How Do Robotics Affect Skilled Trade Jobs?
With more companies bringing robotics and automation into their facilities, many people understandably wonder if machines will eventually replace their jobs.
Indeed, that has already happened for workers in some lower-skilled roles. For example, most grocery stores now have lots of self-checkout stations and only a couple of cashiers. Some McDonald’s restaurants have kiosks where people order instead of speaking to a human.
But what’s the likely impact on people who work in skilled trades? Here’s a closer look.
Automation Cannot Replace Human Expertise
Many of the product descriptions of automated tools claim that people can set them up and largely cease their interactions with them after that. However, even the most advanced robot only works as well as its underlying programming.
People can still make mistakes when setting up an automated system, which is why many companies have started hiring individuals with expertise in robotics and automation. In one case, a company collected more than 38 million data points per day using automated monitoring equipment on critical machines.
Eventually, two failures occurred that took months to remedy. A closer investigation showed that installers did not set the automated system up properly. Additionally, there were system gaps that limited positive outcomes.
This example highlights why people cannot take a set-it-and-forget-it approach to automation. It also suggests that some individuals working in skilled trades may find themselves in even higher demand if they have robotics knowledge.
The recently launched READY Academy is an online platform geared for manufacturing professionals who want to gain robotics expertise. Its modules cover how to deploy, manage, scale, and design automation at a plant.
Robots Could Relieve Skilled Tradespersons From Repetitive Work
Statistics show that 54% of construction contractors have trouble finding enough skilled workers. Relatedly, 81% of respondents said the skilled tradespeople they do have must take on more work to accommodate the lack.
Robots could play an instrumental role in handling the tasks that could make skilled workers more prone to fatigue and injuries. Jim Page is a veteran of the heating, ventilation, and air conditioning (HVAC) industry who currently trains apprentices. He gave an example of how robots could help with welding.
“In the shop production side, if it takes three welders to get it done and part of the process being done by two of those welders is a repetitive process, that process could be put into a jig and could be performed by a robot.” However, that doesn’t take humans out of the picture.
Page continued, “A knowledgeable person who understands the programming and understands the welding side can operate it. Because you’ve got to know all the different steps of the type of weld you want … so that the individual doing it knows what he’s programming on that keyboard. Or you’re going to get a weld, but it may not be the weld that you needed to have there.”
That scenario is another example of how it’s useful for skilled tradespersons to understand the specifics of their work, plus how to tell robots to get the job done correctly. Otherwise, incorrect programming could create more work for skilled people rather than removing the burdens.
Automation Does Not Affect All Areas Evenly
A 2020 talent survey found that skilled trades are the hardest roles for employers to fill. Some people may assume automation could help fill some of those gaps, but that’s not necessarily true.
Robots excel at jobs that occur in relatively stable conditions. Some construction crews use them for tasks like bricklaying. However, skilled tradespersons such as plumbers and electricians will typically use different skills during every client appointment. Each environment and customer has variations. Thus, some automation experts insist that jobs like those will be among the last ones people try to automate.
Moreover, an MIT study showed that automation does not have a universal impact across the country. The researchers confirmed that blue-collar workers are among those most at risk for replacement by automation. However, they recorded significant differences in adoption levels in the United States.
The researchers also expect robots to negatively affect wage growth and employment levels, but they noted that it’s too early to predict the extent to which those things will happen.
Current data showed them that every robot added per 1,000 American workers made wages fall by 0.42% as the employment-to-population ratio decreases by 0.2 percentage points, however.
No Uniform Outcomes
It’s too simplistic to say robotics and automation will have a uniformly positive or negative impact on the skilled trades. Many such professionals use tools like automated invoicing platforms to reduce administrative work, for example. However, automation seems more likely to negatively impact people who don’t aim to educate themselves about emerging technologies.
Comments (0)
This post does not have any comments. Be the first to leave a comment below.
Featured Product
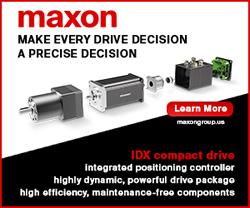