These 7 Emerging Technologies Are Allowing for Fully Automated Warehouses
Warehouses are essential to a functioning supply chain. However, many of these facilities struggle to maintain optimal efficiency amid rising demand, and labor shortages further hinder them from reaching their full potential. Automation has emerged as an ideal solution to these issues.
The idea of a fully automated, “lights-out” warehouse may seem lofty, but today’s technology is not far off. Several recent innovations are paving the way for facility-wide automation, and as this trend continues, they could reshape the industry.
1. Automated Warehouse Management Systems
Warehouse management systems (WMS) are already prevalent throughout the logistics sector. They’re the most-adopted technology among third-party logistics providers (3PLs), with 84% of 3PLs using them as of 2021. While the software is not technically an automation solution, it makes extensive automation feasible.
A WMS provides a single repository for all warehouse data, including inventory levels, fleet information, logistics routes and operational performance indicators. Automated equipment throughout the facility can use this data to work efficiently and accurately. Having a single source of truth also ensures all robots act on the same information, preventing errors.
WMS solutions can also track a warehouse’s automated technologies to give companies insight into their efficacy. Consequently, it becomes easier to adjust automation initiatives to achieve optimal results.
2. Automated Storage and Retrieval Systems
Regarding physical automation, automated storage and retrieval systems (AS/RS) are among the most promising emerging technologies. These systems pick items from shelves or store incoming goods. As simple as that is, it can be a considerable time-saver.
Picking is often a warehouse’s most inefficient process, as employees spend up to 50% of their time walking between locations. Consequently, automating it through AS/RS removes significant amounts of time waste. AS/RS systems can also move faster than people, using vertical tracks to scale shelves quickly or ceiling-mounted ones to avoid traffic on the warehouse floor.
AS/RS itself is not new, but recent advances have made it additionally impactful. Connecting it to a WMS or Internet of Things (IoT) sensors lets it improve picking accuracy by delivering real-time data on each product’s exact location. Newer solutions are also less bulky, making it possible to integrate them into smaller facilities or safely apply them to high shelves without weight-related risks.
3. Autonomous Mobile Robots
Once AS/RS retrieves items from a shelf, autonomous mobile robots (AMRs) can transport them to the loading bay. Many warehouses already use automatic guided vehicles (AGVs) for this purpose, but AMRs have emerged as a better alternative.
AMRs can create routes in real time through laser guidance systems and GPS, whereas AGVs must follow pre-defined paths. As a result, AMRs are more adaptable — an area where robotics often struggles — and require less infrastructure. Such adaptability is key for long-term results, as warehouses may need to change their setup over time to optimize space and operations.
Machine learning models take AMRs’ benefits further. Such technology can equip them with object recognition features or self-driving algorithms to improve responsiveness and flexibility. Alternatively, robots could use AI to analyze potential routes and find the best one in near-real time, ensuring maximum efficiency.
4. Truck-Loading Robots
An automated warehouse must also have a way to load retrieved goods onto outgoing vehicles. While such technology is not quite as mature as AS/RS or WMS, recent iterations show significant potential.
FedEx recently adopted a dual-armed truck-loading robot to pack boxes in a fraction of the time it’d take a human. More impressively, the solution uses AI to compare billions of possibilities in 500 milliseconds, determining the ideal package layout to make the most of the available space. This analysis reduces the number of trips necessary to move goods, resulting in lower transportation costs and emissions.
Similar robots can unload trucks delivering products to the warehouse. These can be as simple as a conveyor belt and a single robotic arm, but even such a straightforward setup saves time and prevents musculoskeletal injuries to workers.
5. Autonomous Vehicles
Before long, the fully automated warehouse could include automated transportation as well. While self-driving trucks have yet to become a viable option for businesses, the underlying technology has seen several notable improvements over the past few years.
Level 4 autonomous vehicles are already operating in the U.S. and a few other countries. Public transportation and taxis account for many of these systems, but the shift still affects warehouses. As driverless cabs complete more journeys, they generate additional data for their AI to learn from, leading to necessary accuracy and flexibility improvements in self-driving models.
Driverless vehicles may come to logistics processes before they reach mainstream adoption in consumer circles. Truck routes tend to stay mainly on highways, which have predictable traffic patterns. Consequently, AI models would not need to advance as much to work in this environment.
6. Edge Computing
Many of these emerging technologies work best when they can communicate with other automated systems and process large data volumes. Doing so conventionally can be difficult, but edge computing provides an answer.
Like WMS, edge computing is not an automated technology but a complementary innovation to make automation viable. Instead of processing data locally or in far-away data centers, edge networks distribute computing tasks across nearby devices and small-scale IT infrastructure. As a result, it enables faster data processing without equipment needing more built-in computing resources.
Studies show edge networks can reduce latency by up to 30% compared to the cloud. Consequently, AMRs, AS/RS and other automated solutions in a warehouse can respond to changing conditions or identify optimal workflows in minimal time. Processing errors will also become less common, resulting in greater uptime and precision.
7. Predictive Maintenance
Another complementary technology with high potential is predictive maintenance (PdM). This practice uses IoT sensors and AI to monitor real-time equipment health and alert businesses to emerging repair issues.
A fully automated warehouse means a greater number of machines within a facility. Consequently, maintenance costs and downtime are pressing concerns. PdM helps because it warns of incoming problems while they’re still small, enabling cheaper repairs and preventing breakdowns. However, unlike most preventive maintenance strategies, it does not require stopping workflows to inspect equipment.
Some brands have achieved 20% reductions in downtime by implementing PdM. Improvement on that scale would make fully automated warehouses far more cost-effective and resource-efficient.
The Automated Warehouse of Tomorrow Begins Today
Lights-out warehouses may not yet be a widespread phenomenon, but they could become a reality soon. The shift will start with these seven technologies, which are already making impacts today. Learning to work with and implement these systems will help organizations stay ahead in a quickly shifting industry.
Comments (0)
This post does not have any comments. Be the first to leave a comment below.
Featured Product
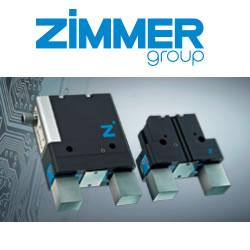