ABB announces EDP300 series digital valve positioner
ABB announces the EDP300 series digital positioner for regulating air-driven linear and rotary actuators, including control valves.
ABB announces the EDP300 series digital positioner for regulating air-driven linear and rotary actuators, including control valves. The EDP300 design incorporates an advanced algorithm to precisely position the valve actuator with accuracy and speed. It also offers ABB's HMI (Human Machine Interface) with menu-driven programming and control selection of options, saving time and cost.
EDP300 diagnostics include optional pressure sensors to determine valve/actuator performance, allowing engineers to monitor actuator conditions in real-time and improving process reliability. The unit also incorporates a Partial Stroke Test (PST) function for in-process verification of valve integrity. With an integrated valve signature function, testing and verification of actuator and positioner assembly baseline performance can be performed without the need for additional hardware.
The pneumatic output control stage of the EDP300 provides up to 23 scfm air capacity for fast valve travel, eliminating the need for volume boosters. Supply pressures up to 145 psi deliver unsurpassed valve seating load.
Designed with a high degree of mounting flexibility, the EDP300 has application options for linear or rotary actuators with the same footprint as the ABB TZIDC positioner. An optional stainless steel housing permits the EDP300 to operate in corrosive environments typically found in chemical, pulp & paper, and offshore applications.
ABB is a leader in power and automation technologies that enable utility and industry customers to improve performance while lowering environmental impact. The ABB Group of companies operates in around 100 countries and employs about 130,000 people.
Featured Product
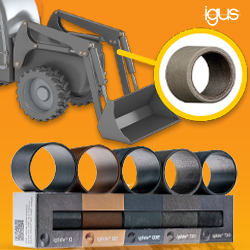
igus® - Free heavy-duty plastic bearings sample box
The iglide® heavy-duty sample box provides a selection of five unique iglide bearings, each suitable for use in heavy-duty equipment due to their self-lubricating, dirt-resistant properties. Each bearing material boasts unique benefits and is best suited for different application conditions, though each can withstand surface pressures of at least 11,603 psi at 68°F.