Microscan Introduces EtherNet/IP™ for the World's Smallest Machine Vision Smart Camera
Microscan, a global technology leader in barcode, machine vision, and lighting solutions, announces the availability of EtherNet/IP™ communication on its ultra-compact machine vision smart camera, Vision MINI Xi.
RENTON, WA, November 6, 2014 - Microscan, a global technology leader in barcode, machine vision, and lighting solutions, announces the availability of EtherNet/IP™ communication on its ultra-compact machine vision smart camera, Vision MINI Xi. One of several cameras in Microscan's award-winning AutoVISION® machine vision product suite, the Vision MINI Xi offers a complete machine vision tool set for high-speed identification, inspection, and other automated tasks with the optimal size and shape for space-constrained machines.
With the release of the Vision MINI Xi Smart Camera in March, Microscan introduced industrial Ethernet TCP/IP to its miniature smart camera line, enabling integration with machines designed for Ethernet connectivity. With the release of AutoVISION 3.0.2 software, the Vision MINI Xi now supports communication via EtherNet/IP for use in industrial environments. To install Vision MINI Xi within a networked automation system, users can rely on AutoVISION's built-in EtherNet/IP support and one-click connectivity tool, Microscan Link, to connect machine vision tools, inspection values, and settings from the camera to PLCs and other control systems.
Compared to RS-232 (also supported by Vision MINI Xi), fully-integrated Ethernet in machine vision smart cameras offers several unique advantages in the communication of data from the camera to other machines networked on a line. The first advantage is speed: as devices are required to capture and store high-resolution images, Ethernet offers data transmission over high-speed connections without impacting production speeds. An Ethernet system can also span longer physical distances without losing transmission speed, using point-to-point connectivity over Ethernet hubs and allowing manufacturers to remove control systems and PCs from the floor and co-locate them in a controlled environment. This remote device management allows tasks on the smart camera to be controlled from anywhere a network connection is available. A process engineer can, for instance, troubleshoot an MES without leaving the office. The engineer can also save integration time and cost with Ethernet devices that enable native integration with MES and ERP systems, which are network-based and communicate over Ethernet. Finally, the growing use of Ethernet as the common data transmission protocol in computers and workplaces allows data to be collected at more points throughout the manufacturing process. One network interface card (NIC) in a single computer can connect to a nearly unlimited number of Ethernet devices with independently addressable connections. This allows more tasks to be performed in parallel, improving productivity and cycle time.
The AutoVISION family includes several options for networking systems over EtherNet/IP, from the Vision HAWK Smart Camera with integrated liquid lens and the Vision HAWK C-Mount Smart Camera (both featuring EtherNet/IP and PROFINET I/O support), to the updated Vision MINI Xi Smart Camera. Manufacturers can look to the Vision MINI Xi for the smallest footprint in networked machine vision for embedded and close-range applications. Measuring 1 in. (25.4 mm) x 1.8 in. (45.7 mm) x 2.1 in. (53.3 mm) and weighing 3.2 oz. (91 g), Vision MINI Xi is the world's smallest Ethernet-enabled smart camera for inspection, color matching, symbol decoding, OCR, and other vision capabilities. Vision MINI Xi also features corner-exit cabling for flexible mounting, serial connectivity, a 24-volt interface, and optically isolated I/O in one compact package.
Vision MINI Xi is the ideal solution for manufacturers working in limited integration environments who require Ethernet speed and connectivity as well as the flexibility to expand to advanced inspection tasks if necessary, all with a single device. All AutoVISION hardware and software offers unique scalability and job portability to change cameras without switching software or inspection jobs. Users can also upgrade to Microscan's advanced Visionscape® software without switching cameras. With AutoVISION and the Vision MINI Xi Smart Camera, manufacturers can incorporate powerful machine vision inspection into virtually any environment to meet a range of dynamic requirements.
For more information on Microscan's new Vision MINI Xi Smart Camera visit www.microscan.com.
About Microscan
Microscan is a global leader in technology for precision data acquisition and control solutions serving a wide range of automation and OEM applications. Founded in 1982, Microscan has a strong history of technology innovation that includes the invention of the first laser diode barcode scanner and the 2D symbology, Data Matrix. Today, Microscan remains a technology leader in automatic identification and machine vision with extensive solutions for tracking, traceability, and inspection, ranging from basic barcode reading to complex machine vision inspection, identification, and measurement.
As an ISO 9001:2008 certified company recognized for quality leadership in the U.S., Microscan is known and trusted by customers worldwide as a provider of quality, high precision products. Microscan is a Spectris company.
Microscan Contact
Corporate Headquarters, U.S.
Shaina Warner, Marketing Specialist
+1 425.203.4963; swarner@microscan.com
###
Featured Product
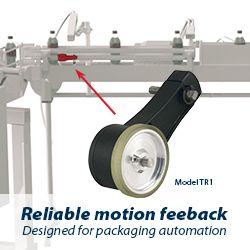