Placing coins into a coin presentation case insert sounds like an easy thing to do, right? But when the application calls for placing several thousand coins in exact places on moving inserts every day, the task becomes much more demanding.
Farason Corporation Chooses Dorner Conveyors to Integrate with its Robotic Machine to Successfully Assemble Coin Proof Sets
Contributed by | Dorner Mfg. Corp.
Placing coins into a coin presentation case insert sounds like an easy thing to do, right? But when the application calls for placing several thousand coins in exact places on moving inserts every day, the task becomes much more demanding.
This was the challenge facing engineers at Coatesville, Pennsylvania-based Farason Corporation. Its customer was looking for an effective way to place and package commemorative coin proof sets. The answer proved to be an integration of vision-guided robots, along with precision conveyors supplied by Dorner Mfg. (www.dornerconveyors.com)
Farason Corporation (www.farason.com) specializes in the design and build of custom machinery and systems to perform assembly, manufacturing and packaging processes. The company has expertise in numerous industries, including cosmetics, food and confections, medical, pharmaceutical, manufacturing and others. For this application, the job involved picking and orientating coins for placement into coin presentation case inserts, and then assembling the inserts with the remaining presentation case top and bottom lens.
Buying and trading commemorative coin proof sets are a popular hobby in the United States. A large part of the appeal for collectors is not only the precise level of detail found in coins, but the overall presentation of the packaging as well. Coin proof sets are billed as premium items that can increase in value over time, so it’s important that the integrity of the coins and packaging is preserved during processing.
“Our challenge was to take the various coins, and place them into the inserts, and in turn take the inserts and place them into the plastic outer shell,” said Joe Hurley, president, Farason Corporation. “The best way to accomplish this is through the use of robotics.”
The entire machine system uses 13 vision-guided robots and 22 Dorner conveyors, which were purchased from Doylestown, Pennsylvania-based Stokes Material Handling Systems, Inc. (www.stokesmhs.com). During the initial in-feeding process, coins are housed in trays as they enter the machine to be indexed for picking. Since the machine is capable of processing a coin presentation case containing six different coin types, six Dorner 2200 Series conveyors are required to feed stacks of trays containing the six different coins, to the tray unloading robots.
Next, the two tray unloading robots remove rows of coins from their respective trays and then place them onto one of six, two-inch wide, servo-driven Dorner timing belt conveyors. Each conveyor is responsible for indexing its respective coins to a downstream location where a camera takes a picture of the coin to determine its rotational orientation. Additionally, each conveyor is paired with a coin placing robot, which then picks the coin and places it, properly orientated, within a coin insert well. After the tray unloading robots have fully depleted a tray of its coins, they pick the empty trays and place them onto one of six Dorner 2200 Series conveyors for transfer out of the machine.
As part of the upstream operations, a robot picks the coin inserts from a stack, presents them to a camera to inspect for smudges, scratches and other imperfections, and then places them onto a 10-inch wide Dorner 3200 Series conveyor. The purpose of this conveyor is to transfer the coin inserts past the six coin placing robots.
Completed coin inserts are picked by a flipper robot and placed into a device that flips the insert 180 degrees, which is the orientation required for downstream assembly operations. While in the flipping fixture, top and bottom cameras inspect the insert to ensure all coins are present and properly orientated.
If a coin insert is deemed a good part, the presentation case top-lens robot will pick a top lens from a stack, present it to the camera for inspection and then place it down onto the downstream Dorner 3200 Series conveyor. The top lens receives the good part coin insert from the flipper robot. The purpose of this conveyor is to transfer the good part coin insert to the remainder of the presentation case assembly operations. Subsequently, the presentation case bottom-lens robot picks a bottom lens from a stack, and if it passes inspection places it down onto the top lens/coin insert partial assembly. This assembly is then pressed together prior to transferring to the trolley loading robot, which picks the finished assemblies, in a three-up operation, and places them into the trolley for downstream operation.
The 2200 and 3200 Series belt conveyor are ideal for lightweight to heavyweight industrial applications like the one with Farason because it features a low profile design and can move with precision at low speeds. The conveyors also work well with robotics and indexing applications as they are easily programmable to work a variety of drive and control options to fully integrate into a larger system. All Dorner conveyors are made to order to exact customer specifications.
It took about a year from initial specification to delivery for Farason to complete the machine, which was commissioned to its customer in April. Farason has built other coin picking systems for customers, and has used Dorner for all support conveyors.
“We do a lot of work with Dorner and have developed a relationship with them through the years,” Hurley said. “Our systems call for precision when working with robotics, and we need that same level of precise movements in our supporting conveyor systems. Our track record with them has been positive, and that’s why we keep buying Dorner.”
The content & opinions in this article are the author’s and do not necessarily represent the views of RoboticsTomorrow
Comments (0)
This post does not have any comments. Be the first to leave a comment below.
Featured Product
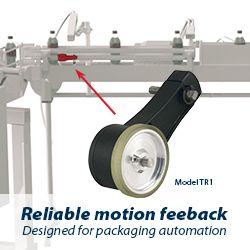