OCTOPUZ v1.4 Release - What's New?
It's here! The newest version of OCTOPUZ brings with it upgraded capabilities that include support and functionality for welding with multiple robot brands. This OCTOPUZ release boosts the software's versatility and efficiency, solidly positioning it as the ideal solution for any robotics challenge. What's new?
What's new in OCTOPUZ V1.4?
It's here! The newest version of OCTOPUZ brings with it upgraded capabilities that include support and functionality for welding with multiple robot brands.
The new release includes:
- An automatic updater that will keep the software up to date, and let you download and install add-ons and tutorials
- Saved file size improved
- New settings interface for intuitive changes• Welding interface updated with new, cleaner GUI, new wording, and a 3D interactive window showing the weld and how the parameters affect it
- New welding support and functionality, including additions to touch-sensing
- 3D touch-sensing supported for Fanuc
- An updated post framework for all robot brands (KUKA, Fanuc, Motoman, ABB, etc) as well as new Stäubli posts for versions 6.9.1 and 7.6.4 and updates to OTC and Kuka.CNC posts
- Reference points (path correction/issue avoidance) reapplied when reimporting paths from CAM
- CAM import speed improvements
- Rotary Auto Positioner has rotary speed limits used in calculations
- All Mastercam tooling types supported
- Shifting paths improved
- Frames (base and tool) better supported for accurate simulation
Behind the scenes, the latest version of OCTOPUZ has undergone revisions designed to optimize performance by installing a new software engine, updating the installer and adding an XML-based configuration utility. These changes boost the softwares versatility and efficiency, solidly positioning it as the ideal solution for any robotics challenge.
OCTOPUZ is the intelligent offline robot programming and simulation software created by In-House Solutions. Ideal for any path-sensitive application, the software allows for offline start-to-finish programming and simulation, cuts path generation time by at least 50 percent and allows users to program multiple robots simultaneously without impacting production time. OCTOPUZ is compatible with as many as 19 robot brands, offers full customization and comes with extensive support before, during and after each sale through training, software assistance and cell programming.
To learn more about the OCTOPUZ new release or to arrange for a personalized demonstration, visit www.octopuz.com, call 1-800-529-5517 or email info@octopuz.com
About OCTOPUZ
OCTOPUZ is an intelligent offline robot programming and simulation software ideal for any path-sensitive application. Created by In-House Solutions, the company took a revolutionary approach by combining the offline programming of robots with a manufacturing process simulation. Today, OCTOPUZ provides a mainstream, versatile, powerful and effective solution for any robotic challenge.
About In-House Solutions
More than 27 years ago, In-House Solutions began reselling and developing powerful software tools accessible to small- and medium-sized manufacturers. Today, the company provides CAD/CAM, DNC, PCMM and OCTOPUZ robotic programming software solutions to organizations of all sizes. The In-House Solutions team of experts, with offices in the U.S., Canada and Germany, are dedicated to selling, supporting, developing and implementing a full spectrum of software tools, particularly those specializing in NC programming and optimization, shop floor DNC communications and offline programming of industrial robots. In-House Solutions is the Canadian Mastercam distributor, and OCTOPUZ completes the companys software solutions for manufacturing.
Featured Product
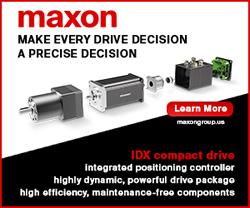
The maxon IDX Compact Drive with Integrated Positioning Controller
The compact brushless EC-i motor combined with an EPOS4 positioning controller delivers a highly dynamic, powerful drive package with field-oriented control (FOC), high efficiency, and maintenance-free components in a high-quality industrial housing. The maxon IDX drives are suitable for use across the entire speed range (from standstill to maximum speed) and have an extremely high overload capability. Together with a positioning controller, the integrated sensor (single turn) enables absolute positioning.