How will the drive actually behave in the real-life application? For brushless DC-motors from FAULHABER, this question can be answered without any hardware whatsoever.
Testing drive systems virtually - Simulink library for development and digital twin.
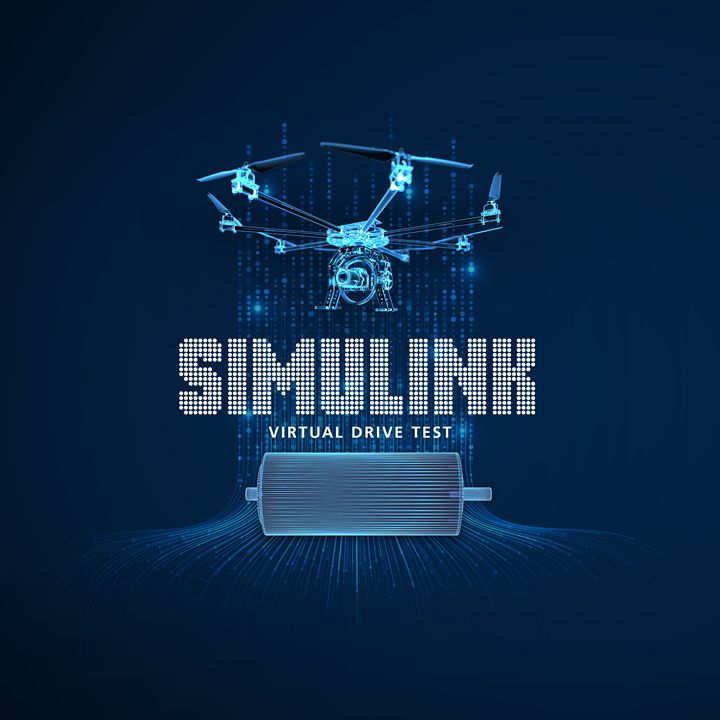
Article from | FAULHABER
How will the drive actually behave in the real-life application? For brushless DC-motors from FAULHABER, this question can be answered without any hardware whatsoever. They were recently added as virtual modules to a library and can be integrated into modeled applications using the simulation software Simulink. The simulated behavior serves as an indicator for the real-life situation. It takes just a few clicks to "try out" different drives. This makes the development process much easier.
Let us take a transport drone used in logistics as an example. Its drives need to meet high dynamic demands to enable precise and responsive control of the flying object. They must respond without perceivable delay, smoothly and with precisely defined force. Motors that drive such high-precision applications therefore have to meet very high expectations.
Saves time and reduces risks
The transport drone is just one of many application examples for which simulation of the drive system during the development phase constitutes a valuable tool. What matters here is not only the behavior of the motor, which can be modeled with reasonable effort based on the data sheet parameters. A complete drive system also requires emulation of the sensor system and control. Realistic emulation of these components helps reduce comprehensive trials with physical drives.
Integrating sensor system and control
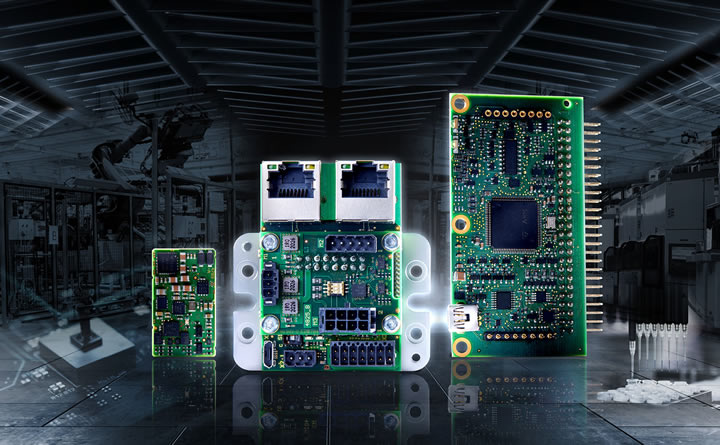
For simulation of a controlled drive system with FAULHABER components, the library provides modules for torque, speed and motion control. Motion Controllers of generation 3.0, which include e.g. the models MC 3001, MC 3603 and MC 5005, form the basis. In combination with a motor from the library and a configurable load inertia, the same controller parameters can be determined as those that exist in a physical Motion Controller. By simulating the complete drive system, it is possible to, for example, establish realistic positioning times, adapt the controller parameters or compare the behavior of the drive when different concepts are applied.
Practical toolbox
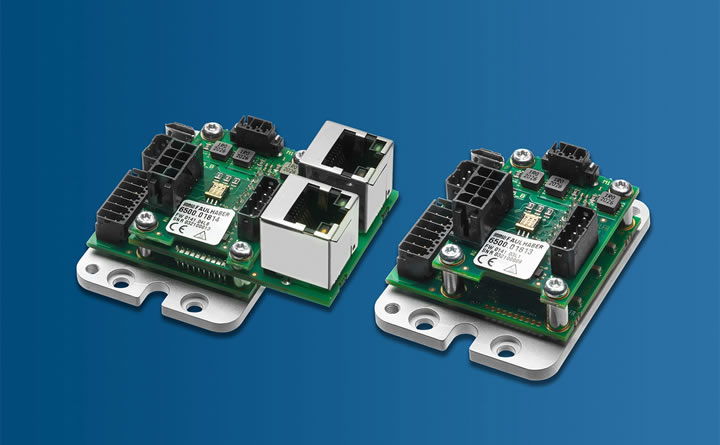
The content & opinions in this article are the author’s and do not necessarily represent the views of RoboticsTomorrow
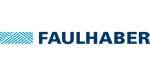
FAULHABER MICROMO
Since 1961, FAULHABER MICROMO has partnered with OEMs to deliver high precision, high performance, custom micro motion system solutions to markets such as medical, robotics and automation in North America. FAULHABER MICROMO's tradition of innovation started decades ago in Germany. The groundbreaking invention of the FAULHABER coreless winding started it all for a market that produces millions of motors today. How can the FAULHABER MICROMO team help you deliver your next innovation to market first? Learn more about MICROMO's solutions for the most demanding applications, our diverse motion products and technologies, online ordering, Engineering and R&D teams, Clean Room Assembly, Machining Center and other services at our Clearwater, FL facility at https://www.faulhaber.com.
Other Articles
Walking naturally with artificial foot
At least 60 million strokes
DC microdrives bring dynamics into handling
More about FAULHABER MICROMO
Comments (0)
This post does not have any comments. Be the first to leave a comment below.
Featured Product
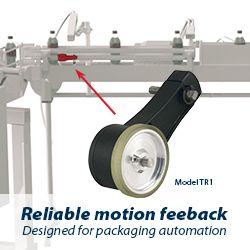