Automation in the food industry: How smart palletizing holds the key
In food production, much like in other industries, numerous factors could slow down the overall flow of production. Consider labor-intensive tasks such as stacking products onto pallets for shipment, which are also prone to human error. There could be inconsistencies in stacking efficiency or potential damage to products, leading to food waste and unwarranted costs.
Add to this the fact that the food industry faces unique challenges, including the need to adhere to stringent hygiene and safety regulations. Manual handling heightens the risk of contamination and could put product integrity on the line. Then there is the labor shortage to deal with. In short, you simply can’t cut corners when it comes to operating in a clean and controlled environment in the food industry. In response to these challenges, automation is increasingly being adopted within the industry. Let’s explore how it makes a difference.
Unique challenges call for distinct solutions
To stay on top of changing consumer preferences, manufacturers need to constantly innovate and experiment with their products (think seasonal products and limited-time offerings). If their warehouses cannot adapt dynamically to accommodate novelty and heterogeneity, that would indeed make it challenging for them to keep up. That’s where automated solutions come in, enabling a smooth transition between multiple product lines and minimising disruptions in an already delicate supply chain.
Automation solutions, like automated palletizers, offer certain specific advantages tailored to the needs of food production. For instance, Smart Palletizer is a compact, single SKU handling solution that efficiently stacks products onto a pallet. It has found practical applications across the food industry, including sectors like coffee, snacks, confectionery and bakery, helping to address various challenges in both production and outbound processes.
Managing variety with accuracy and efficiency
One of the standout features of the solution is its ability to manage a diverse range of products, each varying in shape, size and weight— much like the assortments found on supermarket shelves. It is interesting to note that stacking open boxes is a feature that most cobot palletizing solutions lack. Thanks to the fork gripper, the Smart Palletizer is able to stack open boxes easily.
Whether it’s introducing entirely new product lines or altering existing ones, the system can easily adjust to support different products, enabling producers to stay on track with their goals. It can accommodate different stacking patterns and configurations, enabling quick adjustments to meet changing production requirements without significant downtime or reconfiguration. The Smart Palletizer also optimizes pallet configurations to maximize space utilization, allowing companies to store more products within their existing facilities. By creating stable, uniform stacks, it also facilitates easier handling and transportation, making the outbound process smoother and efficient. After all, maintaining operational efficiency, mandates an effective use of warehouse space.
The lower the risk of error, the smoother the outbound process will be. Misplaced or incorrectly stacked products can lead to significant delays and unnecessary costs. By ensuring consistent stacking patterns and precise pallet arrangements, smart palletizing can enable companies to fulfill orders with enhanced accuracy and timeliness. Similarly, automated handling also reduces the likelihood of contamination, ensuring the products meet the health and safety guidelines that govern the food industry.
Creating a safer, better workplace with automation
Manual palletizing is not only a physically demanding and mentally taxing task, but also a hazardous one that can lead to workplace injuries, ergonomic challenges and employee dissatisfaction. It is hardly surprising that warehouses often face high rates of sick leave and employee turnover. Automation should ideally relieve employees of repetitive and physically straining tasks, not only to boost their morale but also to allow them to apply their intellectual capital effectively in areas that require critical thinking, creativity and problem-solving skills. Given its ability to operate round the clock with an average availability rate of 99.7%, Smart Robotics designed the smart palletizing solution to save up to 3 employee shifts per day. Besides productivity, this also ensures that food products are handled with utmost safety and efficiency.
It is also important for robotic solutions to work harmoniously alongside human employees in a warehouse. A cobot solution like the Smart Palletizer designed for safe human-machine collaboration can operate without safety fences, which in turn minimizes its footprint. This setup allows employees to move around freely in warehouses, remove full pallets and load empty pallets, all while the cobot continues its operation.
Uninterrupted, consistent processes as an answer to end-of-line challenges
As discussed above, with automated systems, it is possible to keep production lines running continuously across multiple shifts without fatigue. By helping prepare products for shipment quickly and reliably, this consistent and high-speed performance allows food manufacturers to meet tight delivery schedules, even during periods of peak demand. Especially in an industry where freshness, safety, and availability are critical and non-negotiable, automation ensures that products maintain the highest standards in both quality and quantity.
The adaptability of the smart palletizing system makes it a versatile choice for handling multiple product lines, while its effortless integration with existing infrastructure makes it an accessible solution for a wide range of food production plants. Even small companies can start with standard palletizing systems and scale up as their production needs grow. Today, features such as remote monitoring and troubleshooting accompany modern automation solutions, helping resolve issues quickly without halting production. This means that by reducing the need for manual intervention, even when it comes to troubleshooting, automation empowers businesses to consistently meet their delivery commitments on time and maintain their competitive edge in the marketplace.
About Smart Robotics
Smart Robotics is a leading developer of robotics and automated warehouse systems. Their pick and place robotic solutions are engineered to improve overall capacity, increase the reliability of warehouse operations, and tackle issues related to the continuing labor shortage in the logistics industry. These solutions are driven by Smart Robotics’ advanced AI tech-trinity, hardware and software. Smart Robotics’ customised automation solutions aim to improve working conditions for warehouse floor workers by taking over repetitive and physically strenuous tasks, such as order picking, packing, palletizing, and sorting.
About Heico Sandee
Smart Robotics Founder and CEO, Heico Sandee, holds a PhD degree and previously acted as program manager for robotics at Eindhoven University of Technology. With more than 15 years of experience in robotics development, Heico now leads Smart Robotics in developing intelligent, robot-independent software for flexible deployment of automated solutions.
Comments (0)
This post does not have any comments. Be the first to leave a comment below.
Featured Product
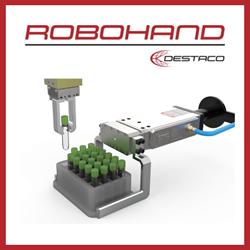