Dürr equips first BYD plant in Europe with sustainable painting technology
The Chinese electric vehicle manufacturer BYD Auto Company Limited is building its first European passenger car plant. To equip it with painting technology, BYD selected Dürr. Over the coming months, the German mechanical and plant engineering company will send more than 120 robots to Hungary for various painting lines. These robots, fitted with EcoBell3 atomizers, deliver outstanding quality and support sustainable painting.
BYD Auto Company Limited, is one of China’s largest vehicle manufacturers, ranks among the market leaders in electric vehicle sales. Now, the company is building a European car factory in Szeged, Hungary, becoming one of the first Chinese car manufacturers to do so. For painting its “New Energy Vehicles” (NEV), BYD has partnered with Dürr. For this project, Dürr will supply and install more than 120 painting and handling robots. “As a world market leader in automotive painting, Dürr is the right partner to implement projects of this size successfully and on schedule. It was not just our outstanding technology that won over BYD, but also our experience in Hungary, where we have already completed a number of projects,” explains Dr. Lars Friedrich, Head of the Application Technology division at Dürr. This is the first order the company has received from the Chinese carmaker in the passenger car segment. Dürr Systems AG was successfully audited extensively by BYD before being considered as a supplier.
Latest robot generation for painting process
The painting lines will use Dürr’s latest EcoRP series painting robot, available in both six- and seven-axis variants for interior and exterior painting. The seven-axis robot offers high precision and flexibility for interior painting, reaching even the most difficult to access areas. Six-axis robots will handle exterior painting. The scope of supply also includes the corresponding door, lid, and flap openers as additional aids for the painting process.
Sustainable paint application
EcoBell3 high-speed rotary atomizers ensure flawless painting quality with uniform shade, flow, and layer thickness. When combined with the associated cleaning equipment and color change technology, the atomizer family minimizes paint and solvent consumption and enables fast color changes within the cycle time. In the future, BYD will also be able to sustainably implement customers' special color requests using Dürr's standardized, modular EcoSupply P paint supply system with pigging technology. The ”pigs” – which are what the fitting bodies matched exactly to the internal diameter of the hoses are called – push paint to the color changer and return any leftover paint back into the paint container, leaving absolutely no trace of residue and eliminating the need for cleaning. This process reduces both paint and the rinsing agent consumption, benefiting both budget and the environment.
Automated body cleaning
The supply scope also includes cleaning robots that remove dust and dirt particles from the bodies before painting. Flexible-action feather rollers clean different body shapes efficiently and independently of each other in nearly any combination and order – ideal for BYD’s various NEV types.
About Dürr
The Dürr Group has been established in the United States since 1970 and currently employs approximately 1,400 people. From the Campus with a state-of-art validation, testing, and training center in Southfield, MI, Dürr USA represents four of the five divisions. Paint and Final Assembly Systems offers equipment for painting and assembly processes, while Application Technology provides paint, sealants and adhesives application systems. Dürr’s Clean Technology Systems division is leading in air pollution control, noise abatement systems, and battery electrode coating lines. Dürr has three locations in the US: Dürr Systems, Inc. in Southfield, MI, and De Pere, WI; Durr Universal, Inc. in Stoughton, WI. The subsidiary Schenck USA Corp., with headquarters in Deer Park, NY, and additional locations in Hudson, MA, and Southfield, MI, offers balancing machines, vibration and condition monitoring systems, spin testing and services for the aerospace, automotive and general industry. The customers of Dürr USA include automotive and commercial vehicle manufacturers, as well as their suppliers, and a diverse group of other industries like the chemical or wood industry. HOMAG Machinery North America operates the production facilities for HOMAG Group in Grand Rapids, MI, which is also the base for the sales and service company Stiles Machinery Inc. The HOMAG Group produces machinery and equipment for the woodworking industry.
The Dürr Group is one of the world's leading mechanical and plant engineering firms with particular expertise in the technology fields of automation, digitalization, and energy efficiency. Its products, systems, and services enable highly efficient and sustainable manufacturing processes – mainly in the automotive industry and for producers of furniture and timber houses, but also in sectors such as the chemical and pharmaceutical industries, medical devices, electrical engineering, and battery production. In 2023, the company generated sales of €4.6 billion. The Dürr Group has around 20,000 employees and 141 business locations in 33 countries. As of January 1, 2025, the former divisions Paint and Final Assembly Systems and Application Technology were merged to form the new Automotive division. Since then, the Dürr Group has been operating in the market with four divisions:
Automotive: painting technology, final assembly, testing and filling technology
Industrial Automation: automated assembly and test systems for automotive components, medical devices, and consumer goods as well as balancing technology solutions and coating systems for battery electrodes
Woodworking: machinery and equipment for the woodworking industry
Clean Technology Systems Environmental: air pollution control and noise abatement systems
Comments (0)
This post does not have any comments. Be the first to leave a comment below.
Featured Product
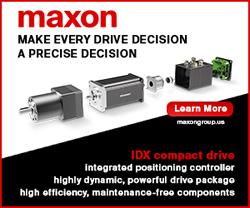