Ball Joint Module makes service robots mobile.
Featuring -170 to +170° angle of rotation and 2 integrated servo axes that can each achieve 35-64 Nm torque, SPB Powerball can be used to implement lightweight arms, service robots, and other handling applications
November 18, 2011 - Featuring -170 to +170° angle of rotation and 2 integrated servo axes that can each achieve 35-64 Nm torque, SPB Powerball can be used to implement lightweight arms, service robots, and other handling applications. Integrated control and regulation electronics and 24 Vdc power supply provide basis for decentralized and mobile applications. With integrated intelligence, universal CAN communication interface, and cable technology, module can be integrated into existing control concepts.
SCHUNK has expanded its modular robotics range with the SPB Powerball. For the first time ever, the movements of two axes are combined in a single, compact module that provides high torques, and can be used to implement compact lightweight arms, service robots, and other handling applications with a modular structure.
In the past, two rotary modules had to be combined for movements with two degrees of freedom, but now the Powerball is sufficient. For example, an individual lightweight arm can be configured with six degrees of freedom using only three Powerball SPB modules, which saves space. The ball joint module also paves the way for modern handling concepts.
The two integrated servo axes can each achieve torques between 35 and 64 Nm. With its angle of rotation between -170 and + 170°, the module is capable of flexible operating cycles. Position, speed, and torque can be adjusted flexibly. Using a quick-change system and plug connectors with integrated signal transmission, it can be put into operation quickly and easily without sophisticated cabling by using the Plug&Play method.
Its integrated control and regulation electronics and power supply with 24 V direct current, provide the ideal basis for decentralized and mobile applications. The SPB Powerball is fully integrated in SCHUNK's modular robotics range. Due to integrated intelligence, universal CAN communication interface, and cable technology for data transmission and power supply, the modules can be easily integrated into existing control concepts. Even complex systems and robot structures with several degrees of freedom can be implemented with minimal design and programming costs. The "Viro-Con" configurator can be used to configure a complete system of individual modules at the PC and check its suitability for the selected task.
Featured Product
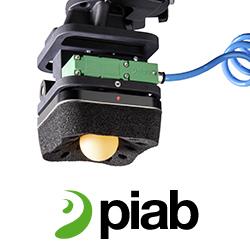