Will RTLS be the Next Big Step for Automation?
There is so much change taking place in factories and industrial environments, it can be hard to keep track of the latest buzzwords and terminology. Since the explosion of IoT (Internet of Things) devices over the last six years, the smart factory revolution has gripped the imagination of many enterprise managers, but many don’t know where to start – I suggest looking into RTLS (Real-Time Location Systems).
What is RTLS?
Real-time Location Systems have existed for a long time in one form or another. Growing out of warehouse and logistics management systems, RTLS has aimed to track the precise location of all objects within a system, whether that be a factory, transit yard, warehouse, hospital, or military base. This is usually achieved through a system of tags and sensors, with the resulting data being processed by a centralized software system either onsite or in the cloud.
By knowing where a system’s products, tools, vehicles, raw materials, and personnel are at any given time, one can gain far better oversight of all processes, while opening the door to task automation, AI forecasting, and improved safety measures.
What technology does an RTLS use?
This is where things get more complicated. There are many different types of technology being used in RTLS systems, and some will be better suited to certain industrial environments than others. There will also be a great variety in the quality of different systems, which will effect both the accuracy of the systems and their reliability.
Some examples of RTLS technology include:
RFID – This is perhaps the most well-known tracking technology. It usually consists of “passive” tags that are attached to goods and products and require manual scanning. The data provided by these tags is limited and will not provide locational data. However, RFID can be useful for simple inventory management, and new “active” RFID tags can emit signals with more detailed information, but still lack the accuracy and reliability of other RTLS systems.
BLE (Bluetooth Low Energy) – This is another well-known technology, mostly due to its use in mobile phones, iPads, and computers. It is currently widely used in many industrial settings due to its ease of setup and its ability to incorporate many common handheld devices. By tracing the rough location data of Bluetooth devices, a BLE RTLS can be used for gatekeeping purposes, sending alerts when people enter restricted areas, or performing headcounts of personnel. It lacks the accuracy of other RTLS technologies, so it won’t be useful for some tasks, including the precision parking of vehicles, automatic tool calibration and tool management, and other precise interactions between objects or personnel. Bluetooth is also prone to interference from other radio signals, making it less useful in mission critical deployments.
A UWB sensor in an industrial setting
UWB (Ultra-wideband) – This is the increasingly popular choice in many industrial settings. UWB is a unique technology, as its radio signals are both extremely reliable and can be tracked to within a few centimetres. While there are differences in the accuracy of different UWB offerings, most UWB will be able to perform precision tracking in the most complex environments. Many factories will be chock-full of machinery, vehicles, and Wi-Fi signals – but UWB tends to perform well regardless. The technology is even becoming more ubiquitous in mobile phone technology.
One last benefit to UWB is its ability to track objects in 3D, allowing for height sensitive tasks to be tracked an automated.
RTK GPS – This technology is a twist on the same GPS technology we use on our phones. While GPS is now reliable and relatively cheap to use, it still isn’t ideal for the tracking of objects in indoor environments, and outdoors it still only tracks things to within a few meters. RTK GPS solves this problem and creates centimetre-level GPS by modifying the GPS signal data with extra data usually sent from a separate base-station receiver on the ground. This extra data accounts for common errors that cause GPS data inaccuracies. The result is one can track assets accurately in large outdoor spaces.
Is RTLS software easy to use?
This is a difficult question, as it depends on what you are hoping to achieve from your RTLS system. If an RTLS is deployed with the simple aim of tracking assets to prevent search time across a site when assets go missing, then the software interface and utilization will be straight forward. If one is hoping to gain oversight of a complex factory floor and determine the system bottlenecks, and deploy predictive analytics and automation processes, then the software can be more complex. The important thing to understand is that many RTLS software systems will be customizable to your needs and any serious RTLS provider will help you get up and running and will offer support services to ensure you utilize their system effectively.
As you can see from the above, there is plenty to consider when choosing an RTLS system. It is advisable that you keep an open mind regarding the best technology to use and speak to an RTLS provider who has a strong track record in your industry.
Steven Manifold, CMO at Ubisense.com.
Comments (0)
This post does not have any comments. Be the first to leave a comment below.
Featured Product
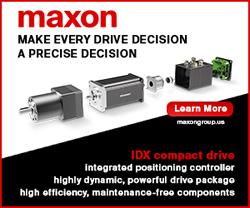