What Are the Secrets to Optimizing Motion Control in Robots?
While robot costs have fallen over time, automation is still a significant investment in most cases. Consequently, businesses must tailor their robotics solutions to their situation to maximize the benefits and justify these expenses. Optimizing motion control systems is a crucial part of this endeavor.
The Importance of Optimizing Motion Control
It is difficult to overstate the importance of robotic motion controls. Without these technologies, machines could not move on their own. Losing autonomous movement renders physical automation useless.
Motion control optimization is about more than ensuring a robot can move. It must also move correctly — meeting the ideal speed, power, direction, length and timing. Assurance in each of these categories is necessary because these are what separate robots from human employees.
Cost and capacity improvements are the most common drivers behind automation, accounting for 62.2% and 54.1% of robot adopters, respectively. Neither of these goals is possible without reliable motion systems. A robot that cannot consistently meet movement needs won’t produce cost-saving productivity benefits or boost throughput.
Motion optimization is not the only way to drive reliability and cost-efficiency in robots. However, it is a crucial one. While manufacturers can go further than these improvements, they must start here to ensure baseline performance.
How to Optimize Robotic Motion Control
Ensuring robotic motion control delivers on its promise requires attention to a few key considerations. Here are five steps to optimize these systems for a stronger return on investment.
1. Determine the Type of Motion
First, manufacturers must identify the kind of motion their robot will perform. At its most basic level, this means determining the movement direction — such as moving side to side or up and down. Beyond that, businesses should consider their needed fluidity and range of motion.
These considerations have a considerable effect on robot price and complexity. A robotic arm placing components on a product may only need one or two single-axis actuators. Autonomous mobile robots (AMRs), which account for 32.13% of all robotics adoption, must support more directions and more fluid movements, requiring more complex motion systems.
In addition to determining the number of axes and types of actuators required, these choices dictate a robot’s power system. It takes less energy to move a single joint than to propel a robot along a factory floor.
2. Consider Power Requirements
Once manufacturers know the type of motion their robot requires, they can consider this movement’s power. The appropriate amount of force depends on the weight of the moving parts, expected resistance, desired speed and the specific task at hand.
Meeting these requirements is more than ensuring a motor can deliver enough force. The kind of power matters, too. Moving a robot on wheels requires constant, steady force while punching a die through metal necessitates explosive power. Even if these solutions involve the same amount of energy, they deliver it in different ways, so they require different motion systems.
Power delivery is not the only factor to consider, either. The motion control system must also withstand the force it exerts or the resistance it encounters. Even when components support the same speed and radial load, some last up to 5.31 times longer than others, making them better for high-intensity applications.
3. Ensure Precision
Similarly, robotics motion control systems must deliver the needed amount of precision. This factor must go hand in hand with power considerations, as the two often conflict. High power delivery results in faster speeds but requires more force to stop at a desired point, hindering precise movement.
Precision can stem from several places. Using lighter materials to reduce power requirements and force is one option. Equipping a motion control system with faster-acting sensors is another. The ideal approach depends on the manufacturer’s budget and the robot’s other needs.
Generally speaking, closed-loop control systems enable the most precision as they respond to both input and output measurements. Open-loop alternatives cannot respond to real-time variations, making them less reliable, but they are cheaper to implement and require less data. Consequently, robots with more predictable workflows can rely on open-loop controls.
4. Use Appropriate Motion Control Sensors
Manufacturers can also optimize motion controls through their choice of sensors. This consideration is more complex than it seems at first because the right sensor for a robot depends on more factors than precision alone.
Lasers offer fast, accurate measurements, making them ideal for guiding a cutting arm or sensing objects on an assembly line to initiate motion. However, they struggle to provide the wealth of data necessary for more complex tasks, such as guiding autonomous vehicles, without expensive setups. In these cases, camera-based machine vision may be more reliable, but it introduces more room for error and requires sufficient lighting.
Some robots may need to combine multiple sensor systems. AMRs and other mobile systems may require one sensor group to navigate and another to control independently moving arms.
5. Provide Adequate Computing Resources
Relatedly, robots and their underlying infrastructure need enough processing power to respond to this sensor data. Once again, the required complexity depends on the specific bot and its task.
Robots performing simple motions do not need much computing power, as their programming is straightforward and they likely process minimal data. Machine vision systems and other AI applications, by contrast, must perform complex analyses. In some cases, onboard computing resources may be insufficient, requiring cloud connections.
Manufacturers should consider their network infrastructure in cases requiring more complex computing or connection to multiple sensors. Edge computing can make these connections more reliable, boosting latency by up to 30%, but this strategy requires more tech investment. Considerations like these can quickly raise a robot’s implementation costs, so it’s important to review them early.
Robotic Motion Control Requires Close Attention
Any physical robot needs a motion control system that suits its end use. Manufacturers must address this need if they hope to profit from their robotics investments.
Ensuring reliable motion control is often more complex than it appears. However, if manufacturers and robot designers can pay attention to these factors, the resulting benefits will more than make up for the costs and complexity of the design. Following these steps will help organizations meet these needs and design better robotic motion control systems.
Comments (0)
This post does not have any comments. Be the first to leave a comment below.
Featured Product
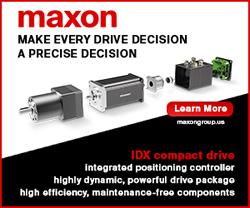