STRATASYS AND WORRELL ACCELERATE MEDICAL DEVICE DEVELOPMENT with 3D printed injection molds
Since 3D printing injection molds for medical devices, Worrell slashes lead times by a game-changing 95% in comparison to traditional tooling, with costs plummeting 70%
Minneapolis, MN; Rehovot, Israel - October 30, 2014 - Stratasys Ltd. (Nasdaq:SSYS), a leading global provider of 3D printing and additive manufacturing solutions, today announced its collaboration with design and product development company, Worrell, to accelerate medical device development through the use of 3D printed injection molding (which Worrell refers to as "3D IM"). Since 3D printing injection mold tools for medical devices, the company is producing injection molded prototypes using final production materials in 95% less time and at 70% less cost compared with traditional aluminium molds.
In a bid to promote the significant cost savings of 3D printed injection molds for medical device manufacturers, as well as the huge reductions in product development cycles, Stratasys and Worrell will jointly attend international tradeshows and host a series of workshops to educate the medical industry on the innovative process and its radical impact on manufacturing.
"We have recognized a significant under-utilization of the 3D printed injection molding process in medical device development and were working with Worrell to help fill this gap," says Nadav Sella, Senior Manager of Manufacturing Tools at Stratasys. "Worrell is a leading design firm with the expertise and infrastructure necessary to integrate injection molding and 3D printing within the product development cycle. In an industry where products have the potential to save lives, we want to use this collaboration to demonstrate how medical device manufacturers can bring their products to market significantly faster than ever before."
Medical device manufacturers traditionally face two main obstacles in getting medical devices to market: tooling costs and the FDA regulatory process. Traditional tooling is both costly and time-consuming, as new molds must be created every time a prototype is refined before manufacturing. To reduce potential iteration risks and tooling costs, Worrell uses Stratasys PolyJet-based 3D printers to create injection molding tools and then inject the same materials that will be used in a finished medical device, creating higher-fidelity prototypes.
"We were recently approached by medical device start-up, MedTG, to design and engineer a dual-flow needleless blood collection system that reduced the need for multiple injections, thereby increasing patient comfort and hospital efficiency. Utilizing 3D printed injection molds to prototype the device, we were able to reduce the costs associated with traditional tooling by approximately 70%, as well as cutting times by 95%," explains Kai Worrell, CEO at Worrell.
Worrell concludes, "Using 3D printed injection molds, we are able to create a prototype for a fraction of the cost and in a matter of days compared to the eight-week lead time associated with traditional tooling processes. This revolutionary manufacturing process enabled by Stratasys PolyJet technology is now an integral part of our product development cycle, allowing us to provide better prototypes for care providers, while saving our clients considerable time and money."
Featured Product
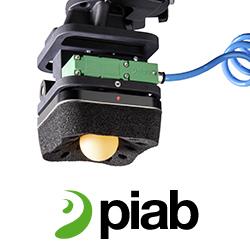