.
• Supported by leading institutional and venture capital investors.
Sonair, previously operating in stealth, today revealed its innovative developments in sensor technology designed to improve safety in industrial automation. The company also announced the upcoming launch of their first evaluation kit this summer, signaling a significant advancement in the field of robotic and machine autonomy.
The Sonair 3D ultrasonic sensor allows AMRs to detect distance and direction to all objects in a 180x180 field of view, up to a five-meter range. Combined with 2D images and AI, the outcome is confident navigation.
The demand for autonomous mobile robots is increasing, with a growth rate of 30% annually, largely due to their rising use in logistics and manufacturing. Sonair's technology enables effective human-robot interaction by improving safety. It also offers manufacturers considerable cost reductions, by as much as 80% of the total sensor package.
"Today, as we step out of stealth mode, we are excited to share our vision and contributions towards a future where humans and machines can coexist safely and productively," said Knut Sandven, CEO of Sonair. "Our cutting-edge ultrasound technology not only detects obstacles in three dimensions, but does so with unprecedented accuracy and at a fraction of the cost of current sensors."
Founded in 2022 in Oslo, Norway, Sonair specializes in ultrasonic sensors that reduce the financial burden associated with autonomous mobile robots (AMRs). By utilizing patented technology developed at SINTEF's MiNaLab, Sonair's sensors enhance a robot's vision from 2D to 3D, offering a significant improvement over traditional LiDAR and camera systems.
"Our sensors are designed to end the era of expensive laser-based sensors," said Sandven. "With our evaluation kit releasing this summer, we encourage innovators and industry leaders to explore the potential of our technology in transforming machine perception."
Several companies are already exploring Sonair's sensor technology. One is Solwr, a company that develops a competitive combination of robotics and software to automate picking and sorting processes in warehouse and retail environments.
"We are impressed by the technology and the unique opportunity Sonair gives us to offer mobile picking robots with next-generation operational safety solutions. We are really excited to start testing the Sonair 3D ultrasonic sensor on our robot in warehouses," says Olivier Roulet-Dubonnet, Solwr CTO.
Sonair has received strong financial backing, highlighted by a recent seed round that raised approximately 30 million Norwegian kroner from prominent investors including SINTEF Venture VI, ProVenture, Startuplab Founders Fund, and Stratel.
"We are delighted to back Sonair's committed team as they develop safer and smarter robotic systems," said Borgar Ljosland, partner at ProVenture. "Their innovative approach not only enhances human-machine interactions but also opens up significant business opportunities across various industries, including service and delivery robots."
Featured Product
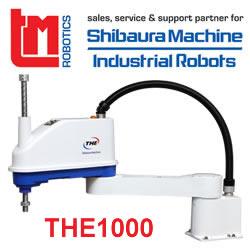