How Autonomous Mobile Robots are Transforming Material Handling for Automotive Tier Suppliers
Automotive tier suppliers are under constant pressure to streamline their operations, reduce costs and deliver on increasingly tight deadlines. The demand for faster production, while maintaining high-quality standards, continues to intensify. To meet these challenges, many suppliers are turning to autonomous mobile robots (AMRs) to improve their material handling processes.
This article will explore how automotive tier suppliers can leverage AMRs to streamline material handling, cut operational costs and improve workforce safety—all without the need for expensive infrastructure overhauls.
The Shift to AMRs
Automotive tier suppliers are tasked with meeting the demands of original equipment manufacturers (OEMs) while managing costs and maximizing productivity. Historically, this meant investing heavily in fixed infrastructure like conveyor belts, automated guided vehicles (AGVs), or even forklifts and manual labor. However, such systems come with significant limitations. Fixed infrastructure can be expensive to install and difficult to modify, especially when production requirements change. Additionally, AGVs require predefined paths, which often demand physical modifications to the facility and lack the flexibility needed for dynamic manufacturing environments.
AMRs represent a more adaptable and cost-effective alternative. Unlike AGVs, AMRs use advanced sensors, cameras and machine learning algorithms to navigate autonomously throughout a factory or warehouse. This flexibility allows tier suppliers to quickly adjust to shifting production needs without making costly changes to the facility's layout. AMRs can also be deployed alongside existing processes, making them an attractive option for facilities looking to modernize their operations without major disruptions.
Reducing Costs
One of the most compelling reasons automotive tier suppliers are turning to AMRs is the potential for cost savings. Labor costs, in particular, can be a significant burden on tier suppliers, especially in markets where skilled labor is in short supply. By automating material handling tasks, AMRs can significantly reduce the need for manual labor, freeing up employees to focus on more complex, value-added tasks. The use of AMRs can also decrease the likelihood of human error, which can lead to production delays or quality issues.
AMRs also offer long-term cost advantages in terms of scalability. Unlike fixed automation systems that may require substantial modifications to expand, AMRs can be deployed incrementally, allowing suppliers to scale up or down as needed without disrupting ongoing operations. This flexibility is particularly valuable in the automotive industry, where production volumes can fluctuate based on market demand, new vehicle launches, or supply chain disruptions. AMRs can be quickly reprogrammed to handle new tasks or rerouted to different areas of the factory, making them an ideal solution for dynamic environments.
Maximizing Productivity
Beyond cost savings, AMRs can significantly boost productivity for tier suppliers. With the ability to operate around the clock, AMRs help reduce downtime and ensure that materials are delivered precisely when and where they are needed. This continuous operation minimizes bottlenecks and allows for smoother, more efficient production processes.
AMRs are also capable of handling a wide range of material types, from small parts to large components, making them versatile assets in an automotive facility. Tier suppliers can program AMRs to manage different material handling tasks, from transporting raw materials to delivering finished products, all while adapting to changes in production schedules or layouts.
The data-driven nature of AMRs also provides an additional advantage in terms of operational insights. AMRs can collect and analyze data on material flow, identifying potential inefficiencies in real-time. This information allows tier suppliers to make informed decisions on how to further optimize their material handling processes, leading to greater overall productivity and efficiency.
Enhancing Workplace Safety
AMRs also play a crucial role in enhancing workforce safety. Manufacturing environments can be hazardous, with heavy machinery, moving parts and congested workspaces posing risks to workers. AMRs can help reduce these risks by taking on some of the most physically demanding and hazardous material handling tasks.
With their advanced sensors and obstacle detection systems, AMRs are designed to safely navigate complex factory environments, avoiding collisions with both objects and people. This reduces the likelihood of accidents, including collisions involving forklifts or manual handling equipment.
The Future of Material Handling for Tier Suppliers
As the automotive industry continues to evolve, so too must the supply chains that support it. Looking ahead, we can expect AMRs to play an even greater role in enabling suppliers to meet production demands, especially as global production growth is expected to grow by 15% by 2028. For tier suppliers looking to stay competitive in an increasingly demanding market, AMRs offer a clear path forward to greater efficiency and operational excellence.
Comments (0)
This post does not have any comments. Be the first to leave a comment below.
Featured Product
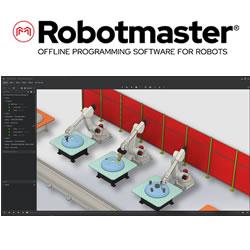