Humanistic Robotics Teams up with DARPA to Elevate Safety at the Robotics Challenge Finals
Wireless Emergency Stop Technology Now Required for all Challenge Entries
PHILADELPHIA--Humanistic Robotics, Inc. (HRI), a robotics and technology innovator dedicated to making the world safer through engineering and design, has teamed up with the Defense Advanced Research Projects Agency (DARPA) to heighten the safety at the final "showdown" of the DARPA Robotics Finals, June 5-6, 2015. All twenty-five finalists are required to integrate HRI's Wireless Emergency Stop and companion technology into their robots, a challenge protocol that will maximize safety and minimize damage in the case of unforeseen malfunctions. The Wireless E-Stop utilizes HRI's proprietary SafetySense technology to create a safe and reliable wireless link for controlling advanced machines remotely.
"These contestants are as advanced as they come in the engineering world. The machines they design represent the next generation of robotics - they aren't in this just for fun, they are in this to innovate technology that will change the world," said Josh Koplin, Co-Founder, HRI. "Requiring our Wireless E-Stop isn't just meant to increase the safety at the Challenge event. We see it as a way to demonstrate to spectators and the general public that robots are going to increasingly impact their lives in a really positive way, and a lot of us are working to ensure that this innovation happens safely and robots can become tools people can trust."
As machines in all industries become more capable and intelligent, HRI is developing wireless systems to ensure the safety and productivity of human-machine teams. HRI products such as the Wireless E-Stop utilize industry-leading safety methodologies including SafetySense®, a proprietary design strategy included in all of HRIs robotics products.
HRIs Wireless E-Stop provides immediate intervention to prevent unsafe conditions before they develop, while the hand-held device also allows anyone to intervene in the operation of a machine from wherever they are. Unlike other emergency stop technologies, the HRI Wireless E-Stop utilizes two-way constant communications and extremely stringent monitoring of the wireless link on the machine side, as well as dual output emergency stop signals. The end result is a truly reliable wireless connection thats always available to stop the machine if you need it.
"The HRI Wireless E-Stop is an evolved, sophisticated tool thats indispensable for the advanced operations we run," said Daniel Lee, University of Pennsylvania Engineering Professor, and DARPA Challenge participant. Dan has been working with HRI for years as Director of Penn's GRASP (General Robotics Automation, Sensing, Perception) Lab, and continued: "We were the first to purchase HRIs wireless product and this E-Stop demonstrates emergency technology that has advanced right alongside the growth of robotics. As engineers get more bold in their designs, functions and capabilities, the Wireless E-Stop assures safety protocol at the same advanced levels."
While the use of the HRI Wireless E-Stop technology is mandatory for all DARPA Robotic Challenge finalists, DARPA has purposefully left it flexible on how the teams utilize it. Engineers can do anything from utilizing the hand-held stop device as a stand-alone element, to expertly integrating the emergency stop technology and software into their robots.
"HRI is extremely proud to provide DARPA this technology for this prestigious competition," said Samuel Reeves, Co-Founder and CEO, HRI. "Still, the need for quick stopping often arises. If and when that occurs, the contestants can be sure that when they hit our Wireless E-Stop button, their machine will stop."
More information on HRI, the HRI Wireless Emergency Stop and SafetySense is available at HumanisticRobotics.com.
Featured Product
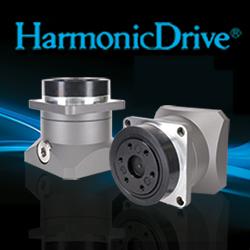