Amazon announces over €700 million investment in robotics and AI powered technologies across Europe
Nestling among the centuries-old rice fields of Vercelli, northern Italy, is a building that is shaping the future of work. The Amazon Operations Innovation Lab is one of Europe’s most advanced centres for robotic innovation, an international centre of excellence where scientists and engineers develop and test new technologies, including advanced robotics and AI-powered innovations that are shaping the future of work across our network.
Investing in advanced technologies across Amazon’s European fulfilment centre network
Established in 2017, the lab serves as the hub for the global Mechatronics & Sustainable Packaging team. This team was formed in 2019 and by the end of 2024 will have been responsible of the installation of over 1,000 new robotics and AI-powered innovations throughout our European fulfilment centre (FC) network, representing an investment of more €700 million. These cutting-edge technologies encompass item sorters, pallet movers, and automated guide vehicles, actively supporting Amazon employees in their roles across our sites. Robotics and technology play a crucial role in enhancing our operations network, while AI enables us to scale these advancements for a global operation serving millions of customers worldwide.
With each technology comes different skill requirements, and in many cases the creation of new specific roles. In fact, over 50,000 jobs in FCs across Europe have been enhanced by the introduction of new technologies over the last decade which support employees in their roles, providing them with a safer working environment and upskilling opportunities.
At the same time, robotics and AI-powered innovation improve price, selection, and convenience for our customers. It is one of the factors that in 2023 enabled us to deliver to Prime members at the fastest speeds ever globally, with more than seven billion units arriving the same or next day, including more than four billion in the U.S. and more than two billion in Europe.
An international hub for people: from training teams to public tours
The lab is more than just the international innovation hub for Amazon teams. It serves as a training centre for Amazon Robotics operators, as well as a testing ground for start-ups receiving funding and guidance through the Amazon Industrial Innovation Fund. Moreover, starting in 2024, the lab will be open for public tours, offering customers, schools or anyone interested the opportunity to discover how we create and develop innovations.
“We are proud to open the doors of our lab, not only as a hub of innovation for Amazon, but to encourage customers, schools, and start-ups to be inspired and learn about the potential for technologies to create a better and safer future of work,” said Stefano La Rovere, our Director for Global Robotics - Mechatronics & Sustainable Packaging. “At Amazon, our commitment to thinking big runs deep – over five years to the end of 2024, we will have invested over €700 million in the deployment of more than 1,000 robotics systems across our European fulfilment centre network. In addition, the introduction of new technologies over the last ten years has enhanced 50,000 new jobs within our operations in Europe.”
Stefano added: “The lab is host to a diverse and international team of engineers and scientists dedicated to finding innovative ways to enhance everyday tasks for our employees, providing a safer workplace while consistently delivering for our customers.”
In 2024 alone, we expect to introduce 120 new pieces of automation technologies across our European network. Here are some of the most exciting innovations emerging from Amazon labs in recent years, including the Universal Robotic Labeler (URL) that was unveiled today, and how they are reshaping our workplace and beyond.
1. Universal Robotic Labeller (URL)
The URL (Universal Robotic Labeler) is a high-speed auto-labelling technology that improves label placement and adhesion on irregular surfaces. Its innovation lies in its ability to apply different types and dimensions of labels, and on different types of irregularly shaped products. On one hand, it allows for applying smaller labels, hence reducing packaging dimensions; while on the other it allows for placing labels on paper-bags, even irregularly shaped ones, or directly onto products to ship in product packaging, eliminating the need for additional packaging and contributing to reduced waste on the customer’s side. The URL machine represents a significant advancement in our fulfilment technology. It improves the entire labelling process, contributing to our sustainability goals, and, ultimately, benefiting our employees’ roles, customer experience, and the environment.
2. Universal Item Sorter (UIS)
The Universal Item Sorter (UIS) ensures that thousands of products are efficiently sorted into shipping locations every day. Upon induction, the system utilises advanced wireless technology to move shuttles, called iBOTs, that travel in various directions carrying the items and delivering each to a tote – already matched to its final destination. This meticulous planning ensures the accurate pairing of the right item with the corresponding tote. The UIS prioritises safety and ergonomics in the workplace. By incorporating intelligent technology, it minimises physical strain on employees, contributing to a safer workplace. Furthermore, the UIS provides space-efficient sortation capability: this system can accommodate up to 40 different totes, corresponding to 40 different destinations, in a compact footprint. This allows us to reduce our building dimensions, in turn reducing both our footprint and energy consumption.
3. Automated Tote Retriever (ATR)
The Automated Tote Retriever (ATR) complements the UIS (Universal Item Sorter) in optimising processes and improving safety and ergonomics for employees. A shuttle connected to the UIS moves on a rail track along the full length of the UIS wall and receives notifications when a tote is full. In response, the shuttle moves towards the full tote, using a special gripper to replace it with an empty one. Once completed, the UIS resumes delivering items to this location, repeating the process seamlessly. By automating the tote replacement process, the ATR reduces manual effort, contributing to a more streamlined and ergonomic workflow with fewer steps and reduced lifting for our employees, while improving efficiency.
4. Bag Containerization Matrix Sorter (BCMS)
The Bag Containerization Matrix Sorter (BCMS) optimises our sorting capacity by identifying and grouping parcels with the same end destination within FCs, providing an ergonomic and space-efficient sortation capability, within a compact footprint. The system innovatively categorises packages into transportation bags, ready for last mile delivery. This avoids unnecessary double touch of the same parcel in an FC and in a sort-centre, optimising operational efficiency, while reducing human effort.
5. Automated Guided Cart (AGC)
The Automated Guided Cart (AGC) is a flat, autonomous robot on wheels that slides under stacks of empty totes, and automatically carts them around FCs. In so doing, it reduces the need for employees to push or carry heavy loads over long distances. Sensors on the bottom of the robot read a magnetic tape on the floor to self-navigate, while safety scanners detect if any people or obstacles are in the way so the AGC can slow down or stop, until the path is clear.
6. Flat Sorter Robotic Induct (FSRI)
Robots love things to be in order, and the FSRI is a clever piece of kit that ensures packages move through the FC at a smooth, steady, and ordered rate. The FSRI takes over repetitive tasks, making life easier for employees. With smart vision sensors, it spots packages wherever they end up on the conveyor, and a nifty robotic arm swoops in to pick them up and send them on their way. Additionally, the robot's 'hand' uses suction cups to gracefully handle all sorts of packages.
7. Robotic Tote Palletizer (RTP)
The Robotic Tote Palletizer (RTP) technology is a fundamental part of the palletisation process. It has two robotic arms working in harmony to condense several totes into neat, double-stacked pallets with precision and care. The first arm gathers three or four layers of totes on a single pallet, while the second stacks two pallets on top of each other, creating a single unit. The RTP then ties everything safely together with straps, and applies a shipping label, before an employee moves the double stack safely into a trailer destined for the shipping dock. It’s a complex series of actions that contributes to a safer and more ergonomic process, ultimately saving employees from repetitive heavy-lifting.
8. Amazon’s automated packaging technology
Our automated packaging technology creates custom-fit paper bags on demand by scanning items and calculating the right amount of paper needed for quick and accurate packing. This machine packs individual items – such as video games, sports equipment, and office supplies – in made-to-measure paper bags which are durable and flexible. Using heat-sealing technology, it secures each bag, minimising empty space. By packing items in 100% recyclable light paper packaging, which is made-to-fit without the need for padding, the machines help to avoid more than 26 grams of packaging per shipment, on average. Lightweight paper bags used by Amazon are up to 90% lighter than similar-sized cardboard boxes.
9. Amazon Robotics Floor
The Amazon Robotics Floor is the heart of a fulfilment centre. It transforms inventory management while prioritising employee safety and comfort in a space where technologies work together in harmony with people to store and pick millions of items. Thousands of AR (Amazon Robotics) drive units efficiently and navigate under the yellow pods, bringing them to ergonomic workstations and back to the inventory storage area. This eliminates the need for employees to walk long distances when transporting items.
Comments (0)
This post does not have any comments. Be the first to leave a comment below.
Featured Product
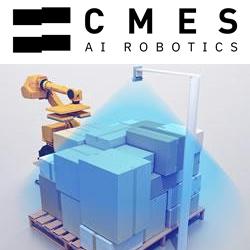