FANUC America Demonstrates Seamless Integration of its CNC, Robotics and ROBOMACHINE Products at the Automation Fair Event
Automation Fair event, hosted by Rockwell Automation, Nov. 18-19, in Chicago.
ROCHESTER HILLS, Mich.--FANUC America Corporation, the leading supplier of factory automation, will highlight the seamless integration of its CNC, Robotics and ROBOMACHINE products at the Automation Fair event, hosted by Rockwell Automation, Nov. 18-19, in Chicago, booth #1351.
"Companies are continuously searching out the latest manufacturing technologies that will help them drive future growth, innovation and profitability," said Rick Schneider, president and CEO, FANUC America. "Our demonstrations present reliable, practical and easy-to-use automation designed to help both large and small manufacturers improve quality, increase throughput and reduce production costs."
FANUC will feature the following product demonstrations at the Automation Fair event:
A demonstration highlighting the ease of use of FANUCs products will feature the α-D21SiA5 ROBODRILL tended by an LR Mate 200iD robot. As a video presentation shows the easy setup of the robot and ROBODRILL system, a special gift will be manufactured for each visitor. The robot and ROBODRILL will be connected to a Rockwell Automation programmable automation controller (Logix PLC) for high-level monitoring and data collection.
A "One FANUC" System will highlight the seamless integration of FANUCs products and connectivity with Rockwell Automation and Cisco technologies. First, a FANUC CR-35iA collaborative robot equipped with an iRVision 3D Area Sensor will pick part blanks and place them on a part station. Next, a GUDEL Gantry controlled by the FANUC Power Motion i-Model A will transfer parts between two FANUC α-D21SiA5 ROBODRILLs, each tended by an LR Mate200iD robot. Finished parts will be distributed to visitors.
"The system underscores the importance of scalable technologies that can adjust to our customers changing production needs," said Schneider.
Zero Down Time (ZDT) is FANUC's cloud-based application designed to virtually eliminate unexpected production downtime. ZDT collects and analyzes critical information about a robot's mechanical, maintenance and process health and alerts customers of potential product, system or process issues so action can be taken before unexpected downtime occurs. ZDT also provides customers with Smart Maintenance notifications, optimizes performance and enhances FANUCs world-class technical support services.
The demonstration uses a network built with Allen-Bradley Stratix Ethernet switches to connect all robots in the FANUC booth to a Cisco Unified Computing System (UCS) that runs FANUCs ZDT Data Collection software. Data collected from the robots is sent live over the internet to Cisco and FANUCs cloud-based ZDT Data Center where it is stored and analyzed. A large monitor in the booth will be logged into FANUCs ZDT Web Portal where visitors will be able to see the state of all robots in the FANUC booth. Meanwhile, an LR Mate 200iD set up in a simulated production application next to the monitor will be used to demonstrate how ZDT can detect and prevent an issue from causing unexpected downtime.
An education demonstration will feature FANUCs Certified Education Training (CERT) for robotics and CNC, and a CNC Simulator. Products will be connected to a Rockwell Automation HMI visualization screen to display system status.
"As manufacturing evolves and processes become more connected, theres an increasing need for workers with higher levels of computer science and engineering skills," said Schneider. "Our education programs are aligned with STEM initiatives that prepare the next generation of manufacturing talent."
In addition, FANUC will demonstrate two Rockwell Automation manufacturing intelligence applications using FactoryTalk VantagePoint and FactoryTalk View.
The first is a real-world example of FactoryTalk View visualization software. This interactive system will deliver live data and video feeds from FANUCs sheet metal factory in Japan, allowing users to monitor the overall factory floor status as well as drilling down to view individual cell or machine status. Live video feeds will be presented using a large, user-friendly touch screen monitor.
The second demonstration combines FANUCs MT-LINKi and OPC Server data collection tools and FactoryTalk Vantage Point as the host application to deliver live CNC machine data from three FANUC machining demonstrations. Data will be presented in a customized dashboard via a large monitor as well as local mobile devices. The FactoryTalk Vantage Point dashboard allows users to make informed decisions to improve production operations based on the live data of "smart assets."
About FANUC America Corporation
FANUC America Corporation is a subsidiary of FANUC CORPORATION in Japan, and provides industry-leading robotics, CNC systems, and factory automation. FANUCs innovative technologies and proven expertise help manufacturers in the Americas maximize efficiency, reliability and profitability.
FANUC America is headquartered at 3900 W. Hamlin Road, Rochester Hills, MI 48309, and has facilities in: Atlanta; Boston; Charlotte; Chicago; Cincinnati; Cleveland; Dallas; Indianapolis; Los Angeles; Minneapolis; Montreal; Pine Brook, NJ; San Francisco; Toronto; Buenos Aires, Argentina; Sao Paulo, Brazil; and Aguascalientes, and Mexico City, Mexico. For more information, please call: 888-FANUC-US (888-326-8287) or visit our website: www.fanucamerica.com. Also, connect with us on YouTube, Twitter, Facebook, Google+ and LinkedIn.
Featured Product
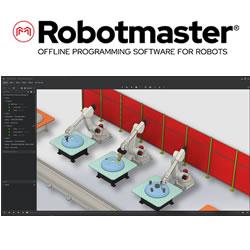
Robotmaster® 2024
Program multi-robot cells and automatically solve robotic errors with ease. Hypertherm Associates announces a new version to its robotic programming software. Robotmaster 2024 addresses key market trends including the support for programming multiple robots in a single work cell and the demand for automatic trajectory optimization and robotic error correction.